-
Posts
4,457 -
Joined
-
Last visited
-
Days Won
3
Bandsaw Steve last won the day on July 18 2022
Bandsaw Steve had the most liked content!
About Bandsaw Steve
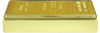
Profile Information
-
Gender
Male
-
Location
Western Australia
-
Interests
Aviation, History, WW2, painting, modelling
Recent Profile Visitors
14,562 profile views
Bandsaw Steve's Achievements

Very Obsessed Member (5/9)
11.8k
Reputation
-
Wingnut Wings De Havilland DH-9A Ninak 1/32
Bandsaw Steve replied to Elias's topic in Ready for Inspection - Aircraft
What an absolute ripper! -
See if you can find a local print shop that does lithographic printing. Thin Aluminium sheet is a waste product. They might sell it to you for very little. it’s extremely useful in model building
-
What fantastic-looking aircraft these were. 👍
-
That’s looking fantastic!
-
Cripes! Imagine what we could achieve if I knew something!
-
"Hollywood MiGs" list?
Bandsaw Steve replied to Andrew D Jolly Rogers guy's topic in Aircraft Cold War
I seem to recall a story I once read about some bubble-too P-47s posing as ‘Yaks’ in a film about the Berlin airlift. Perhaps this might prompt some more details from someone more familiar with the matter. -
Embraer E-190 - Alliance Airlines **Finished**
Bandsaw Steve replied to Romeo Alpha Yankee's topic in Give Peace A Chance GB
Great job. An attractive aircraft type in a lovely colour-scheme. -
Is there going to be a poll on this one? I want to vote for ‘Alliance Airlines’ 😀
-
Australia and New Zealand group build part II - Chat
Bandsaw Steve replied to Corsairfoxfouruncle's topic in ANZAC 2 GB
Hello my fellow ANZAC enthusiasts, Unfortunately my earlier stated intention of scratch-building a RAN S2 Tracker as part of this GB is no longer possible. Between work and travel commitments I don’t have sufficient time to tackle this project in this group build. I will however be building one at some point, so if you are interested, keep your eyes peeled on the aviation WIP pages. Although I can’t be an active participant in this group build I remain very interested in it and will be checking in very frequently. Best Regards, Bandsaw Steve -
Hasegawa 1/48 f-104J,grab your sunglasses!
Bandsaw Steve replied to stevej60's topic in Ready for Inspection - Aircraft
Great looking model! Fantastic colour-scheme -
Back when this group m-build was first mooted I chipped in with support saying I had the ‘perfect’ subject for ‘Give Peace a Chance’. As it happens that ‘perfect’ subject was not the one I built as I was not referring to the Ferrari 500 but something much more peaceful than a screaming racing car from the 1950s. All of which is to say; if there is a repeat of this group build then I have a subject ready to go! 👍
-
Ferrari 500, 1/12, Scratchbuild - FINISHED!
Bandsaw Steve replied to Bandsaw Steve's topic in Give Peace A Chance GB
Lessons Learned Building models is a hobby that invites continuous learning. You can spend a lifetime building models and still learn something each time. When I wrap up a project I generally put a few bullet points regarding what I have learned in the RFI post. In this case I can't, because the RFI is in the gallery, so I will put them here instead. Here are the main things that I have learned from building this Ferrari: It takes far more hours of work to build a model than I thought. To finish this project (excluding the display base) took about 2.5x more hours than my initial estimate. I have no actual method to estimate how many hours a project might take. 'Just guessing' and 'using gut feel' completely failed in this case. This might be something I should work on because I seem to take on more projects than I should. The 'spine and ribs' construction method that I used here was highly successful and proved very practical. Sooner or later I should use this method on an aircraft fuselage. MDF (medium density fibreboard) is an exceptionally useful model-building material and I will use it more extensively in future. It is possible to cut very even, clean, convincing panel lines in MDF. These are much better than I have managed in any type of natural wood. Aluminum sheet (in this case 2.2mm thick) is an extremely useful scratchbuilding material that can be shaped very precisely without any specialist tools to create robust model components. I will be using this material much more in the future. Britmodellers are very forgiving folks when it comes to issues of 'accuracy'. I have taken a few short-cuts in this project; I did not spoke the wheels, I put 'racy but incorrect' diagonal grid in the air-scoop and gave this car a tank's hatch for a fuel cap and no-one here seems to have batted an eyelid! This shows a very sensible attitude to thorny issue of 'accuracy'. Accuracy matters greatly to some people and less to others, It's good to accept that variety. Finally, thanks very much to @bianfuxia for coming up with the concept of this group-build and for hosting it with such competence and enthusiasm. Best Regards, Bandsaw Steve.- 90 replies
-
- 7
-
-
-
- Scratchbuild
- wood
-
(and 1 more)
Tagged with:
-
Occasionally while delving around in the ‘very long time ago’ section of BM I find something extraordinary. When that happens I sometimes give the thread a ‘bump’ to the top of the pile. I consider it a community service. 🤣