-
Posts
5,820 -
Joined
-
Last visited
-
Days Won
8
Jamie @ Sovereign Hobbies last won the day on July 29 2023
Jamie @ Sovereign Hobbies had the most liked content!
About Jamie @ Sovereign Hobbies
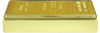
Contact Methods
-
Website URL
http://www.sovereignhobbies.co.uk
Profile Information
-
Gender
Male
-
Location
Aberdeenshire, UK
-
Interests
Constructive feedback on my modelling is welcome
Recent Profile Visitors
Jamie @ Sovereign Hobbies's Achievements

Completely Obsessed Member (6/9)
17k
Reputation
-
Hi Edward, as per Facebook, it would have needed a LOT of model paint sales for it to rival an energy industry technical director career and the income demands on someone in a similar position to yourself (mortgage, children, etc). In truth it was mostly always Bea behind the scenes doing all the work. That was fine when she had the time free, but now she doesn't as she embarks upon a PhD for the nuclear industry, so the time burden of making and packing up paints for sale needs to go.
- 526 replies
-
- 10
-
-
HMS Formidable, Flyhawk, 1941 1/700
Jamie @ Sovereign Hobbies replied to Archelaos's topic in Work in Progress - Maritime
I totally agree. My initial reaction was disappointment at loss of colour, but honestly most wel built models I've seen since with grey bottoms look very attractive indeed. I've actually now swung the other way when drawing these profiles for FlyHawk etc and get disappointed at having to use red!- 60 replies
-
- 1
-
-
Fairmile D - deck colour ?
Jamie @ Sovereign Hobbies replied to Simon Cornes's topic in Maritime WWII
B15 was very blue -
1/700 HMS Howe
Jamie @ Sovereign Hobbies replied to The Naval Guy's topic in Work in Progress - Maritime
- 11 replies
-
- 3
-
-
- Howe
- Battleship
-
(and 1 more)
Tagged with:
-
1/700 HMS Howe
Jamie @ Sovereign Hobbies replied to The Naval Guy's topic in Work in Progress - Maritime
Hmm. Wonder why I never published the 1944 drawings for HMS Anson and Howe. I drew them... Anyway, in 1944, HMS Howe was similar to HMS King George V (as was HMS Anson) except that HMS King George V was the odd one out in using G10 (dark grey) as the darkest shade whereas both HMS Anson and HMS Howe used G5 (virtually black) as the darkest shade. The other 3 colours were the same on all 3 ships though.- 11 replies
-
- 4
-
-
-
- Howe
- Battleship
-
(and 1 more)
Tagged with:
-
HMS Glory - 1:72 scale
Jamie @ Sovereign Hobbies replied to Colin Miller's topic in Work in Progress - Maritime
This is the sort of thing where you will see slight variances in colour depending on mixes, batch, colour of substrate or primer etc etc. It's more when someone paints something an entirely uniform colour that's clearly miles off then claims it's because things varied a bit that people go "Hmm". You could go slightly further and include areas of touch-up on the larger areas of colour. Subtlety is the key, but most ships will have patchiness where the ongoing touchups and partial repaints don't exactly match the older paint. Not unlike car bodywork repairs, in fact. -
Quite interesting details of the white stripe around the top of the mainmast tripod. My old model is incorrect here also.
-
What are your thoughts on RLM 72 and 73?
Jamie @ Sovereign Hobbies replied to Ingo Ritz's topic in Aircraft WWII
I think in hindsight they were poor matches. The previous owner of WEM was in fact colourblind and there wasn't really any QC happening on what arrived from the contractor who made them. The newer batches were rematched against M&K and new formulae saved. In fact, the contractor consolidated their operations a while ago to one facility and their surplus paint machine came here at their suggestion. Only their Technical Manager was actually capable of matching colours properly and despite the brochures mixing machines are inconsistent. They have good days and bad days. Sometimes what comes out is about right. Other times it just isn't. The interesting part is this contractor always has and still makes colour matched paint for other brands. The machine came here and they sell us untinted base in big drums now since moving all operations to the town where the Technical Manager doesn't live. Apparently I'm the only one who ever rejected batches so they knew I wouldn't be happy with what I was getting when it wouldn't be that individual personally making my paints, and hence their proposal was to sell the machine to me for a depreciated price.- 32 replies
-
- 10
-
-
What are your thoughts on RLM 72 and 73?
Jamie @ Sovereign Hobbies replied to Ingo Ritz's topic in Aircraft WWII
That's correct. -
I've finished a model. It's been a couple of years I think since I've managed that. Needless to say I started with high aspirations and became increasingly dissatisfied as time went on. This wasn't helped by cats which have always been around our house and normally cause no trouble like this whatsoever, but this model has been badly damaged twice now. The first time was when almost completed but before I'd added the seatbelts to the ejector seat. I placed it on a shelf where models have been fine for ten years at night before going to bed, and kicked it across the floor in the morning. It was in such a state that it almost went in the bin but my wife persuaded me to sweep up the large number of broken parts and put them upstairs. Even the counter measures pod was broken in half. After a few weeks I put it back together as best I could, but despite my best efforts the tailerons no longer move. About a fortnight ago, after I'd done some oil weathering but still hadn't done those seatbelts, another cat jumped in through an open Velux window and landed on the model sat on my bench and smashed it a second time. Now, well, it goes without saying that I'm dissatisfied with the turnout but given it's been wrecked twice before it was even finished I suppose it's about as good as I can expect. Anyway, it's the Tamiya F-16C kit. The cockpit and engine are Aires resin. Whilst the engine fit fine, the cockpit needed a lot of work to fit and if I built another I wouldn't bother. The GBU-87 cluster bombs are from Eduard Brassin and the AN/ALQ-119 counter measures pod is from ResKit. Paints are obviously my own. Decals are by Elite Decals. I think it has the wrong Heads Up Display for the aircraft I've tried to model but I know very little about jets and if the correct HUD is available out there I don't know what I'm looking for... I copied the load out and took some guidance for subtle weathering from the photograph on this page: https://www.f-16.net/g3/f-16-photos/album38/album87/album85/aas
- 12 replies
-
- 52
-
-
This really is very sad indeed.
-
No Australian stockist anymore?
Jamie @ Sovereign Hobbies replied to sapperastro's topic in Sovereign Hobbies
Thanks Steve, We are thinking of various options. We'd obviously like it to continue in some form and for Model Revival Australia to resume supply into the Australian market. BNA were a stockist back in the WEM days I think but I imagine they have enough on their plate? -
* the very fire Chinese Modelling company *
Jamie @ Sovereign Hobbies replied to 73north's topic in Maritime WWII
With respect you're either ignoring what we're trying to tell you or not understanding what you're reading... Making a kit of Shinano is a big financial risk and based upon other obscure subjects, it probably will not be a good seller. Another thing you quickly learn running a business is that wishlists seldom translate to actual sales. You can click the Like button all you want, but that does not legally obligate people to hand over the money if the kit is actually produced. If you run a business in this industry you will learn that lots of people are happy to write words or click Like or whatever for an obscure product, but they are not so good at actually placing a real order when real money is required. Talk is cheap.