-
Posts
1,114 -
Joined
-
Last visited
About JasonC
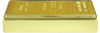
Profile Information
-
Gender
Male
-
Location
Bath, UK
-
Interests
1/48 props, WW2 & onwards.
Occasionally armour.
Recent Profile Visitors
4,850 profile views
JasonC's Achievements

Very Obsessed Member (5/9)
1.2k
Reputation
-
No worries. Which kit are you building? J.
-
For reference:
-
Feedback needed on our Early Mark Spitfires and BF109E Profiles
JasonC replied to WLJayne's topic in Aircraft WWII
The prop shaft is missing.๐ J. -
https://www.reuters.com/world/asia-pacific/britain-end-evacuation-afghanistan-saturday-2021-08-28/ Per Airbus press release, ZM411 was the last UK military aircraft to leave Kabul.
-
Clearly the second solution depends on the construction of the radiator. A FOD screen a la the photo above would help protect even the style you've linked to.
-
The function of such guards is to keep hard debris from directly impacting the radiator matrix. Since the tubes of the latter carry coolant, such impacts risk cracking the cooling tubes and causing a leak. A similar function can be achieved by having the first row of the matrix be solid rather than hollow. Clearly in that case they would have no cooling function!
-
The lower fuel consumption of the new engines offers the potential to cut a mid air refuelling out of some mission profiles. Thatโs a big saving right there; delivering a gallon of fuel at 30,000ft isnโt cheap. J.
-
Correct Colour Schemes for Matchbox's Fw 190A3/4 Decals?
JasonC replied to 3DStewart's topic in Aircraft WWII
Returning to the Eastern Front, Eagalcals (usually quite reliable) sheets EC128 & EC129 show green camouflaged Fw190A-3's. Said aircraft from both JG51 and SchG.1, as per the OP. One supposes that these would have been re-painted rather than factory schemes. Indeed, there was an earlier discussion here on this board that included a photo of the SchG.1 machine: -
Correct Colour Schemes for Matchbox's Fw 190A3/4 Decals?
JasonC replied to 3DStewart's topic in Aircraft WWII
JG51 operated on the Eastern Front, and some of its early mark 190's wore the 70/71 scheme on the topsides. These two greens were quite low contrast, and might have been mistaken for a single shade of green. -
Can't vouch for either of these, but they came up on Amazon UK: https://www.amazon.co.uk/806-Naval-Air-Squadron-Top-Scoring/dp/1781557500/ https://www.amazon.co.uk/Fighters-Fleet-Air-Arm-1939-1945/dp/1777029716/
-
Google translated so you don't have to. "Good day! Sorry, but my english language = --- 1 On the second page there is my photo with Mikhail Orlov. Thanks to him and his search for originals, in 1997, the AMT series paints were created and not only AMT-1: http://shop.akan.ru/ru/6xxxx-series/109/136/63000.html AMT-4: http://shop.akan.ru/ru/6xxxx-series/63001.html AMT-7: http://shop.akan.ru/ru/6xxxx-series/63002.html AMT-11: http://shop.akan.ru/ru/6xxxx-series/63044.html AMT-12: http://shop.akan.ru/ru/6xxxx-series/63045.html I do not research photographs, but only reliable materials are used. How they look in the photo on various screens (even calibrated ones) does not really interest me. There are also screen researchers of this kind in this thread, but I do not argue with them, and advise you not to. Respectfully yours, Alexander Akanikhin, creator of "Paint AKAN"."
-
If you're not averse to masks rather than decals, then Maketar do 24" RAF letters in 1/32: https://shop.maketar.com/?product=132-raf-24-inch-letters-numbers They will also do custom sizes: https://shop.maketar.com/?product=british-raf-insignia If you do go for them, I would suggest the 'kabuki' material (basically Tamiya tape), rather than vinyl. J.
-
As far as I can tell, this PR.IX is in original condition. Clearly, it's the lens covers that are coloured rather than the bulbs.