-
Posts
410 -
Joined
-
Last visited
About mollythedog
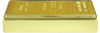
- Birthday 19/06/1958
Profile Information
-
Gender
Male
-
Location
a black hole
-
Interests
Royal Navy, USN, scratchbuilding, FAA, learning to photograph model subjects better........
mollythedog's Achievements

Established Member (3/9)
503
Reputation
-
HMS Ark Royal IV circa 1977 scratchbuilt 1/1250
mollythedog replied to mollythedog's topic in Work in Progress - Maritime
This is far as I've got on this,though there are several "modules" still not shown. I guess you can refer to aircraft as "modules" when thinking of aircraft carriers,as they make up the main weapons system. mtd- 30 replies
-
- 10
-
-
HMS Ark Royal IV circa 1977 scratchbuilt 1/1250
mollythedog replied to mollythedog's topic in Work in Progress - Maritime
Thanks for all the encouraging comments. As I have said on a number of occasions,the size of the model doesn't really apply,if you want to make something then just treat it as "blocks" and scale accordingly, whether 1/200 or 1/1250 makes little difference,except of course that in larger scales you can work in much more detail. But a model is a model in the end. Except when it's a dogs dinner that is. The thing continues to fight me, even just trying to photo a hull proved beyond my lighting and photo set up,it is just a teeny bit too big to really fit the background. Apologies for the grubby mitts, I have been rebuilding the front end of my wifes 1972 Honda 350K and the sludge from the front fork oil and rock hard steering head bearing grease won't come off. Another reason to avoid models for the moment,as oily or greasy hands destroy paint finishes. So here is a hull casting, one piece and in metal. It has been fettled a bit,but not much,and primed and blown over in a top coat. My old camera decided not to allow me to reset depth of field hence blurry ends, but you get the idea. The model dates from so far back that I have almost no constructional photos so these will have to do. I also got a header notice the other day going on about postings for WIP of RFI that had no photos, not sure why that was, maybe I hadn't posted enough,or maybe it was just a generic thing. I am sure the mods will red flag me or something if it applies.... mtd- 30 replies
-
- 14
-
-
I think that both the white and terracotta were made for repairing china and pottery. Have never used the latter,hated the white one, horrible. You are correct about the crust on the darker one,removed and you have fresh stuff underneath,but by that stage the light one is going "off"-it refuses to mix and combine with the dark one, just sticks to your fingers and everything but the other part. It has had it. Also when applying the second layer to the first it helps to moisten your finger,tool or whatever so that the mixed milliput sticks to the stuff already in place and not you. Like you I have used it many times for sandbags, bedrolls,tilts etc on vehicles, blast bags and sculpting figures or modding commercial ones. And then there is the DIY,it is superb for repairing mouldings such as door arcitraves and skirting,it dries hard and sand perfectly,the repair is invisible and solid forever after. Forget that wood stuff sold in DIY places,this is much better! Once you get the hang of it you'll always find uses for it.
-
HMS Ark Royal IV circa 1977 scratchbuilt 1/1250
mollythedog replied to mollythedog's topic in Work in Progress - Maritime
Sorry, when I said "dogs dinner" I wasn't being self effacing just saying that my builds are usually much "cleaner" and more streamlined than this dogs dinner.Which it is. But it did start looking more like what I wanted once I got to building a couple of bridges. This is a metal casting with the etch added. Forgive the rough look,this was the first try,and in my haste I used a can of white primer,instead of the normal grey,and worse,the tin was almost empty,so it has a spattered pebble dash look that is the paint and not the casting or etch. It had to be simplified a bit in 1/1250 but I tried to incorporate as much as I could,they are "interesting" to put it mildly when assembling. It was starting to grow on me,that was in 2019,until I got bored with it and it went back in the box..... The reason I'm posting this here is to try and make myself finish the *****ing thing once and for all. Hopefully it'll come out of the box now and get done,as I really love this ship and want a model of it,one day.- 30 replies
-
- 20
-
-
I have read some of the comments here with interest. I have been using Milliput for about 25 years. It is not perfect, it does have some issues,but here are some tips that will help. 1) Use the cheapest "Grey/Green" one,forget the rest.Just don't...... 2) Try to buy some from a place with high turnover,like an art or sculptors suppliers (Tirantis for example)- it ages and if is has sat on a shelf or display for years it will be past it,it isn't date stamped or anything so the only way is to buy it as fresh as possible. 3) Keep the sticks well closed in their bags, just wrapped as they came,with the end folded over and put back in the box. Note on the box the date and place you bought,for next time and know "your" age on it. 4) I have found that mixing it 80/100, that is to say 4 parts light green to 5 parts dark green gives better results. Whatever you do,at the end you will always, always end up with more light green. Chuck it. )5 keep a finger bowl of water handy, it helps to keep you hands very lightly damp if mixing large amounts. But for small amounts,that is say smaller than a pea of each it won't matter. 6) Apply using a smooth metal tool, or a modded old scalpel blade (use a Dremel to shape an old blade into a rounded or chisel ended,but blunt spatula) and apply firmly. Once you have some where you want it apply more,it will stick to itself really well. 7) Use gentle heat such as radiator,if the model can stand it,for warming it while is sets-it will set harder and quicker,in an hour or so. Or sunlight. "pot life" is about 20-25 mins if used at typical room temps. There are more,but this is enough for now. It is really good,better than almost anything else I have tried, but bin your old almost black sticks and get some fresh stuff!! HTH mtd
-
HMS Ark Royal IV circa 1977 scratchbuilt 1/1250
mollythedog replied to mollythedog's topic in Work in Progress - Maritime
Thanks. Moving on to 2018 I finally bit the bullet and decided to finish this thing. One day. So the bridge was finished and cast,and the etch test fitted-some of the main bits anyway,there's quite a lot of it.....I am no draughtsman and had to redraw the etch 3 times, each time paying to have it etched (not that expensive, really) and the photo tool and set up (quite expensive for very short run things). The real ship is a bitch to model,with a hull shaped by a committee of madmen high on some sort of glue,and this just kept stopping me from getting a real "bite" without just hitting a wall and putting it back in a box. Many times. So 2018 sometime, bridge in place and hull detailed a bit,with the first version of the boats fitted,mastered in plastic and cast in resin. Still looking like a dogs dinner.- 30 replies
-
- 16
-
-
Been a while away from here, just busy with models. Seems that most have found more time to get to projects what with all this lockdown stuff. Has made little difference to my daily routine to be honest,and where I am has been barely touched,it seems,by World events.So far. Started on this thing more years ago than I care to remember,certainly more than 15 years since I first "laid down" the hull. Has gone in fits and starts over the years,and been rebuilt and hacked about continuously. Anyway, might be on the home straight with it now,so thought I'd show some of it. Entirely scratch built,don't use 3D printing etc, never have and never will. If I can't make it it ain't worth doing,though I am sure many won't agree. That's ok. So all my own bodges,mistakes,errors and cock ups. These photos date from 2013 and show the hull construction, mostly plastic card but with a lot of Milliput,a method I tried this one time for a hull this complex,and though it "worked" I went back to traditional methods after and have only used millput for shaping hulls,sponsons etc and not hulls. It is actually a hollow hull made from a plastic card inner and Milliput over for the shape. It will eventually be cast in metal and building a hollow hull that doesn't warp or distort is more difficult than it might at first appear. It has moved on quite a bit now,though nothing changed until 2018,when I thought it was about time it got finished.
- 30 replies
-
- 22
-
-
-
1/350 HMS P311 T-class submarine
mollythedog replied to Jamie @ Sovereign Hobbies's topic in Work in Progress - Maritime
For cutting acrylic you can find sets of cutting discs on ebay- I bought my wife a fancy German sewing machine cubby hole thingy that has a spring loaded "lift" that pops up and down.It has a thick acrylic (or perspex maybe) plate that is meant to fit snugly around the sewing machine.It is about 5mm thick,and the one she had wasn't correct for her machine. I bought a set of these steel blades which are made from about 1mm steel,and in a Dremel they cut the plastic pretty well. Use masking tape to mark/guide/protect the surface. You'll have to try different speeds of both tool and cut. I used to use polyester resin for ship model casting-i would not attempt cutting it,it'll melt or shatter,or both.And ruin whatever tools you are using to do it. As a release agent you might try some Vaseline mixed with white spirit,mix well and paint it on-the WS will evaporate and leave a thin coat of vaseline-works well on other things like mould halves so might work here-test it first,it is dirt cheap and if it don't work you have lost nothing-north of that border you are known for your "economy".... Good luck..... -
If you are going to be running a lot of wires you might want to consider using some of the very fine silicon wire sold by The Component Shop-very thin and flexible and available in a number of colours. I, have used it in several R/ C projects and it works very well. Keeping track of different circuits via colours is helpful too. I like the boiler effect. I think these kits are not exactly state of the art so it leaves you a fairly clean slate to add as much detail and doo-dahs as you like,
-
1/350 HMS P311 T-class submarine
mollythedog replied to Jamie @ Sovereign Hobbies's topic in Work in Progress - Maritime
My condolences on your loss,it is a shock when it happens, so suddenly too. I just lost my Dad in a similar fashion-certainly time devoted to a hobby when possible is a great help in taking your mind off things,for a bit at least. It is nice to see an RN sub being modelled-it looks a nice kit, I look forward to seeing how it turns out in its natural element. -
Good luck with this,a handful but the subject merits the commitment,
- 421 replies
-
- 1
-
-
- scratchbuilt
- 1:48th scale
-
(and 1 more)
Tagged with:
-
Editing your old posts
mollythedog replied to mollythedog's topic in Help & Support for Forum Issues
Thanks.but Im not sure what you are trying to point out to me....I know which posts I want to edit but I cant see how. Apologies but am trying to type on german keyboard and cant find any punctuation. Apart from full stop....all I want to do is replace the old useless bb codes from photobucket with new ones from flikr so that the photos display as they should, It must be possible to to do this surely. -
I have been away for a while,and came back to find a topic I'd like to add to-by linking one of my old posts with photos of the subject in question. Unfortunately I found that a) I'd used photobucket and they are "gone" and b) I can't see any way of going back into each post and replacing the photos with ones uploaded to Flikr. Can it be done? It would be time consuming but I'd like to do it if possible, I suspect there are some others I might want to update with Flikr,and in the future it that goes t*ts up replace it with whatever free photo hosting site going. Any ideas? Thanks in advance peeps
-
AIRFIX 1/600 HMS DEVONSHIRE County Class Destroyer
mollythedog replied to adey m's topic in Ready for Inspection - Maritime
I really like this,very nice work on an old kit and proof that you don't need wood decks,photo etch or metal barrels to make a splendid model. mtd -
Thanks to everyone for the kind remarks and compliments. I hope I can show that if you put some effort in, just about anything can be made, and it doesn't have to be kit related. Luckily on BM there seem to be a number of others that agree and do much the same,though to a very high standard,and in the "normal" scales. As I mentioned previously,this is still a WIP and at the same time I built the Attacker I finished a second prototype to represent Battler, a little later time wise,but still with the same weapons fit. Both models were finished in time to take to a model show,and it was interesting to note that of the 2, the Battler attracted the most favourable comments,by a considerable margin. I can only assume that she appeared in more "traditional" Royal Navy colours (though I freely admit that the colours I chose were something of a guess,based on the time period and "typical" colours that were possibles. Thinking about this afterwards I concluded that if I'd seen,for example, an Essex or Midway class CV painted in Royal Navy camo it would appear "odd" and not right. Despite that fact that it appears well documented that several RN CVEs left the yard in US colours it looks "wrong" in most peoples eyes. But this is mere guess work on my part, it could just be peoples taste and nothing more. Battler 43a by plastichacker, on Flickr Battler 43b by plastichacker, on Flickr Unfortunately the pale green looks far too green in the photos, it isn't in "real life", ditto the weathering,which looks far too heavy and obvious,again to the naked eye it is much less so, though I am still playing with paints versus pastels on this. Anyway,this is how this version looks. Again,it has my Martlets (Wildcats) on deck,and has the prominent HF/DF mast forward, one of the very first and most important additions in RN service,but apart from the the 2 models are essentially the same. Battler 43d by plastichacker, on Flickr Battler 43e by plastichacker, on Flickr Next step is to try and correct a couple of areas that could be more accurate,and modify the weapons fit and emplacements on the port side. And try and cast it without breaking the mould,as the goal is to have several different ships of this important class. Battler 43c by plastichacker, on Flickr Battler 43f by plastichacker, on Flickr mtd