-
Posts
1,832 -
Joined
-
Last visited
-
Days Won
2
nick last won the day on September 30 2012
nick had the most liked content!
About nick
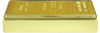
- Birthday 28/12/1964
Contact Methods
-
Website URL
https://unobtainium.digital
Profile Information
-
Gender
Male
-
Location
North Wales
-
Interests
3D, CAD, WWII Aviation, Big Iron Jets, AFV, Cars
Recent Profile Visitors
8,081 profile views
nick's Achievements

Very Obsessed Member (5/9)
3.4k
Reputation
-
Thanks for all the great comments everyone. I have been irrestably drawn to a Trumpeter Faun Tank Transporter today - watch this space! Nick
-
FInished it!
-
nick started following A kick up the RC part 3 What’s in my Lunch Box? 🍔 , RFM Leopard 2A6 Full Interior 1-35th , RFM Leopard 2A6 Full Interior and 1 other
-
Well it's finished. I've kept it new and shiny looking, well because they are mostly I think? I'd almost forgotten all this was in here - seems a long time ago! Thanks for looking! Nick
- 17 replies
-
- 40
-
-
-
Yes I’m a plane guy at heart, but these RFM kits are just fascinating, you get a real good idea of how tanks are screwed together even if you know little about them- like me.
-
Not completely finished, and noticed a few repairs required under the glare of my unforgiving L-series 100mm Macro, but nearly done... Now I don't know much about tanks, but I know a little about kits, and this is just exceptional. As well as the PE, vinyl mud flaps and decals, the moulding is just amazing - the welds, casting data and friction surfaces especailly are absolutely exceptional.
- 27 replies
-
- 13
-
-
I hadn’t really appreciated how much of this thing is turret - it’s damn near as big as the hull when it’s got all its bins and other paraphernalia fitted!
- 27 replies
-
- 11
-
-
Thanks for all the kind words everyone. I’ve been thinking about this and actually kits like this aren’t that crazy after all. ‘why’ I hear you say (one of many voices in my head) well who looks at your models? I mean in the flesh? OK you may enter the odd comp, most people don’t, so apart from that one or two like minded friends maybe? But mostly nobody, but who looks at PHOTOS of your models? Lots of people, us lot for a start, so actually the main ‘consumer’ of our models is the camera and the internet, so in that case all the ‘lost’ detail that gets locked inside, isn’t lost at all, its just as valid as the work thats still visible externally on the finished model. and for my next trick I will be proving black is white (and trying not to get run over on the next zebra crossing for any other Douglas Adams fans out there) I’m off for a lie down now anyway. Nick
-
So here's the next batch of fotos as promised. I love this kit - Completely pointless, but glorious. Thanks for looking Nick
- 27 replies
-
- 17
-
-
Bentley 4 1/2 litre Blower in 1/12th scale - may contain Airfix.
nick replied to nick's topic in Work In Progress - Vehicles
Exciting news, I've finally put version1 of the Bentley wire wheels into production. The full car as a kit (rather than a one-off) is a mamoth undertaking I have come to realise, so I have taken the decision to release the wheels as a direct replacement for the Airfix items. This means that they have the four studs on the back that fit the airfix brake drums so the wheels can both be used in new builds and retro-fitted to completed kits to give them a major boost. They make use of the kit tyres too, so are a direct replacementbwith no modification to the kit at all. In true Blue Peter fashion, heres one I prepared earlier mated to the airfix drum. I plan a version 2 that will ship with a brake set that will correct the airfix drums and mount the wheels in a more scale-like manner. Production is ramping up as we speak and they are available for sale on the unobtainium web shop today. Thanks for your patience and continued interest! PS I've also re-commenced work on the hybrid printed/CNC chassis, stand by for updates and photos. Regards Nick- 503 replies
-
- 6
-
-
I'm a huge fan of excessive, never-to-be-seen-detail so these RFM kits are right up my street. There's no real way of ever displaying all the work inside these things as transparent stuff always look a bit naff to me, exploded stuff can be made to work, but I'll settle for some photos along the way. so having said that, here's some of the really nice detail the chaps at RFM provide that will never see the light of day. I like it anyway. The 'Powerpack' I know little of tanks, but as far as I can see, the transmission has a pair of friction plates that engage with a similar set in the hull, so the whole shooting match looks like it lifts out pretty easily without messing about disconnecting any driveshafts etc. You can see them in this shot, very clever if that is indeed how it works? 'So we want you to drive this big tin box full of very large explody bullets, right next to your left ear while people shoot at you' That big old motor/transmission does fit in the hole it turns out You can still see some stuff with the lid on Lots still to do, but really enjoying this I must admit. Thanks for looking Nick
- 27 replies
-
- 20
-
-
-
Let me know if you need any more panels easy enough now I’ve figured out how to make them. Nick
-
Bentley 4 1/2 litre Blower in 1/12th scale - may contain Airfix.
nick replied to nick's topic in Work In Progress - Vehicles
It just so happens I’ve started looking at the beast again this week. Stand by!- 503 replies
-
Up to your usual standard. Amazing work.
-
A kick up the RC part 3 What’s in my Lunch Box? 🍔
nick replied to The Spadgent's topic in Work In Progress - Vehicles
Just found this thread and admiring your 3D printing exploits. Just wondering can you do that? Suspension takes a real hammering on these things, I use a lot of ABS-like Resin and whilst it looks great, it’s pretty brittle, the stuff the original parts are made from is tough as hell and flexible in comparison. If this is a thing fair enough, excuse my ignorance!- 59 replies
-
- 1
-
-
- Tamiya RC
- Tamiya Lunch Box
-
(and 1 more)
Tagged with: