-
Posts
3,175 -
Joined
-
Last visited
-
Days Won
4
CrazyCrank last won the day on June 29 2023
CrazyCrank had the most liked content!
About CrazyCrank
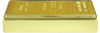
- Birthday 30/09/1958
Profile Information
-
Gender
Male
-
Location
France
-
Interests
My grand-children, photography, vintage cars
CrazyCrank's Achievements

Very Obsessed Member (5/9)
9.7k
Reputation
-
You've built this model with a master's hand. The paintwork and varnish are remarkable 👍
-
Alfa Romeo Tipo 308, GP de l’A.C.F 1939
CrazyCrank replied to Bengalensis's topic in Work In Progress - Vehicles
What more could I say than what my friends have already said? I'm lacking of superlatives...BRAVO ! -
Thanks a lot @JCH for your kind last words, much appreciated. And, to answer your question: I've used Gravity Colors paints, and not automotive ones. And I've sprayed the bonnet and all the other parts in the same orientations (criss-crossed layers) with the same angle... I'll make a guess: the area of the bonnet where the shade appears slightly different, and only from certain angles, is where I think there's a small defect in the moulding and where the bonnet isn't as curved as it is elsewhere. This could explain why the angle of attack of the paint particles there was slightly different. Anyway, as the result is quite satisfactory, and I've already done it 7 times, there won't be an eighth!
-
Thanks a lot @keefr22 😎 I've never tested the GSW brush chrome, but what you're saying comes as a surprise to me. It's actually child's play to achieve a good result with the GSW airbrush chrome. As an evidence, I was successful at the first attempt ! Joking aside, here's my process. The first two stages are crucial !: - First, get a super clean and smooth surface for the part you want to paint. - Second, spray a super glossy black coat. I usually use A-STAND lacquer primer (A-MIG-2351 Gloss Black Base Primer). Leave it to dry for at least 48 hours. - Thirdly, spray your GSW Airbrush chrome at 20 PSI with the minimum flow your airbrush allows in several very light layers and you'll quickly see the shine appear. If it can help
-
Series 1 Range Rover - Lift Kit & 32s
CrazyCrank replied to SnøMotion's topic in Work In Progress - Vehicles
Very nice and convincing job on the dash and on the spare wheel.👍 -
Hello everybody A little update this evening with the refurbishment of the air intake fairing, where the shade of grey was too dark compared to the rest of the bodywork. A real mess, to be done and redone 3 times since yesterday, due to various little problems, but it's done. The tint is good, the varnish is correct. There's a micro-dust that will go away with the usual depolishing-polishing. I also redid several radiator grilles, which were chromed today after a high-gloss black primer the day before yesterday. GREENSTUFFWORLD chrome is impressive! And the photo below doesn't do justice to the real look, which is simply stunning! The varnish on all the body parts will be frosted where necessary, then repolished with the usual compounds by the end of next week, after which I'll be able to continue with my assembly, if my three grandchildren will let me 🙄 Stay tuned 😎
-
Afternoon Gentlemen Just a quick update today: I've clear-coated the bonnet and its air intake fairing. You should know that I had several mishaps with this job over the last few days! I've had to redo the work seven times before achieving a passable result, which I'll show you in some photographs! For some unknown reason, despite using the same techniques and process to apply the clear coat to the bonnet as to the other parts of the bodywork, I got a slight orange peel effect on it. I'll easily get rid of this during the polishing session, which I can't avoid. Furthermore, there are slight variations in the aluminium shade in several places on the bonnet, which I can't explain. These imperfections are only visible under artificial light. I'm certainly not going to redo the job for the eighth time! For another unknown reason, the aluminium colour shade on the air intake fairing is darker than the bonnet's! (When the bonnet's colour is the same as the other parts of the bodywork!) I have to redo the job on this tiny part because the difference is too much obvious! Under strong day light: Stay tuned if you like 😎
-
1955 Mercedes 300 SLR Uhlenhaut-Coupé
CrazyCrank replied to Plastheniker's topic in Ready For Inspection - Vehicles
Your Merc' is very nicely done 👍 -
Morgan three wheeler Supersports 1935
CrazyCrank replied to HK-500's topic in Work In Progress - Vehicles
Your headlight bulbs are very nice @HK-500, but I think you should consider repainting them with translucent yellow, for example Clear Yellow from Tamiya. The effect, especially on top of the aluminium if you polish it first, would be much better...... Well, it's true, I'm quibbling....🙄