-
Posts
2,580 -
Joined
-
Last visited
-
Days Won
4
CrazyCrank last won the day on June 29 2023
CrazyCrank had the most liked content!
About CrazyCrank
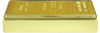
- Birthday 30/09/1958
Profile Information
-
Gender
Male
-
Location
France
-
Interests
My grand-children, photograph, vintage cars
Recent Profile Visitors
6,224 profile views
CrazyCrank's Achievements

Very Obsessed Member (5/9)
7.4k
Reputation
-
CrazyCrank started following Yet another Airfix Bentley Blower and Two Lane Blacktop '55 Chevy
-
Yet another Airfix Bentley Blower
CrazyCrank replied to The guy from quebec's topic in Work In Progress - Vehicles
I've not yet found any evidence, but, I've read that timing belts were used for the first time in 1953, and that timing chains were commonly used on cars since 1960. I guess that in 1932, on your Rolls the camshaft driven by gears, as on my Bugatti or on the Alfa 8C -
Yet another Airfix Bentley Blower
CrazyCrank replied to The guy from quebec's topic in Work In Progress - Vehicles
Hi François Finally, you bought it 😉 I don't know if it could help, but you can already follow this link to a Pocher Rolls Royce builder. Click on Build notes 1 and 2. -
Your behavior make me remember a Kipling's famous poetry ! 👍😉😎 Welcome back
- 1,900 replies
-
- 1
-
-
- Convertible
- Ford Mustang
-
(and 1 more)
Tagged with:
-
Yet another Airfix Bentley Blower
CrazyCrank replied to The guy from quebec's topic in Work In Progress - Vehicles
Hello guys I wouldn't like to spoil this topic, but... I've been lucky to visit yesterday @The guy from quebec in his home, and happy to meet a very nice guy 😎 I should say in addition that he's very modest, even though the Bentley he's building at 1:12 is worthy of a Museum. In fact, I should also say that it would be difficult to know which museum would be worthy of exhibiting his true masterpiece. Having been able, like some of you, to admire his model in the photos he took during assembly, I can tell you that, although they are excellent, they do not do justice to the incredible beauty, richness and finesse of detail of his Bentley. You'd swear it was ready to drive. Everything is built like a real car, and to scaled, and...and...I'm not here to reveal his secrets ! In conclusion, I can assure you that to be able to admire it with my own eyes was a real privilege, and that alone is worth crossing the Atlantic for! Thank you to you, François, for your warm welcome 👍 CC -
Afternoon gentlemen I'll be back home in one month. To tide you over until I get back to the workbench, here's the fourth video of my build. All texts and speeches ares subtitles in English Please watch it on Youtube, and don't hesitate to share and comment. Thanks in advance. Enjoy your watching and have a nice week-end
-
Hi guys My second and third videos of the assembly of this model are on Youtube They are in chapters and the description is both in French and in English Subtitles are available in English To see them, links below: Please watch them on Youtube instead, and feel free to comment. If you like them, give me a thumbs up and subscribe to support my channel. Enjoy and have a nice week-end Thanks in advance
-
Afternoon guys I'm still staying in Montreal, and, to occupy my mind and have fun, I've realized the first video (commented slide-show) of the building of this BMW 507 Elvis. It concerns only the preparation, modifications and painting of the body. To watch it: Although it's commented only in French (at the moment), I hope you'll appreciate it. Feel free to comment the Youtube video and to give a Thumb Up if you like it, this will be much appreciated, and don't forget to subscribe to my channel and activate the bell to be notified for forthcoming releases
-
You're right, @cmatthewbacon, this Jeep isn't powered. Mikaël, 3 year old, love it of course. He's a bit of rough little boy and it has been difficult for him to understand that, at the moment, as the toy is very fragile, he can only "touch it with his eyes", as used to say my father 🙂 My next build will be the ROKR Grand Prix Car 1:16 scale, which is, imho, an attempt to reproduce a 1910 Mercedes-Benz SSK 😎
- 26 replies
-
- 1
-
-
- Wooden puzzle
- vintage cars
-
(and 1 more)
Tagged with:
-
you’re right @Spiny ! I used effectively a scalpel, but it’s not a rule, just a statement from the manufacturer, and actually a lying advertising , as well for the “no-glue-needed “! My promise to built it strictly OOB has been broken because I added just a little stuff to enhance 2 parts…….which ones ?
- 26 replies
-
- Wooden puzzle
- vintage cars
-
(and 1 more)
Tagged with:
-
Failed 👎 🤣 I really broke my promise ! look a little better 😉
- 26 replies
-
- Wooden puzzle
- vintage cars
-
(and 1 more)
Tagged with:
-
Hi everybody Step 25: Front mudguards rear panel assembly Step 26: Assembly of left footboard, upper panel of left front mudguard / left front fender with headlight and jerrycan . . x Step 27: Mounting the windshield on its left pillar Step 28: Assembly of right footboard, upper panel of right front mudguard / right front fender with headlight and axe Step 29: Mounting of mudguards top panels, and exterior mirrors Step 30: Assembly and mounting of the exhaust This build is now complete and will be soon exhibited in the RFI section. Some pictures quickly taken to keep you patient: It's been a lot of fun and joy to assemble this kit, and my 3 year old grandson Mikael is deliriously happy because I've given him this Jeep as a gift. Now, a little challenge for my "afficionados": I've betrayed my promise somewhere in this build....are you able to find where ? Thanks for watching and having encouraged me along this thread. 😎
- 26 replies
-
- 3
-
-
- Wooden puzzle
- vintage cars
-
(and 1 more)
Tagged with:
-
Hi guys Step 21: Assembly of wheels . Step 22: mounting of radiator and grill - front bumper Step 24: assembly and installation of the hood (It's an American vehicle, so it hasn't a bonnet 🤣) And the most difficult job, taking in account the extreme weakness of the hood that you must drastically bend....without breaking it ! That's all for this release folks Stay tuned if you like😉
- 26 replies
-
- 3
-
-
- Wooden puzzle
- vintage cars
-
(and 1 more)
Tagged with: