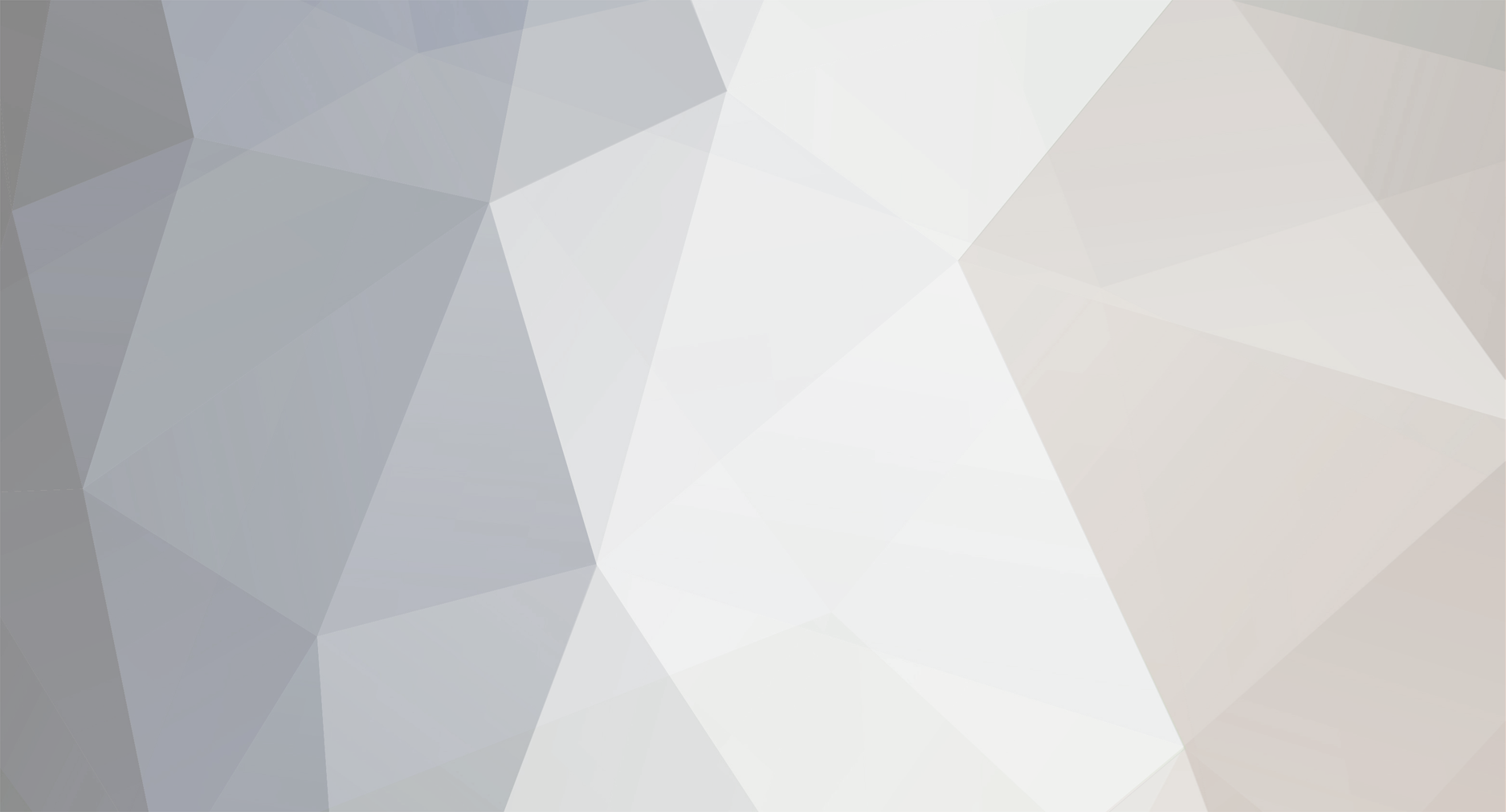
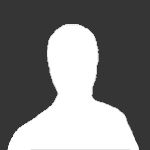
ianwau
Members-
Posts
377 -
Joined
-
Last visited
-
Days Won
1
Content Type
Events
Profiles
Forums
Media Demo
Everything posted by ianwau
-
De Havilland Australia - DHA-3 Drover - 1/48 scratchbuild
ianwau replied to ianwau's topic in Work in Progress - Aircraft
Hi Jeff. Yes - this buck is filled solid with car putty. It's not THAT much volume-wise - and I do like the idea of using balsa/foam or even creating voids using scraps of styrene. For ship modelling - I'd totally support the approach you take, indeed I've done just that on a 1/72 hyrdofoil. The main reason I vacform is so I can get the interior done - else I wouldn't enjoy the result. Yes a lot of wastage. Most of this is not reusable - although some sections do come in handy as a source for 'odd shapes' - eg I've used some offcuts to build winglets on another project. Most of the offcuts go to one of my Model Club members who somehow finds a use for them. I buy my styrene sheet in bulk (1800mm x 900mm sheets) which makes it quite cheap. Unfortunately, not with my cheap and cheerful technique. Anything with a hard/sharp edge ends up rounded when you're vacforming over the top of a 'male mould' - the hot plastic sort of wraps around the corner and leaves a rounded results (and sanding after would just thin out the plastic too much). If you make a reverse/female mould (ie where you vacform INTO the buck then you'd be OK, but you then need to find a way to create the vacuum. Quality commercial vacform manufacturers (eg Dynavector) DO use this method but they have the equipment to do it. Others here might be able to better answer this question. 3D printing might be a better route for you to go for your multiple turrets etc - but I have no experience with that (yet).- 122 replies
-
- 1
-
-
- Drover
- Scratchbuild
-
(and 1 more)
Tagged with:
-
De Havilland Australia - DHA-3 Drover - 1/48 scratchbuild
ianwau replied to ianwau's topic in Work in Progress - Aircraft
Making hay while the sun shines.... A vacforming day. I'll show a bit of detail here on the basis there is interest and it might inspire a few projects. I acknowledge others will have different approaches/suggestions - feel free to share - I always seem to learn something new from sharing these builds. I've had a thunk, and have decided an approach for the fuselage. The dominant thought here is accommodating the side windows in a way that is not going to cause me issues. The picture below shows the intended sequence First off, I'm going to mould a top 1/2 and a bottom 1/2 in white styrene. The join line will be well below the bottom of the windows (gives more room for blending in). A joining tab will be glued on the inner surfaces to make sure the top and bottom halves stay stuck (nothing worse than a butt joint for this sort of work). Bulkheads will be inserted where they exist on the real thing. My preference to mould top/bottom halves vs left/right halves are that the join lines are not visible inside the model (ie I can build up a false wall which hides the join), and also this allows me to get proper access to the interior . Once that is all dried and nicely blended - I'll then remove the entire upper centre section. Sounds pretty extreme - but this will allow me to deal with the interior (not that it'll have that much - cos you can't see much!) I'll then replace this removed centre section with a clear vacformed equivalent. That will include the cockpit side window - which is conveniently of the same shape as the fuse at that point. This'll get blended in around the perimeter and then will be able to mask the windows off etc. Anyway - that's the theory, so let's see if we can vacform the component parts... Before we start it's worth noting I don't have one of those fancy vacforming machines. I've always admired them, but most are too small for this sort of work (or really expensive). Nevertheless, I do have the equivalent, by way of a combo of household appliances and a few trips to the hardware store. Photo on the left shows the vacforming box. I have a few of these, but this is the biggest and can handle bucks up to 250mm (the Drover is only 230mm) It's basically a cheap plastic lidded box - with 100's of holes drilled in the top (concentrated around the perimeter of the fuselage). A large hole is drilled in the side of the box to suit the generic attachment for the home vacuum cleaner. And there's some thick tape wrapped around the top to ensure the lid stays on and airtight. Also a chunk of wood inside the box to make sure the centre of the lid doesn't disappear up the vacuum cleaner (yep been there, done that). The buck is attached with some 'white-tac' slightly elevated with a bit of extra white-tac under the tail to prevent the hot plastic attaching to itself (and complicating removal afterwards) The photo on the right shows a sheet of 0.75mm styrene sandwiched between two sheets of 3 ply with holes cut out just a bit bigger than the vac box. The bulldog clips are sufficient to keep everything in place during the vac process. This might all look pretty agricultural, but hey it works, and most of us have this sort of stuff lying around... So here were are in the kitchen OK the buck is now top down vs previous photo -but this fits in with the photo sequence to come. Home vacuum cleaner is connected and ready to go. Everything positioned for vacforming. Chopstick inserted in the air vent thingy of the vac cleaner - to reduce risk of box imploding under suction (yep been there, done that). Home appliance #2. The grill element in the kitchen oven. The grill is set to 150 celsius - so it's not molten lava as the photo might suggest. The styrene sandwich has been in there roughly 2 minutes and has slumped suitably. About 10 seconds after this photo, the camera was on the floor, the vacuum cleaner was turned on, and in one smooth motion straight over to the vac box and bring the sandwich over the top of the buck and wait for the suck. And about 1 second later - this is what it looks like. I actually partially remove the chopstick to optimise the suction - then put it back in just while the temp drops back below the 'soft plastic' point - about 10-20 seconds. You can see the suction has distorted the lid downwards (and the container sides inwards) - for which the block of wood I have inside becomes essential. Different vacuum cleaners will perform differently but they all suck pretty hard when the air source is blocked off. This is a successful shot by the way - the plastic has been drawn more than halfway down the sides of the buck, and I don't have the dreaded banyan tree roots intruding on any portion of the finished part. So same again with the clear. I'm using 0.75mm PETG - I used to use Butyrate but had a bad batch and thought I'd try the PETG. Photo at right shows the vacformed clear panel Photo at left shows the vacform clear removed from the frame and before trimming. Nice and clear. Happy with this - and again it's drawn down beyond the halfway point. And here's the top 1/2 in white styrene. Photo at left shows result pre-trimming Photo at right shows the underside of the vacform shot - with the buck still entrapped. This popped out just fine when I cut excess plastic from the rear of the fuse, and a bit from the nose. It should be noted I NEVER use a release agent, and NEVER paint/undercoat the buck. The release agent is simply not required. And painting/undercoating whilst improving the quality of the buck, usually results in the paint/undercoat attaching itself to the melted plastic during vacforming creating a bit of a sticky mess. So now we have the component parts I referenced up above. Photo at left shows the roughly trimmed clear section (sitting on the buck), the top 1/2 and bottom 1/2. These are then trimmed to a common horizontal line - using the buck for guidance and a razor saw. It's actually a bit of a fiddly exercise - obviously you want to cut off too little vs too much Basically I chose the longitudinal former in the buck as the common horizontal line. A pencil line for this and a pencil line for where the top/bottom halves finish then provides a measurement of how many millimetres need to be cut from each vacform half. So measure about 10 times and cut once... Photo at right shows the result with the top and bottom halves now sitting tightly on the buck and a very satisfactory join line (not of Tamiya quality, but good enough for the task at hand!) Also at right note the offcut from one of the trimming cuts - which makes a very hand full length join tab which will be used on the inner surface. This offcut already has correct curvature longitudinally and vertically which makes it a better solution than a nice clean strip of styrene. Getting there! Photo at left shows the full length join tab pegged into position. Also the bulkheads cut and put into position. Photo at right shows same thing with an extra bulkhead at the front, and the cabin floor now installed (easier to do it now than later) And here's the results with top and bottom halves now glued. The X's indicate the section of fuse which will be later removed and replaced with the clear vacformed section Note I have NOT glue the top and bottom halves where the X's are - nothing to be gained from doing that. And the join tab will this way be completely usable for the clear section. Leaving this centre section in place for this steps helps keep everything lined up and true while the glue dries. I'll do a fair bit of cleaning up of this before proceeding to the glass. So below is a summary of where we are at. - fuse has been joined - wing tips are cut/trimmed to size/shape. Wing roots still overlength - I'll cut them when I've worked out the wing to fuse join method.. - tailplane and fin have had wing tips cut to size/shape. Next steps: - the apparently frantic pace will slow down a bit - fuse needs to dry and be sanded/blended and tidied up. - Fuse will then have the top cut off - and will attend to the interior, cockpit etc. Also the seed hopper (this will be an aerial agricultural version...) - Might sort out a solution for joining the wings too while I'm in there - using the proper position of the internal spar. - also need to make a buck for the Gypsy engines.- 122 replies
-
- 16
-
-
-
- Drover
- Scratchbuild
-
(and 1 more)
Tagged with:
-
De Havilland Australia - DHA-3 Drover - 1/48 scratchbuild
ianwau replied to ianwau's topic in Work in Progress - Aircraft
Yes I was thinking about that, but wasn't sure if it'd compromise the strength - so went the all the putty route. Had a brand new tin of putty which is still 2/3 full...- 122 replies
-
- Drover
- Scratchbuild
-
(and 1 more)
Tagged with:
-
De Havilland Australia - DHA-3 Drover - 1/48 scratchbuild
ianwau replied to ianwau's topic in Work in Progress - Aircraft
Long weekend - so a bit of an opportunity to progress. A few photos below show the progress of backfilling the skeleton of the buck Putty being used is standard auto-body filler ('bog') available from your nearest auto-parts store. It's a two-part mix requiring a 'golf ball of putty and a pea of hardener'. I do not have a favourite brand, they all seem to work, and all seem to be 25% styrene. Putty goes off in about 10 minutes - and is ready for sanding within 30 minutes. Meaning you can get the whole thing done basically in a day. Picture on the left shows results after 1st layer of putty - failed cookie is an apt description. You can see where I've used the top view and side view profiles to remove excess putty and minimise sanding. Picture on the right shows results after sanding. 80 grade wet and dry sanded wet (mainly to minimise dust). Sand ONLY till you get a glimpse of the white formers showing through. Still pretty rough eh? So 2nd layer of putty. Same process - again, I'm using the side profile and top profile as a guide for layering on the putty. Continuing to be generous - but not creating too much sanding work. Remember, I have max 10 minutes work time before the putty goes off. And it's sticky stuff.. Photo at left shows result of 2nd application. Photo at right shows what it looks like after sanding - a significant improvement from Layer 1 - but still some major areas. And skipping along... Photo at left shows result after sanding the 4th layer of putty. Basically we're there - just a couple of minor areas to attend to. Note the buck is intentionally a little undersized to allow for the thickness of the styrene when we vacform. The front windscreen is primarily flat panes - and I'm not (at this stage) planning to vacform that. Likely to modify the buck somewhat so that the windscreen area does not negatively impact on the vacformed shape Photo at right shows fuse after application of an automotive scratch/stone/chip filler. This is just a one pack putty (Isopon) straight out of the tube and has some self-levelling properties. Again available from an Auto parts store. This putty reminds me a bit of the old Squadron Green putty which I haven't used for years. Will let this dry overnight So onto the wings: The wings have been glued and bulldog clipped for 24hrs before I've proceeded to the sanding Photo below shows the wings after judicious sanding with 240 wet and dry (sanded wet) and then 400. Pretty much there. The one on left needs a bit of Milliput on the leading edge to bring out that shape a bit. The one on the right needs a little Milliput on the top of the leading edge - where the bulldog clips were a little enthusiastic in the 'welding' process And below is a close up of the left hand wing Note the natural curvature by using 0.75mm as top skin and 1.0mm as bottom skin - the respective top vs bottom curves are what you naturally get. Remember the I-beam spar is effectively NOT glued to the skin (only 3 pinhead dots of glue between bottom skin and spar, not a drop of glue at the top) The need for a bit of Milliput on the leading edge is pretty obvious - I might do a bit more sanding of the bottom curve of the leading edge afterwards. And here's the tailplane and fin - similarly sanded off. No issues to attend to here. Pegs are just to keep my fat fingers out of the photo. So here's where we're at. Wings are made overlength at root and at tip - it's easier to cut it off later than put it on? And extra length also assists with keeping straight edges when sanding Next steps: Cleaning up of the wings/tailplane/fin - sanding the Milliput and getting comfortable with the final shape. Trimming wing tips to size and tidying up/finishing off. And the BIG one - vacforming the fuselage from the buck - haven't quite decided if I'll vac in white styrene and have an infill for the windows, or vacuform whole fuse in clear. Will ponder...- 122 replies
-
- 15
-
-
- Drover
- Scratchbuild
-
(and 1 more)
Tagged with:
-
De Havilland Australia - DHA-3 Drover - 1/48 scratchbuild
ianwau replied to ianwau's topic in Work in Progress - Aircraft
Nice subject choices! 1/32 definitely takes the modelling effort up a notch - means you have to do detail things that don't necessarily pay dividends in 1/48. I like your method for having separate ailerons/flaps. With more 'modern' aircraft with finer panel tolerances and in 1/48, I'm happy to get away with simple scribing. But I do have a 1/48 DH84 Dragon scratchbuild in the wings which is really going to benefit from this sort of approach for ailerons, rudder, elevators. I've never modelled in wood so probably not easier for me although it may be for others. The styrene wing is pretty quick from my perspective - there's probably about 3 hours work to get the basic wing shape formed (and a fair bit of watching glue dry). I know some will have carved the fuselage buck from basswood - just showing a different technique- 122 replies
-
- 3
-
-
-
- Drover
- Scratchbuild
-
(and 1 more)
Tagged with:
-
De Havilland Australia - DHA-3 Drover - 1/48 scratchbuild
ianwau replied to ianwau's topic in Work in Progress - Aircraft
Basically a thin bead for entire length before bringing 2 bits together. Tamiya Extra Thin evaporates too fast for this to work. As long as there's an outlet for fumes to escape and glue to go off it doesn't seem an issue? Enclosed spaces trap the fumes and definitely a problem. Hot off the modelling bench - I've just glued the wing L/E. Key points from this photo: the trailing edge has a 0.5mm strip inboard of the join. Mainly for a bit of extra strength when I start scribing flaps/ailerons etc. T/E has dried for 72 hours since glued before I brought the L/E together Bottom skin is 1.0mm, top skin is 0.75mm. So when they are joined at L/E they each have a natural curve which conveniently is awfully close to wing shaped. The tapered I-beam spar is NOT glued to the upper skin and only about 3 drops of Contacta on the bottom to keep in postion. No glue ensures the top and bottom skins form a completely natural curve The horizontal parts of the I-Beam help spread the force and do create a level of flatness on the top and bottom skin where you need it... The L/E spar is also tapered - and has a wider 0.75mm top strip, to give more purchase to the top skin and provide a bit more meat for later sanding back. The wing chord is a bit longer than it needs to be - which means the L/E is going to be sanded back from where you see it - obviously giving the required curvature over the top vs underneath... No favourites - I picked up my latest tin from SCA. They're all about 25% styrene which seems to assist with bonding it to buck (though those little triangles I have also serve to key the bog to the core). I basically layer it up - as thickly as I'm able to for each layer without causing myself unnecessary sanding effort. It generates heat as it goes off - but not enough to have caused problems. Will show some progress photos of this - I expect 4 layers to get something presentable (looks like a failed cookie before that). No to Plaster of Paris - too soft, too course, yuk! Sydney, NSW. Was up in SEQ this last week - with many visits to the QAM Drover(s) for reference purposes! Thank you for the interest!- 122 replies
-
- 8
-
-
-
- Drover
- Scratchbuild
-
(and 1 more)
Tagged with:
-
De Havilland Australia - DHA-3 Drover - 1/48 scratchbuild
ianwau replied to ianwau's topic in Work in Progress - Aircraft
Absolutely! I take about 0.75mm off the perimeter of all the formers when cutting (although my cutting is not quite as precise as that). I'll vacform using either 0.75 or 1.0mm sheet - noting that the 'stretch' of the process means the end product is thinner skinned than that. It always seems to come out 'close enough' for me - I'm sort of in the 'if it looks right, it must be right' camp vs a precision engineered result? In the pics I have glued and clamped the trailing edges (leading edge will come later). The T/E clamps were removed within about 5 mins of gluing for exactly the reasons you describe. The clamps were there to ensure the bonding surfaces were in positive contact, vs there being any stress at this stage. I've used Revell Contacta as the glue - the joint HAS to weld properly, else it'll split when I bring the leading edges together. In terms of the leading edge - the clamps need to stay on 24hrs and I do sometimes get a bit of deformation from the pressure of the clamps. This usually sands out (as I have excess material at the L/E) - otherwise a bit of Milliput comes to the rescue. The L/E is far more forgiving with this than is the T/E. I'll try and include some close-up pix of T/E result in next update.- 122 replies
-
- 6
-
-
-
- Drover
- Scratchbuild
-
(and 1 more)
Tagged with:
-
De Havilland Australia - DHA-3 Drover - 1/48 scratchbuild
ianwau replied to ianwau's topic in Work in Progress - Aircraft
Thank you! AND - I actually have a cropduster scheme in mind for this one (seed spreading strictly speaking). Not the most exciting scheme - but fits in with my croppie theme. (Image credit: Geoff Goodall via Ed Coates Collection) http://www.edcoatescollection.com/ac1/austmz/VH-PAB2.jpg- 122 replies
-
- 2
-
-
- Drover
- Scratchbuild
-
(and 1 more)
Tagged with:
-
Time for another scratchbuild. Most de Havilland aficionados would be familiar with the DH104 Dove and DH114 Heron. Quoting Geoff Goodall: "At the end of World War Two, the Australian associate of the parent De Havilland company, De Havilland Aircraft Pty Ltd at Sydney NSW (referred to as DHA) was completing wartime RAAF Mosquito orders and looking for a new design to build for the post-war civil market. The general concept was a single-pilot utility transport for 8 passengers as a replacement for the many DH.84 Dragon biplanes in use in Australia. It was to be of simple rugged construction with fixed undercarriage suitable for Outback operations on rough airstrips, with low-powered 145hp DH Gipsy Major 10 Mk.2 engines, which were in plentiful supply. The new aircraft was the DHA-3 Drover....." (source: https://www.goodall.com.au/australian-aviation/drover/drover.htm for much much more....) Below is a photo (credit: Geoff Goodall) - which bears more than a passing similarity to the Dove, and is of a similar size - but with an extra engine. Actually the Drover had very little in common with the Dove other than stressed skin construction concept. Much more on this at the URL provided above... From a modelling perspective - whilst the Dove has been well served (certainly of late) in 1/72 - the Drover less so. There's a number of modelling articles where people have converted a Dove to a Drover, and older articles converting the Airfix Heron to a Drover (and the Airfix Heron to a Dove) - basically major cut and shut surgery. But I wanted a 1/48 model (my preferred scale) and so we turn to scratchbuilding. First problem was getting decent plans - the best I could find was some 'thumbnail plans' - not sure of source but might well be Jane's or similar. These don't respond well to enlargement (the pen lines scale out at about 6" thick), and there were aspects of these drawings just didn't look 'right'. I know Air Britain has a publication on the Drover with drawings from Juanita Franzi which are sure to be great - but it'll take me a while to source that locally (or pay o/s postage!!), and there's a model to be started! Luckily there's a number of airframes in Australia - including a mostly complete Drover, and a fuselage at Queensland Air Museum in Caloundra. So it was a museum visit, and out with a camera, tape measure, pen and paper. The scribblings below was the result of the visit - the drawing at left the enlarged thumbnail plans I was starting with.. Anyway - after translating all this lot to 1/48 - here's what the fuselage plan looks like - top view, side view and cross sections. This was my main concern with the thumbnail plans and there's certainly some differences... So - let's cut some plastic! The fuselage has compound curves all over the place - which is going to require vacforming. And vacforming means I need a 'buck' of the fuselage. My technique here is to first build up a skeleton of side view, top view and cross sections - which we'll later fill in with 'car bog'. You'll see this happen over subsequent posts. Below is the skeleton being built up. I've cut the side view as a single piece (0.75mm styrene) and am adding the cross-sections out of 0.5mm styrene - half on the port side, the other half on the starboard side - with a 0.75mm sliver removed to allow for thickness of the side view piece.... Little triangles of styrene help provide structure and keep things at right angles. And here's what it looks like with all the pieces of the skeleton in place. It'll need some time to dry before I fill it in. So let's move to the flying surfaces - a few hours work required to get the component parts as you see them below. - wing top surfaces (0.75mm styrene), bottom surfaces (1.0mm styrene) and the empennage pieces (all 0.75mm styrene). - All the trailing edges have had their inner surfaces sanded to a fine taper with wet & dry sandpaper. - I've also built up a tapered spar (basically an I-beam), and a tapered leading edge (laminated 1.5mm styrene) And in about 15 minutes - all the trailing edges are glued and clamped. Main spar is tacked in place, and temporary spars have been used for empennage. This now needs time to properly dry as the process of glueing the leading edge is going to put a bit of stress on this glue joint (done it before - it works fine). That'll do for the first post. Next steps. - start backfilling the vacform buck with car bog. - glue the leading edges of the flying surfaces.
- 122 replies
-
- 28
-
-
- Drover
- Scratchbuild
-
(and 1 more)
Tagged with:
-
A late entrant to this build and following with interest - with the Anson kits finally available in Australia! The build looks great so far - and the Silhouette files an unexpected bonus. Thank you!
-
Heller 1:72 Lockheed 1049G Super Constellation
ianwau replied to Hoverboy01's topic in Work in Progress - Aircraft
Nice job! Connie looks magnificent in the air on her regular flights. Surprised that the Constellation has received so little attention from the kit manufacturers. -
Go for it! ASsume you have the Ceres book from Derek Buckmaster - brilliant reference. I've actually done the 1/48 conversion a few years back - here's a Flickr album showing some of the build https://flickr.com/photos/164110839@N02/albums/72157713390688331
- 40 replies
-
- 1
-
-
This one has come together with a bit of a rush... One of the key milestones was on the decal front. I've been doing home made decals for quite some time using my colour laser printer, clear decal sheet - and wait for it...... MS Powerpoint! Powerpoint allows you to do all sorts of things with a range of fonts and standard Powerpoint features (eg the red Shell Chemical lettering with yellow outline, script lettering etc). The image below is an A4 sheet of the latest print run - sort of like a Where's Wally finding out what other projects I might have on the go.... The Ceres is up the top left - with multiple variants checking out impact of different weight of yellow outline on the lettering..... So I've skipped the step of showing how I cut out decals and apply them and also the weathering process (familiar territory I'm sure?). And here's where we are.... Note that the yellow on the wingtips etc is actually far less lemony than it looks in the pix - in fact it's more orange in colour (I was trying to get a Shell Yellow to match the Shell branding). Anyway - apart from a bit of toning down with pastels here and there - that's now officially finished from my perspective. Thanks for following long. And whilst I have no connection - I'd highly recommend you source the new AirCast Resin release of the Ceres. A beautiful little kit of a pretty rare beast. Thanks for following along! Cheers!
- 40 replies
-
- 11
-
-
And it looks like the Ceres kit is due to be re-released by Aircast Resin - and guess which markings it has! A bit late for me, as I'm all set to do my own custom markings. But proves that scratching/converting/customising something is a sure way to expedite a kitted alternative! Aircast Resin have a facebook page - or there's an email on the box...
- 40 replies
-
- 3
-
-
-
So some more progress through December and over the Christmas break. The replacement vacform canopy has been trimmed to size, and glued on using Testors Clear Parts cement. Then blended in with Mr. Surfacer 500 (the one in a jar). Pretty happy with this. Have also made custom masks for the canopy with the Silhouette Cutter and the software it comes with. No idea how I would have done it otherwise... And glued on various other bits using superglue. So here is what she looks like after airbrushing the silver. the little bit of pre-shading I've done gives a bit of subtlety to the finish vs being a monotone. For the silver I've used SMS Aluminium - an Aussie product now increasingly available in the UK. Recommend you try it if you haven't already. Nice stuff - it's lacquer thinner based but easy to use and a good range. Then onto masking for the yellow. It's possible this is meant to be dayglo orange (as it was a few years later on this airframe) - but I've elected to paint it "Shell Yellow" as the aircraft was on contract to Shell Chemicals - and given they paid all the money for fancy signwriting on the aircraft figured they might also have paid for the extremities to be painted in Shell Yellow. Well that's my story anyway! For the yellow I've used Tamiya Acrylic XF-3 darkened up a tad with XF-7. Then a coat of semi-gloss clear over the top before removing the masking. I removed half the masking before remembering to take a photo... So here's where we're at. Walkways masked off and painted black and ready for next steps Next steps print up the custom decals and apply various dangly bits fine detail painting wheels, prop, And a bit of weathering to give it all more tonal variation... On the home stretch. A fun little build...
- 40 replies
-
- 10
-
-
Special Hobby Chase me! The Bugatti 100 Air Racer in 1:48
ianwau replied to Mike's topic in Work in Progress - Aircraft
Oooh! Following with interest! I started a scratchbuild of this in 1/48 over a decade ago. But a sixth sense said there'd be a kit of this.. Only took a decade - must source one... -
Some more progress to report. - the tailplane was added. Unusually for a resin kit - these feature some locating tabs/slots which make the exercise much simpler. - the lego jig is much simpler than I normally do - but is there to make sure the horizontal stabilisers dry horizontally while the 5 minute epoxy does it's 5 minute thing. - i know you can use superglue/CA, but find it either sets at the most inconvenient moment, or doesn't set precisely when you're ready for it to set. And it's a bit more brittle for 'structural' items. - anyway, it's a nice neat fit. Just a touch of putty will be required here... So have then pushed ahead adding on various detail items - hoppers, engine bulkheads, exhaust etc - and a bit of feathering in here and there - and a photobomb from a 1/48 scratchbuild cropduster. Anyone any guesses? Not the most common croppie but very distinctive shape... So then the canopy looms which thus far has stayed safely tucked away in the sealed plastic packing it comes in... - LiftHere! to their credit supply TWO vacform canopies, AND a resin master. - the resin master is exquisite, with the canopy framing pretty much spot on in terms of width. Although standing a little too proud (by about a scale 1 inch/25mm of proudness). - and unfortunately the exquisite-ness has not translated that well to the vacformed result.... - the canopy framing on the vac canopies is overscale in both width and depth - reminds me of the early 1/72 Airfix kits which we were all very happy with at the time, and went to great lengths to paint with a hairy stick. Times have changed. - Pleasingly the supplied resin master provides a solution - by firstly, sanding off the beautifully scale canopy framing.... - the result of which you can see below, together with the original chunky framed vacform part. So here's the revised resin master all set up on the home brew vacforming 'machine' - trusty Lego to the rescue yet again - to make sure the master has a bit of distance from the vacform plate (we'll see why in a minute). - and some white-tac (like blue-tac except white) used to hold in position. And here we are with the vacformed replacement - The medium used is 15 thou clear Butyrate from K&S that I happened to have spare. Whilst I've used K&S for year - I note I've had a dodgy batch of K&S Butyrate recently - it went all micro-bubbles under heat when it's specifically supposed to be for moulding/vacforming (?!?) - the reason for the Lego 'risers' should be clear from this. You'll invariably get Banyan Tree Roots (BTR) forming off the edges of the master down to the vacform plate. Too close, and the BTR intrude into your vacform result. - this was first attempt, and entirely usable... So below - I've masked out the inner edge of required cuts. - Using the original resin master as a guide, and a bit of black texta to indicate where originally supplied canopy finished up. - For cutting, I have one of my favourite tools. A little 12V rotary engraver/cutter - in this case fitting with a cutting wheel - it might look a bit 'industrial' for 1/72 canopy, but I've found it a far safer alternative than eg a razor saw or scalpel. - It spins 'fast' which means the plastic pretty much melts on contact. So basically no pressure is required to cut. Just a steady hand and good eyes (with optical assist!). So here's where we're at. - New canopy is roughly cut out. Have left a bit extra for final fettling before fitting. - a bit of swarf evident on the canopy from the rotary tool. Easily sorted... - @Derek_B - did you have a view on whether canopy height on the model is a bit underdone? The rear fairing looks just a tad stumpy to me? Although kit provided canopy seems to match your plans well, so happy to comply with those dimensions too! Next steps will be fitting of canopy. - Canopy framing will be re-established using paint. - Canopy masks will be done using the Silhouette Cameo mask cutter- using the plans from Derek's Ceres book. Fun little build this. Onwards....
- 40 replies
-
- 8
-
-
Some more progress.... The patient is in the recovery room having had a bit of liposuction to the aft section of the cockpit fairing. Not as hard as I thought - there was sufficient thickness in the resin to allow removal of a sliver of resin on what was previously an overly rounded profile. Thanks @Derek_B for the tip off! Still a bit more fine tuning - but won't require a general anaesthetic Oh - and I've glued the wings on.... Which has revealed a bit of an issue vs the plans/pictures (thanks again Derek!). - we're missing a bit of dihedral on the outer wing panels? - remember this is a one piece resin wing, so inherent in the moulding.. - actually not that disturbed by this. It's a beautiful piece of resin moulding, and a relatively straightforward fix Anyway - method has been to: - cut the wing 2/3 of the way through from the UNDERside - insert a 0.5mm styrene sliver. - glue with thin superglue and sand off -blend in with milliput (which is what you see in the pic below). - (the eagle eyed might note an extra cut on the inner port wing - a little 'adjustment' was required to true things up....) And here we are lining up back to plans... Next steps, - a bit of sanding of the Milliput (and maybe some touchups....) - tailplane - add hopper top and bottom - canopy. soonish.... Enjoying this one. As mentioned 1:72 not my normal scale - but gosh they take up quite a bit less space than 1:48 equivalent...
- 40 replies
-
- 9
-
-
Thanks Derek. An operating theatre appointment has been made for the patient. It's a tricky shape - I can see how LH! (or Aircast?) tripped up. .VH-SSF! Would love to see her painted up in an earlier SSF scheme! The Airfarm red fuse and yellow wings are so recognisable. Current Blayney Airfarmers scheme looks a bit trendy 1980's/1990's vs peak Ceres ops? My cockpit mods are, to be honest, pretty basic. Could have gone to town on it but my eyes and brain would not have appreciated it. Kit basis is a good start though.
- 40 replies
-
- 1
-
-
Thanks Derek! I'm looking at the Pg153 profile of SSZ Ceres-B but can't see the extra window? (Pg63 is Ceres-C). I can see CA28-2 on Pg135 has extra window but not CA28-5 SSZ.... Am I missing something? Also re the shape of the aft end of the cockpit fairing - do you have handy any photos that demonstrate the required shape? Most photos don't have sufficient resolution/detail to show this specific area. Happy to do a bit of surgery to get this fixed.
- 40 replies
-
Looking real nice! Glad to see this one progressing - I have this kit in my stash and your progress is nearly inspiring me to start it!
-
Bit of an update. Now I should note that my 'normal' modelling scale is 1:48 - so this 1:72 caper is really testing my patience. The interior has gone together well enough. The kit provides cockpit floor, rudder pedals, instrument panel, control column, seat - all of which usable. And a "cockpit roll bar" which no matter which way I turned it - couldn't fathom what they LH! had in mind. Besides which the supplied roll bar work out about a scale 3" (75mm) rectangular section. So binned that and replaced with a stretched sprue construction to match photos in the beaut Ceres book. Note my style of modelling is only to bother with detail that CAN be seen - so I have not replicated the entire fuselage framing, and have simplified other bits. Certainly respect those who go for the full detail - just not something I prioritise.... Anyway - below is an early dry fit of the fuselage halves. You can already see how little you can see inside the cockpit. Fit is 'very good' by cottage resin standards. Incidentally, I followed up on Derek_B's comments about Aircast Resin (per post below) In checking out AirCast Resin - the entire packaging of this kit looks like many other AirCast Resin kits (apart from the LiftHere! branding). Which makes me think that the other kits in the AirCast Resin's catalogue must be equally delightful. LOT's of civilian 1/72 aircraft. I'll be exploring this further... So charging ahead, fuselage has been glued together - using sparingly applied 2 part 5 minute epoxy glue. Waited 6 minutes and cleaned up glue residue and wet sanded with 800 grade. Then applied a bead of Milliput to the the join lines result of which you can see below. Not much putty required - that'll be more apparent once i sand off the excess. Insides were painted silver, with (non visible) extremities painted in black to ensure they remained non-visible. Instrument panel in black and picking out of detail on the cockpit sides. Detail is fairly basic - but still more than you get in many of the older (but still stocked) 1/72 kits. And per above - commensurate with 'what you can see'. And the underside... There's a rather odd 2mm gap between the wing trailing edge and the fuse. Had to go hunting through Derek's book to work out what was going on - but have filled it with a filet of styrene strip. No big deal - the instructions are of little help by the way. Apart from every part being named (which is 90% of the solution), there is NO indication of placement. Which means having great reference is essential... Below is a pic of the glued fuse sitting on the wing (dry fit). You should get a bit of a sense that the parts fit is VERY GOOD - and minimal putty/surgery is going to be required. Also of note is the tailplane which rather than a butt joint - has some handy little tab recesses. That will indeed be handy for getting a strong/positive joint. Also- I have settled on a colour scheme (so many tempting schemes to choose from!). The kit comes with very nice decals for VH-SSZ in a nice silver and dayglo scheme - but a few people have done that, and I like doing something different. Earlier in the life of VH-SSZ (1960) she had a 3 month contract with Shell Chemical (Aust) who were providing an Aerial Spraying Service in Western Australia - spraying lots of goodies in the Shell product range. Rather conveniently - this is a Ceres-B (single seater) which means no surgery is required for the kit (and also why I've pushed ahead with the interior detailing and fuse gluing. Photo below is via Geoff Goodall - silver overall with Shell branding and wingtips, fin/rudder tip etc probably in Dayglo (although I might exercise some artistic license and go for "Shell Yellow" given Shell forked over all the money for branding). I've explored whether the fuse underside is actually 'black' but consensus is that this is a poor contrast photo (ie was only in this scheme for ~3 months - hardly had time to weather...) Next steps: - sand the fuse - glue the wings on and blend in - glue the tailplane on and blend. - engine and cowl.... This kit will be through to paint fairly quickly. Rather looking forward to that - and the decals (home printed) should give it quite a Lift! And for dcrfan I've actually done a 1/48 Ceres. This one was a Sierra hobbies conversion of a Monogram Texan into a Wirraway - THEN converted into a Ceres! The Special Hobby route should be MUCH easier - go on, make a start!
- 40 replies
-
- 11
-
-
[Posting on behalf of Alan Flett - who has not as yet resolved his Britmodeller access. Photos are copyright Alan Flett per watermark. Alan is well known in Australian Aviation History circles for his prolific photographic record of Australian aviation since the ~1960's - much of which in company with his father] Alan: "these photos were taken 48 years ago with the specific but unrealised intention of making a model of the Ceres because no model company was ever likely to make a kit of it! They might however now be useful for ‘anyone’ who might want to modify some possible future kit into a two seater?"
- 40 replies
-
- 8
-