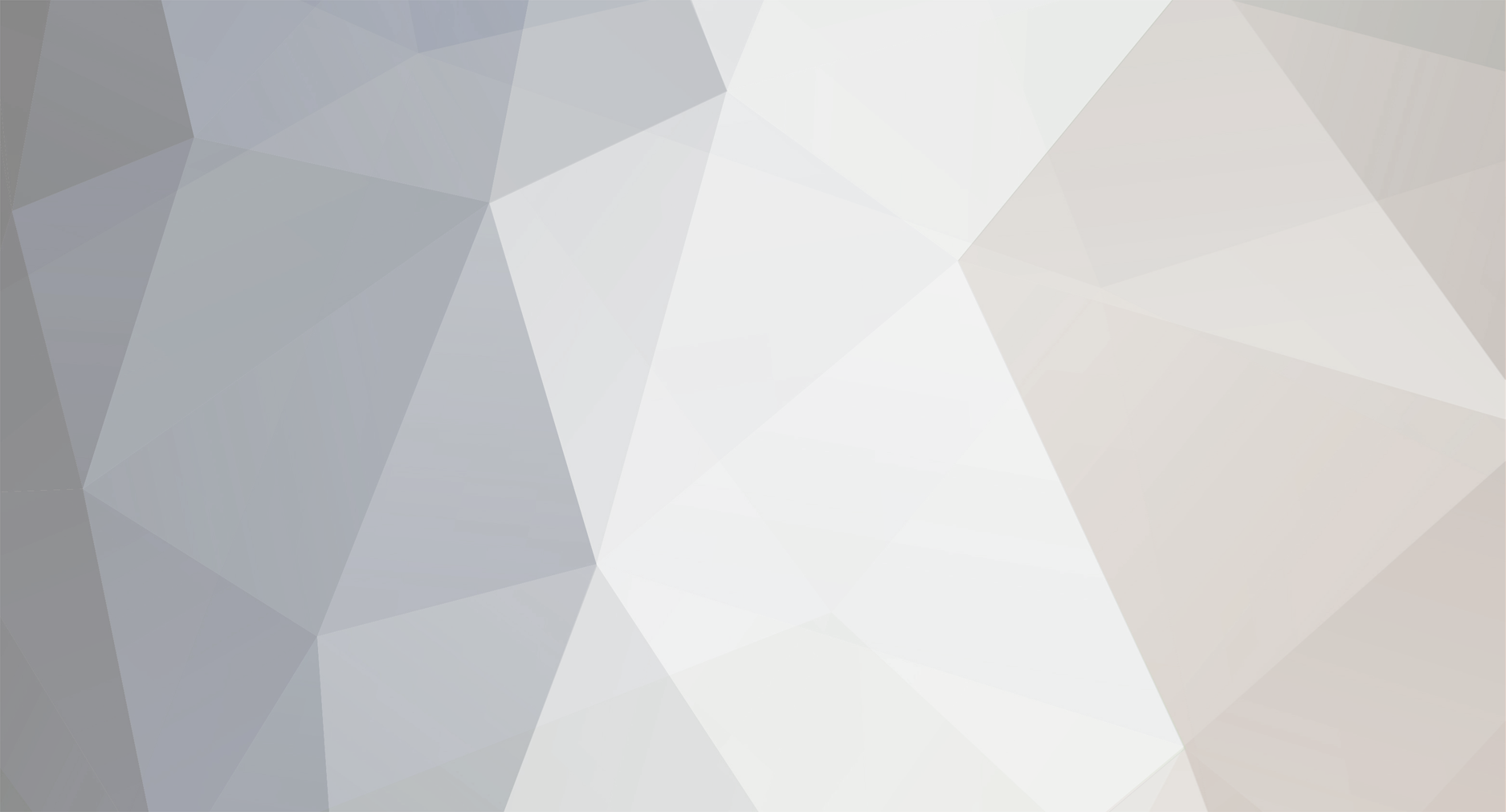
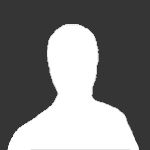
Torbjorn
Members-
Posts
1,432 -
Joined
-
Last visited
Torbjorn's Achievements

Very Obsessed Member (5/9)
4.6k
Reputation
-
Thank you - it’s Airfix’s 1/72 kit kit, with new wings, engine, etc. Yes, they were, but they had detachments in several different, changing locations at times. I believe this particular machine was stationed at Detling during the second half of 1917.
-
Forgot this post. In case anyone wonders I found pictures of other machines in the unit with the tank and a Lewis gun on a foldable stick, like so:
-
Missed the deadline by a longshot, but I had valid causes. Anyhow, I haven’t forgotten. Various shades of PC10 applied, then against better judgement I tried applying the Roden tail stripe decals, which of course half disintegrated. Should have painted immediately. Lots of silvering on the ’G’ as well
-
May I suggest painting? The decal disintegrated when I tried…
-
I have built one of these, and was considering to warn you of these difficulties, but I see you found out Beware of the wing roots, I remember that being the worst part.
-
A bit more progress. There is a large vent/opening on the underside. Visible empty insides bothers me, so I added a tank (oil/fuel?) that can be seen, plus the firewalls that come with the kit: Then turned to the radiators. The upper one in the photo below is for the Viper. The PE fret has replacement grills/shutters for this one. There were several different versions for the Hispano, fortunately the one I’m building had the early kind with vertical shutters that is included in the kit. It appears it did have shutters in the middle section as well, which I added: here I’ve started to modify it. Modifications included opening the holes, adding brass lining on the inside of the Hisso radiator, and some extra details, including ”wooden” PE frames on the inside: Then I discovered I’ve made a booboo. The kits come with three versions of the fuselage top piece with different cockpit openings. Of course I managed to use the wrong piece on BOTH models and firmly attach them to instrument panels and fuselage. After many silent naughty words I sliced off the piece from the Viper, and the. got ofg instrument panel, but the Hisso is attached with generous amounts of CA and too delicate to remove without permaneny damage. Plan B is to change airframe to McCudden’s B4853, which had a modified cockpit consisting of built-up bulging sides making it appear like a little tower-like structure. I carved away around the cockpit and used plastic sheet to create this structure, and milliput for the leather. Below is the new finished McCudden cockpit (bar a bit of filling and sanding), with the correct standard cockpit for the Viper resing inboard on the wing , and the now removed piece I had used next to it.
-
Go Twin Boooooooms!
-
Aye, Venn diagram approach!
-
I had things powered by Eagles in mind.
-
Oh man, not a single contender I voted for is above the line. Seems like 2025 will be a bleak GB year for me. Go Rolls-Royce!
-
No progress but I’ve at least chosen airframes, with the following pecularities: Hispano-Suiza: McCudden’s B4891, 54 squadron. -Wooden landing gear -Shortened exhaust pipes -no headrest -experimental narrow chord elevators -four-bladed prop (but which one? there are two on the sprues) -no white in the underwing roundels -vertical radiator shutters -white pennant on rudder? Viper: E4071 or D6586 of No 84 squadron, piloted by Sidney Highwood and others resp Anthony Beauchamp-Proctor -Wooden landing gear -Um, standard everything?
-
You’ve got some strange moose. Ours are fairly docile unless in rut or drunk.
-
I wish they had a light version too, with only the most useful pieces. I’d definitely have ordered a second (and third) fret.
-
Tried the decals by stealing some serials for another built - one disintegrated, the second came loose by its own while I was cutting the paper and had to be glued on with varnish. I’m therefore looking for alternatives. I have Print Scale’s balloon buster sheet, which contains E4071, apparently built by Vickers. I guess it had a Viper engine, but still haven’t found a photo or confirmation. If so I’ll have a go at one of McCudden’s Hispano-Suiza machines for the second model.
-
Progressing slowly. The cockpit is a bit tricky in the way it is assembled - I find I want to add bits in different order, but it’s not possible due to the model being split in three with two sides and an upper decking. The Part PE contains a full cage, but I cut it in 4 and removed the parts that won’t be seen. For the non-PE model I used hair to represent the ibternal bracing instead. Used the kit seats, but modified them a bit. The cockpit floor should be plywood as I’ve understood it, but I have troubles painting fresh plywood. I somehow managed with the non-PE but forgot how I did it The kit instrument panel cannot compete with the PE: And that’s before I even finished painting the PE part and adding the levers and other weee detail.
- 10 replies
-
- 10
-