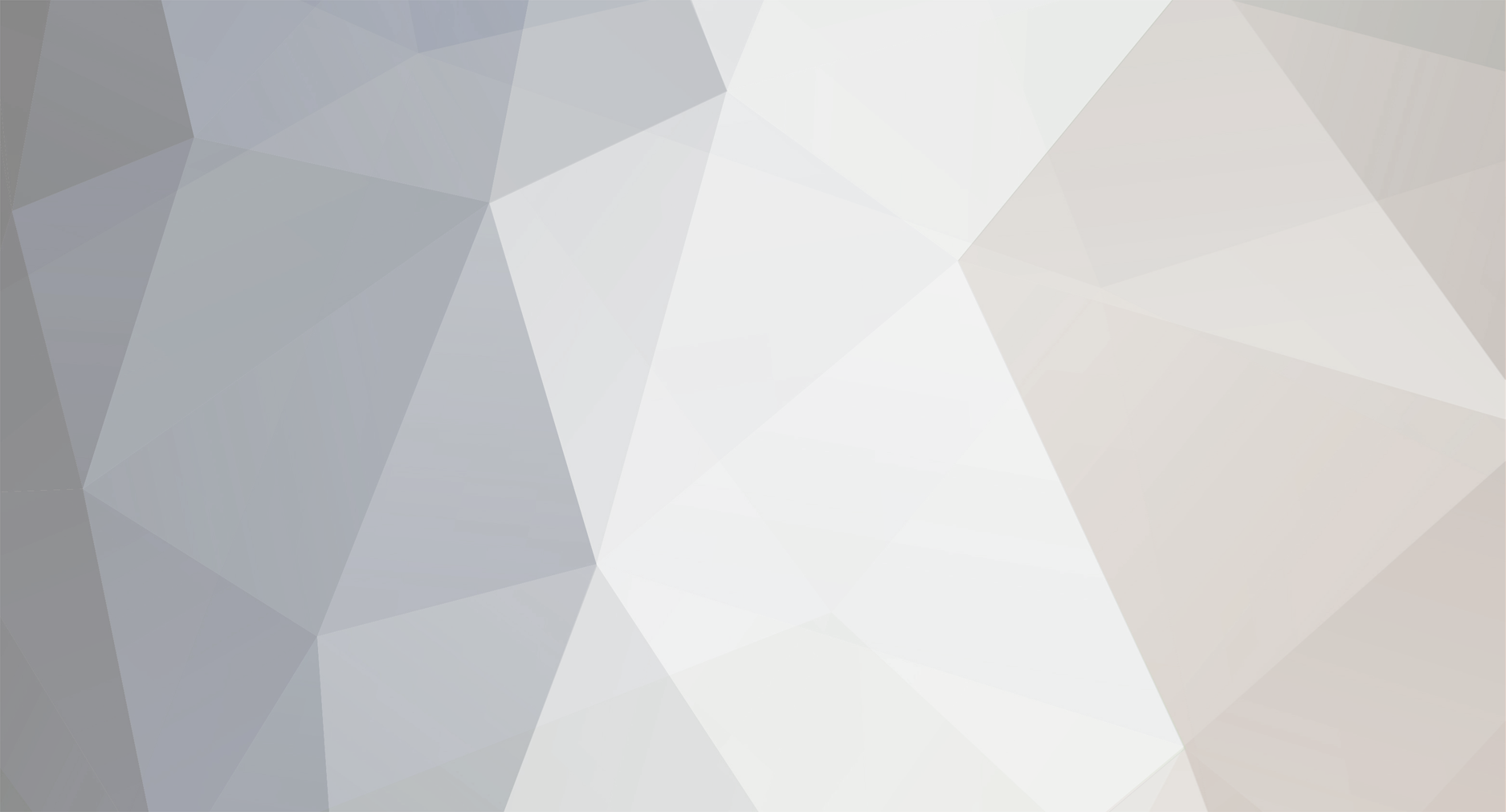
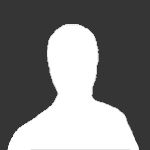
pheonix
Members-
Posts
2,145 -
Joined
-
Last visited
-
Days Won
2
Content Type
Events
Profiles
Forums
Media Demo
Everything posted by pheonix
-
1/32 scratch build Short Wright Flyer 1910
pheonix posted a topic in Ready for Inspection - Aircraft
Evening All, I have been building this since October 2024 and am pleased to be able to report that it is now finished. It is made from plastic sheet, strip, rod, brass bar and wood: there is a build log in the under cconstruction section for the masochistic among you. The figure of C Rolls was converted and painted for me by Steve Spooner who is a fellow member of my modelling club. The figure is based on a photo taken at the time of Rolls' historic flight and shows him in the life jacket that he wore for the occasion. In August 1908, Wilbur Wright demonstrated the Wright brothers’ new Flyer variant, (later called the Type A), near Le Mans in France. After taking many passengers, including C.S. Rolls, the latter placed an unconditional order for one. Wright had agreed that copies the Flyer could be built in France under licence, but Griffith Brewer negotiated all of the British and Empire rights on Wright’s machines and managed the UK patents on Wright’s behalf. Brewer, like C.S. Rolls, was a keen balloonist and member of the British Aero Club who was well acquainted with the Short brothers who had been manufacturing balloons for members of the club and the army since 1902. Brewer recommended the Shorts to Wright as potential builders of Flyers under licence in Britain. The result of this was that a contract was signed for six machines, all for members of the Aero Club: the first was reserved for C. S. Rolls. Rolls was unable to take flying lessons with Wright in France, so the latter suggested that a Flyer be built by the Short brothers without an engine, which he could use to learn to fly. The glider was constructed by Shorts at their factory in Battersea in four weeks during the spring of 1909, and was taken to the Aero Club’s new flying ground at Shellbeach on the Isle of Sheppey in Kent where it was covered in fabric and the final rigging completed. Rolls practised flying from Stamford Hill Eastchurch - a site that he leased for the purpose as it was the closest suitable hill to Shellbeach. (Later in early 1910 this site and adjacent land was bought by the then Royal Aero Club as a new flying ground - it later became Eastchurch airfield). In December 1908 Wright moved to Pau in southern France and allowed Horace and Eustace Short to measure and sketch the Flyer in February 1909. On their return to the UK Horace Short and P.H. Jones produced the first complete set of working drawings of the Flyer. Meanwhile the Aero Club had bought the landing ground at Shellbeach and the Short Brothers built a new factory 1/2 mile away to assemble the Flyers as the premises at Battersea were too cramped. The factory at Shellbeach was soon found to be too small, and by August 1909 a second unit had been built. The first production line for aircraft was thus established on an relatively remote island off the north coast of Kent: in August 1909 it was employing over 80 men. The Short Wright Flyer was a three bay biplane with a forward elevator on outriggers which were attached to landing skids. The pilot and passenger sat side by side with the pilot on the left and the engine to the right. Control of the flying surfaces was by levers: the fore-aft elevator control was on the left and a universally pivoted lever on the right moved fore-aft to control the rudder and sideways to warp the wings. A 27hp engine designed by the Wright brothers drove two propellors through separate chains in guide tubes and sprockets. Take off was from a trolley fixed under the landing skids which ran on a launch rail. Assistance in take off was provided via a rope hooked to the trolley and pulled by a falling weight which had previously been raised on a derrick downwind of the rail. Later machines built in France had wheels attached to the landing skids, but Rolls made his historic flight in Short Wright Flyer No 6 which did not have wheels. C.S. Rolls gained a degree in Mechanisms and Applied Sciences from Trinity College Cambridge. He was a founder member of the Aero Club of Great Britain in 1903, which at the time was a ballooning society. He made over 170 balloon flights and in 1906 won the Gordon Bennett Gold Medal for the longest single flight time. He started one of Britain’s first car dealerships, importing French and Belgian cars: he owned a French car himself. In May 1904 he met H. Royce, another car dealer, and in November they agreed that Rolls would take all of the cars that Royce could produce. 2 years later the partnership was formalised as Rolls Royce Ltd. Rolls bought the first Flyer to be built by the Short brothers and flew it extensively, winning several prizes in the process. He gained the second pilot’s license to be awarded by the Royal Aero Club. (The first had been awarded to J.T.C. Moore Brabazon). Later he also bought Flyer No 6 and donated No 1 to the Army at Farnborough. He established a flying ground at Swingate Down, east of Dover Castle and erected a hangar and launch rail there in early 1910. The field was leased from the War Office and later became Swingate airfield which was used by the Royal Flying Corps during the First World War: the RFC squadrons flew from Swingate to France in August 1914. It was from Swingate Down that Rolls made his most famous flight - the first non-stop return crossing of the English Channel in an heavier than air machine on 2 June 1910. The flight started at 6.30 pm and crossed to France approximately 1.5 miles east of Sangatte at around 7.15 pm (UK time), and flew approximately 1/3 mile over France where he dropped a message to the French Aero Club. He returned to Dover at 8.02 pm. The event was witnessed by a crowd of around 3000 people. Rolls claimed no credit for the achievement - all he did was to sit at the controls and let the machine take him! It was he said, a credit to the Short brothers and their high quality engineering. Rolls bought the third French Flyer to be built which had been fitted with a wheeled undercarriage, and he flew this to Bournemouth in July 1910 for an air competition. Prior to the start of the competition Rolls had a controllable elevator fitted to the rear of the rudders, and it was while he was attempting to make a rapid descent on 12 July that the tail boom distorted and touched one of the propellors with tragic consequences. Rolls was 32 years old when he became the first English person to be killed in an aerial accident, and the 11th in the world to be killed while flying. Today there are two statues of Rolls. One is in Agincourt Square, Monmouth, where he is shown holding a Wright Flyer, and the second is on Marine Parade in Dover, below Swingate Down, and shown here. There is also a memorial window in Eastchurch parish church. The model is now on display at Eastchurch Aviation museum close to where Rolls learned to fly his glider and from which ground he made many other flights. Thanks for looking. P. -
1/32 scratch build: Short Wright Flyer
pheonix replied to pheonix's topic in Work in Progress - Aircraft
Evening All, When Rolls made his historic first return non-stop crossing of the English Channel, he had floats strapped to the underside and front booms in case he needed to ditch in the sea. Looking at the photos I estimated the size of the floats and covered two pieces of dowel and two pieces of plastic tube with crepe paper. I painted them grey to try to represent canvass covering - I suspect (but do not know), that the floats were some form of covered air bag because the Short Brothers had been making balloons for many years. In any event the photos of the aircraft show some form of fabric covering. The floats were tied to the airframe with thread as on the original machine they had been secured with rope: The last major item to add to the airframe was the front biplane elevator. I had already made the flying surfaces and struts but I added the rigging first by drilling holes in the "solid" parts of the elevator surfaces. I cemented struts into the "solid " parts of the elevator surfaces and allowed these to set before the lower elevator was slotted over the left horn, (the right side had been broken off earlier in the build). The right horn was CA'd in place and supported with a conventional jig while the CA set properly: When this structure was secure I could add the upper elevator, the central struts and then rig the whole. The boom supports from the wings to the undercarriage skids were made from 30 x 40 strip: The early Flyers including the six built by the Short Brothers were launched from a wooden rail: the machine was mounted on a simple dolly which was attached to the skids and fell away on take off. I made up one of these from plastic strip with rod for the rollers: The above image was taken before I had touched in the paint! To complete the model I finishes attaching all of the remaining rigging wires - mainly anti-drag wires to the front and rear, and some bracing for the rear elevator. One of the last items added to the model were the propellors - these had been carved from wood and stained. The above image shows the completed model before I mounted it on a base. I want to show the aircraft as it would have been prior to take off for Rolls' historic flight so I made a launch rail from basswood with wood strip for the ground supports: The base was made from hardboard mounted on a wood frame, painted and covered with 2mm static grass. The rail was glued to the base: Two trestles were made from strip wood to support the wings and stabilize the model on the launch rail. Finally the model could be placed on the trestles and rail and was considered finished: I will post more pictures and notes in due course in the RFI. The light has not been good today and the weather windy so I have been unable to take photos outside but I am hoping to have more luck tomorrow. In the meantime, thanks for looking. P -
Scratch built Short S39 Triple Twin biplane.
pheonix replied to pheonix's topic in Work in Progress - Aircraft
Evening All, have fitted the undercarriage, but forgot to take photos of the stages. Briefly the skid and struts are 20 x 30 strip which has been bent to shape (skids) and filed to aerofoil section (legs). The wheels are Eduard PE centres and the tyres 30 thou rod wound around a paintbrush handle and then immersed in very hot water to make a coil. The vertical struts were attached to a skid and the struts inserted into holes on the underside of the wings. The bracing struts were attached and the sub-assembly set aside to dry out, before I repeated the procedure on the other side The axle is brass rod and was CA'd to the skids and the wheels added last. The units were rigged with rolled copper wire. The rear engine was cemented to the rear of the fuselage nacelles and the propellor glued in place with CA as this will be difficult to reach when the booms have been rigged. I attached the chain drives from the front engine to the prop shafts using thread which I wound around a pin which I had previously glued in the front of the nose. The chains exited via the holes in the fuselage sides seen in earlier pictures. The stabilizing rods were made from plastic rod. The engine was cemented to the pin and the front of the cowling opening added: The booms have been rigged and the horizontal tail surface CA'd to the top of the rear of the booms. I also added the front booms and elevator: Thanks for looking. P -
Scratch built Short S39 Triple Twin biplane.
pheonix replied to pheonix's topic in Work in Progress - Aircraft
Evening All, Thanks Stuart for the kind comment - much appreciated. I have been rigging recently using my preferred method with rolled copper wire and CA. It all works fine when the CA works quickly, but it can be a trial when it does not. Fortunately it seems to be working well at the moment. I have added the struts under the upper wing overhang and then rigged them, followed by the fore-aft and rear interplane struts. These are the least accessible and I usually rig these first on my models, following the principle that if the least accessible is rigged first, the task becomes progressively easier. It also means that damage is less likely: I have also started to put in the supports and drive shafts for the forward propellors. These were made from 30 thou rod and painted black because that seems to have been the colour looking at photos, but I could be wrong. Note that the drive shafts were directly attached to existing struts because this was a modification to an earlier design: Thanks for looking. P. -
Scratch built Short S39 Triple Twin biplane.
pheonix replied to pheonix's topic in Work in Progress - Aircraft
Evening All, Having allowed the outer interplane and end boom struts to set overnight, I proceeded to insert the remaining boom stuts with CA as the struts themselves are shaped plastic strip and the booms brass bar. I also added the control horns to the fuselage sides. The inner interplane struts were fitted and allowed to set. These struts were rigged fore-aft with rolled copper wire. One pair of fuel tanks had horizontal struts cemented to the sides and when all of the above was set I was able to add the fuel tanks to the inner interplane struts: The pair of interplane struts inboard of the outer pair were inserted between the wings before I fitted the final interplane pair: this was because the rear struts of the inner pair are longer than the others - they pass through the wing and will form part of the undercarriage. Using this method of fixing longer struts will hopefully create a stronger undercarriage. The second pair of fuel tanks were fitted with horizontal struts and attached to the interplane struts. Once again I had rigged the fore-aft wires of the inner interplane struts with rolled copper wire before I fixed the fuel tanks in position. While I was adding the interplane struts I also added small pieces of stretched sprue between each strut pair to represent the re-inforcing ribs which were exposed on the underside of the upper wing: Thanks for looking. P.- 14 replies
-
- 14
-
-
-
1/32 scratch build: Short Wright Flyer
pheonix replied to pheonix's topic in Work in Progress - Aircraft
Evening All, Many thanks Chris and Alex for you kind comments. I have been building a second model recently for a GB on another site, (there is a separate build thread on this site if you are interested), so radio silence has been the norm on this build as I have only been able to work on this between times. However progress has been made. The supports for the forward skids and horns on which the front elevator was mounted were made from 40 x 60 thou strip. These were CA'd at the bottom where they are fixed to the brass bar skids, and cemented at the top where they are joined to plastic: I have also added the clock which hung from one of the bracing wires near the pilot's head, but this is not visible in the photos. The control rod for the rear elevator ran from the left lever to the rear where it was connected to a horizontal bar: another control rod ran from the horizontal bar to the rear elevator. When the pilot moved the left lever forwards or rearwards the elevators at the front and rear would operate together. The rod from the left lever to the horizontal bar was fixed in place followed by the rear elevator. The elevator was supported by vertical struts - these were made from wood which had been filled with grain filler. A hole was drilled and enlarged on the fabric covered part of the elevator, and a gap cut in the spar on the uncovered side: The control rod from the elevator to the horizontal bar at the rear of the lower wing has been inserted but is not yet fixed in position: The side of the boom will be rigged when the control rod is permanently fixed. I have also put on to the lower exposed wing section the tip bar and trailing edge "wire" - the latter is stretched sprue: I am hoping that the next post for this project will be the last one - light is clearly visible at the end of the tunnel! Thanks for looking. P -
Scratch built Short S39 Triple Twin biplane.
pheonix replied to pheonix's topic in Work in Progress - Aircraft
Evening All, Thanks Stuart for the kind comment which is much appreciated. I can assure you that although the aircraft looks comples, if it is broken down into sub-assemblies it is not as daunting as it looks at first sight. I hope that this construction log will demonstrate what I mean. I have painted all, (or almost all), of the parts ready for assembly. The fabric parts were coated with umpteeen, (I lost count!), layers of thinned acrylics - Revell white with Revell Beige 314. The struts were Revell semi-matt enamel (382), and the propellors are carved from wood strip. I also used Humbrol brass enamel for the fuel and oil tanks: The parts were laid out in the above image to show roughly the order from front, (on the left), to rear (right). Initial assembly of a pusher is important to get right - everything must be lined up accurately or the model will look odd later. Most pusher types had vertical interplane struts which makes alignment straightforward: a simple jig to keep the leading or trailing edges of the wings in line, and another support to keep the wing tips aligned is all that is required. Paint pots or thick books provide the material for the jigs. I did not photograph them for this build because I forgot to, but if you look up any f my previous builds you will see clearly what I mean. Setting up a simple structure that is robust enough to be handled but simple to assemble is also straightforward: I cement the outer interplane struts to the lower wing and try to get them as well aligned as possible. When the cement is partially set so that the struts can be moved without falling out, I put small drops of glue into the locating holes of the upper wing and gently lower the upper wing on to the struts. The boom at the rear has to be supported with a paint pot or other suitable jig, (a piece of wood, corner of a book), while the wings are aligned and squared with paint pots as described above. The middle strut of the boom rear was inserted first on this model - it was plastic strip and was glued to the brass booms with CA. Once the CA had set the corner struts at the boom rear were easily inserted and fixed with CA. This kept the rear for the structure rigid while the cement on the interplane struts set: When this sub-assembly has had 24 hours to set, the remaining struts can be carefully inserted between the wings and booms as the structure is surprisingly rigid. Thanks for looking. P. -
Scratch built Short S39 Triple Twin biplane.
pheonix replied to pheonix's topic in Work in Progress - Aircraft
Evening All, Thanks Ian and Chris for the comments - much appreciated. I made the front and rear booms from brass bar as the originals were from square section timber: Quick and simple to solder. I will prime them later. I made the fuselage nacelle by push moulding 30 thou plastic sheet which had been heated under a gas grill. I used a scrap of basswood for the male mould and plywood for the female. Unfortunately I made the sides a little too short so I had to trim them and add some card to lengthen the rear: a small piece of card was then glued to the rear to make the back of the nacelle. A strip of scrap plastic was added for the seat and a wheel for the pilot. I know nothing else about the interior and as so little will be visible I left it blank. The joints were filled and sanded and a cowling made from 20 thou card. The card was run between the blade of a pair of scissors and my thumb to make it curl, and then mounted on some stretched sprue formers glued to the front of the nacelle. When all of this was dry I added more filler and sanded it smooth. I forgot to take photos of these processes but the result can be seen below. Holes were drilled in the wings to take the struts and undercarriage later. When all the fuselage assembly was dry I epoxied one of the rear booms to the lower wing and supported it with a sophisticated jig while the epoxy cured: I used a slightly more complex jig to attach the rear booms to the upper wing: I now need to make the struts from plastic strip and carve the propellors from wood, following which I will paint as much as I can. Thanks for looking. P. -
Scratch built Short S39 Triple Twin biplane.
pheonix replied to pheonix's topic in Work in Progress - Aircraft
Unfortunately so do I....! I am hoping to be able to keep the two balls in the air, not least because I have reached the last stages with the Short Wright. But you never know! P -
Evening All, I am making this as part of a GB on another site while I try to finish the Short-Wright biplane. I do not normally take on two projects at the same time, but personal circumstances have prevented me from completing the Short-Wright by the time that the GB started. Hopefully I will not become confused as to what to do next on each project and I will be able to complete both before the deadline for the GB. I started by making the engines from plastic rod: Flying surfaces are easy to make and quickly result in something to show for the effort. The wings, tail surfaces, and rudders were made from 30 thou card with the leading and trailing edges sanded and filed to make them into aerofoil sections: The above shows the front elevator, wings, horizontal tail surface and rudders. The notches in the wings are where the booms will be fixed later. I have also started to make the propellors from wood - one has been carved, the fuel tanks - there were 42 fixed originally, later two more were added which were of a different shape, and the bench seat for the pilot and passenger. The fuel tanks were shaped from sprue and the seat from 40 thou scrap plastic sheet: Now I have to make the moulds for the fuselage nacelle. Thanks for looking. P
-
1/32 scratch build: Short Wright Flyer
pheonix replied to pheonix's topic in Work in Progress - Aircraft
Evening All, My belated thanks for all of the positive comments that you have left - I really do appreciate them even if I am slow to acknowledge them in writing: life has been more hectic than usual recently. The radiator consisted of a series of vertical pipes mounted on the leading edge of the lower wing with pipes connected to the engine. I had drilled a hole in the lower wing a put a pin in the bottom of the radiator to make a secure joint. The pipes were made from 20 thou rod and connected the engine to the radiator. There was a small battery placed on the lower wing on the port (left) side of the engine: a small cable connected the battery to the engine: The seat was CA'd to a frame made from 20 x 30 thou strip and the latter cemented to the ribs and solid part of the lower wing. A fuel tank was mounted between the inner interplane struts - the tank was made from plastic tube with card at the ends to block the hole in the tube. A water tank was also mounted between the struts and hung beneath one of the bars which held the fuel tank: A control bar which actuated the rudders extended from the control lever on the right side of the pilot - this was connected to a cross bar on the lower rear boom which in turn was connected to the rudders by control wires. The bar from the control lever and cross bar were made from 20 x 30 thou plastic strip: The rudders on the original machine consisted of a two wooden frames with a single sheet of fabric on the outer surfaces, joined with cross rods. I modelled the starboard (right) rudder with the fabric and the port (left) as just the frame. The fabric on the right side was represented with 20 thou plastic card and the frames made with 10 x 20 thou strip. 25 thou plastic rod was used to join the rudders and the whole rigged with monofilament thread: When the rudders were finished I mounted them between the ends of the central booms and connected them to the control wires from the bar on the lower wing: I have still to decide what to do next - either rig the wings and tie off some of the annoying threads or add the rear elevator and rig the rear booms: with several fragile parts sticking out and waiting to be knocked off or damaged I will need to consider carefully how to proceed. Thanks for looking. P -
1/32 scratch build: Short Wright Flyer
pheonix replied to pheonix's topic in Work in Progress - Aircraft
I am using clear monofilament thread - not sure of the size but I would estimate 0.1 - 0.2 mm. It is very stong and when pulled taught and secured with superglue does not sag. I might use EZ line on the rudder wires - not sure yet, but if I do it will not be pulled very tight - just enough to take out the sag. P -
1/32 scratch build: Short Wright Flyer
pheonix replied to pheonix's topic in Work in Progress - Aircraft
Evening All, Thanks Chris for your kind comment - it is much appreciated. I have had a checquered time recently, having been away twice in two weeks visiting family during holidays. In addition I found that the booms were not properly aligned after I have put the top wing in place, so I had to take it off and reset it - this time thing are properly aligned so I have been able to continue with the build. I finished the elevators by adding the ribs from 20 x 30 strip which had been filed to shape. The ribs were added to the spars and the leading and trailing edge pieces were glued to the tips of the ribs with liquid cement. The wooden frame of the elevators were painted the same colour as the remainder of the wood frame that would have been fabric covered on the real aircraft. I also made the rudders: one is the complete unit with frame and fabric covering (on one side only as per the original), and the other just the frame. These too have been painted. The control for the wing warping consisted of a lever which operated a rod: the tail end of the rod moved from side to side, causing tension on a control wire. I made the rod from plastic rod with a hole drilled to allow the control wire to pass through. The front end of the rod was inserted into a hole in the control lever and the assembly superglued into place on the airframe. The warping wire guides on the upper and lower wings were cut from 15 thou card and superglued into place once the warping wires had been threaded through them. The propellors were driven via chains which were channeled and protected in tubes. The chains passed over drives at the rear of the engine and wheels on the ends of the propellor shafts. The propellor shafts were supported by triangular structures mounted between the wings. I made the triangular supports and propellor drive shafts from brass rod which was soldered over a paper template: These were primed and painted before they were mounted between the wings. The chain covers were also made from brass rod which was soldered: these too were primed and painted. The drive wheels on the ends of the propellor shafts were made from 20 thou scrap card. [ The shaft supports were superglued to the wings and the drive shafts inserted and glued to the propellor shafts. Adding the longer chain drive from the engine to the prop shaft on the port (left side) required an unusual jig even by my Heath-Robinson standards. The chains around the drive wheels were made from stretched sprue. Next I will start to add the features surrounding the pilot: there was no cockpit as such as (s)he sat on a seat mounted on a frame on the leading edge of the lower wing. Thanks for looking. P -
1/48 Eduard Airco DH2 'Weekend Edition'
pheonix replied to Epeeman's topic in Ready for Inspection - Aircraft
Very nice to see a real aeroplane so well presented. As others have commented the rigging is first class, but so too is the general finish. Looking forward to seeing this one for real. P -
1/32 scratch build: Short Wright Flyer
pheonix replied to pheonix's topic in Work in Progress - Aircraft
Evening All, Many thanks Adrian, Chris and Tom for your kind comments - I very much appreciate them. It's official: the Short Wright model is now a real aeroplane, ie it has a spare wing! I made the struts from wood as I considered that plastic strip might not be strong enough. The wood grain was filled with a mixture of talcum powder and dope and sanded down, followed by a coat of dope and a light sanding. I used the same mix of acrylics on the struts as I had used for other exposed wood parts described in the last post. To hold the upper wing in place while I fixd the first set of struts was awkward because the solid part of the wing was quite heavy and had to be held gently in place with books! I also put a pot of paint between the rear of the booms to stabilize that part of the structure. Because the books completely obscured the card wing supports I have photographed the jig parts after the wing was in place but you can see their respective positions: As usual this is all very high-tech Heath-Robinson, as per my usual building methods, but it worked. The reason for the large gap in the centre of the front is that I am leaving the space clear so that I can more easily insert the engine, radiator, pilot's seat and frame and controls. I can however put in place some of the rigging to secure some of those pesky threads which seem to be permanently in the way. Thanks for looking. P -
Sorry to be late to the party but I have only just found this. A fascinating topic and a brilliant subject. If I can offer my two pence to the discussion..... I have push/plunge moulded many forms for pusher fuselge nacelles and flying boat hulls in God's Own Scaleand in other scales too. I find carving from either balsa wood or, (more recently), basswood (lime), is by far the simplest and cleanest solution, and not very expensive. (Being retired and on a low income I have to be economical with my hobby). Getting good cross sections is difficult - I cannot help much there but I find Mk 1 eyeball and photos are usually good enough in this scale. I use plywood for the female mould and 30thou styrene for the material. A little practice is necessary to get a good pair of moulds, (I make one half at a time from the same male mould), and as Adrain has suggested, I make the male mould about 1mm too small. The female mould is the exact size as taken from the side profile. Some cleaning/filling is necessary but a satisfactory shape can be quite easily obtained with a little practice. When I mention carving I do not mean using a knife. Use files and glasspaper and card profiles to check the shape - again simple, cheap, clean and effective. If I were making the wings I would cut them from card and add ribs using strip and Mr Surfacer filler. I have posted many build logs on different sites including this one - if you want some links pm me and I will willingly send them to you. Best of luck with this build - I will be following with interest. P
-
1/32 scratch build: Short Wright Flyer
pheonix replied to pheonix's topic in Work in Progress - Aircraft
Evening All, Many thanks for the very kind comments from those who have passed by. Painting has progressed to the stage where I can now continue with construction. (There are no decorations on this model - the aircraft was devoid of any markings - as typical for the time. Only racing aircraft had numbers - usually on the rudder but sometimes on the fuselage. In this case there was no fuselage...... and Rolls did not use this particular machine for racing). I wanted to represent the wooden parts that were covered in a different shade to those which were exposed, so I used a mix of acrylic white and Revell beige (314) for the ribs and spars and white and Revell Okre (88) for the wooden parts that were normally exposed: the contrast is not strong but as the airframe was made of of ash for the spars, booms and undercarriage and a mixture of ash and spruce for the ribs, the original contrast would not have been strong either. However the exposed wood parts would have been varnished, so I made those a little darker. The fabric surfaces were a mix of acrylic white and Revell beige (314)with even less beige in the mixture than for the wood: If anyone is wondering what the oddments are in the last image, they are the elevators. Half are represented as fabric covered and the other half will be exposed - only the spar is in place at the moment as I have still to make the ribs. There was a biplane arrangement at the front of the aircraft and a single elevator at the rear. The single booms extending from the wings support the rudders, the double booms the rear elevator. I have been busy making parts for where the pilot sat: a new seat, (the one shown before on this thread was apparently fitted to French built Flyers, and although Rolls owned one of these - indeed he was killed flying it in July 1910 - it seems most probable that he was flying a Short built machine when he flew across the English Channel), the frame on which the seat was fixed, and the control levers: The engine is now finished and has been mounted on blocks and a drip tray: The engine is approximately 2cm long x 2cm high. I am now ready to mount the top wing and struts and then I can tie off all of the pesky threads which are attached to the solid parts of the wings. Thanks for looking. P -
1/32 Whirwind (Finished) and Kotare Spitfire finished
pheonix replied to bigbadbadge's topic in Work in Progress - Aircraft
Like Adrian I have missed this thread so I have just spent some very pleasureable time reading through. The Whirlwind is in a scheme that I have not seen before, but the detail and subtle weathering are truly amazing. That must be a large model but it looks very much like a real aeroplane. P- 318 replies
-
- 1
-
-
- Special Hobby
- Kotare
-
(and 1 more)
Tagged with:
-
1/32 scratch build: Short Wright Flyer
pheonix replied to pheonix's topic in Work in Progress - Aircraft
Evening All, Many thanks Chris and Tomoshenko for your kind and encouraging comments - they are really appreciated. I have finished the wings at last. The lower wing had the ribs added to the port (left) side after the last post: these were slotted along the rear spar and secured with superglue: The three outer ribs were smaller than the remainder of the wing and had to be cut and shaped separately. I added a new rudder boom to the rear spar as the one I had fitted was too short for the reasons I explained in an earlier post. I secured the brass bar with superglue but I know that will not be as strong as a soldered joint so I am hoping that it will not fall off before I can secure it with the rudders. The upper wing was made in the same way as the lower: solid plastic for the covered part which had been sanded to aerofoil shape with an electric sander, ribs from 20 x 30 Evergreen strip which were sanded down and Mr Surfacer added to smooth out the rib sections. The spars were brass bar but this time I soldered a rudder boom which was of the correct length. Ribs and elevator boom were added in the same way as the lower wing and I have drilled rigging holes in both wing assemblies. All of the brass parts for both wing assemblies have been primed: I can now start painting these units prior to assembly of the upper wing to the lower wing and undercarriage. Thanks for looking. P -
1/32 scratch build: Short Wright Flyer
pheonix replied to pheonix's topic in Work in Progress - Aircraft
Evening All, Progress which up until now has been rather erratic, has taken off in the last few days as many parts which have taken a long time to make can now be assembled. However before assembly could really begin I had to add the horns on the front of the undercarriage legs which held the front elevator structure. Once again brass bar was used - this was soldered to the ends of the horns on the undercarriage skids: As already noted, the Short Wright machines were altered in many ways from the original Wright design. One of the changes was to add a boom to the rear of the airframe to support an elevator. This was basically an open box structure so I made up the upper and lower sections from brass bar. One of these sections was attached to the rear of the lower wing: where the boom met the rear spar I soldered the joint; where the boom joined the plastic section of wing I drilled a vertical hole into the top of the wing and then turning the drill on its side I scraped out a groove behind the hole. The groove was deepened further with a narrow square file until the forward end of the boom sat snugly in the upper surface of the wing - this was CA'd into place. To ensure that I had the boom at the correct angle to the wing I used a much tried and tested method. I drew a line on the side elevation drawing which touched the leading and trailing edge of the wing and carried it to below where the boom would attach to the elevator. I had to estimate the size of the elevator posts, but I could measure the vertical distance between the rear end of the boom on the plan and the horizontal line drawn from the wing as shown on this sketch: The distance "A" on the sketch was the measurement that I needed to set the correct angle of the boom in relation to the wing, and I could set up a jig accordingly: The wing assembly has been pinned to a block of balsa to hold it steady while the rear of the boom has been rested on a book which was the correct thickness for distance 'A' from the plan. The white blob on the rear spar is a heat sink consisting of a piece of tissue soaked in water to protect the plastic wing. Whoever said that scratch building pusher biplanes was difficult? NB the central boom which will support the rudders has not been attached at the moment because the one I had fixed earlier was too short: remember from an earlier post that I discovered recently how the rear section of these aircraft had been extended to improve longitudinal stability. I had soldered the original rudder boom but as that is next to the end of the plastic section of the wing I cannot solder a new one into place: instead I will have to use superglue and I am afraid that it may well be broken off during handling, so I am leaving that until a later stage of construction. The undercarriage skids and struts were fixed to the wing as follows. Where the skids are attached to the brass bar spars I could solder the joint. I tried to do this by placing the wing assembly on to a balsa block and holding the boom with pins, but after several unsuccessful attempts I had to retire hurt. After some thinking I decided to adopt a completely different approach. I drew a line on the wood block over which i could place the spars so that the location points for the undercarriage supports on the spars were placed over the pencil line. The wing structure was pinned to the balsa block and the undercarriage placed on to the location points on the spars. The forward end of the undercarriage was held between two piles of books - with large heavy books at the top of each pile so that the undercarriage structure could not move easily either. A set square was used to make sure that the u/c was vertical and the line on the block was used to correct the fore-aft orientation. The books also held the u/c in place while I was able to move freely around to solder the two joints: Another awkward operation completed with minimal fuss and the use of Jig Type B. The other half of the undercarriage was fixed by drilling a small hole on the plastic part of the wing and filling this with epoxy resin. I gently lowered the undercarriage leg into the resin and added CA to the front legs where they join the front spar on the leading edge of the wing. I only needed to hold the structure for a few seconds to allow the CA to set and the sub-assembly could be left to allow the epoxy to harden. All the above was done with a minimum of fuss and use of Anlgo Saxon language, (except when I tried and failed the first attempt to fix the undercarriage using pin supports), and required minimum amounts of skill. I repeat: pusher aircraft are not so difficult to make as some seem to think! Thanks for looking. P -
1/32 scratch build: Short Wright Flyer
pheonix replied to pheonix's topic in Work in Progress - Aircraft
Thank you all for kind, supportive comments. I agree with Adrian that there is nothing like working with materials - personally I find it therapeutic but I know that some people would find it intimidating, as I used to do before I gave it a try. Researching these early machines is fascinating because new facts keep turning up. I am also learning about the practical problems that the pioneers had to solve - sadly sometimes at the expense of their lives. It is sobering to reflect that they were exploring a new medium, flight, with very little experience to draw upon, no simulators, no sophisticated computers, just slide rules and knowledge of physics and engineering, and sheer brass nerve to give it a try! And to cap it all the engines were not very reliable either. P -
1/32 scratch build: Short Wright Flyer
pheonix replied to pheonix's topic in Work in Progress - Aircraft
Chris, Thank you for the kind comment. The wing ribs can still be used as they were not fixed to the spars on the old wing, and the ribs were much closer in size to the scale thickness of the wing. The new wings are much nearer to the scale thickness but still slightly over scale but that is simply because of the need for the model to be robust enough to be moved about. P