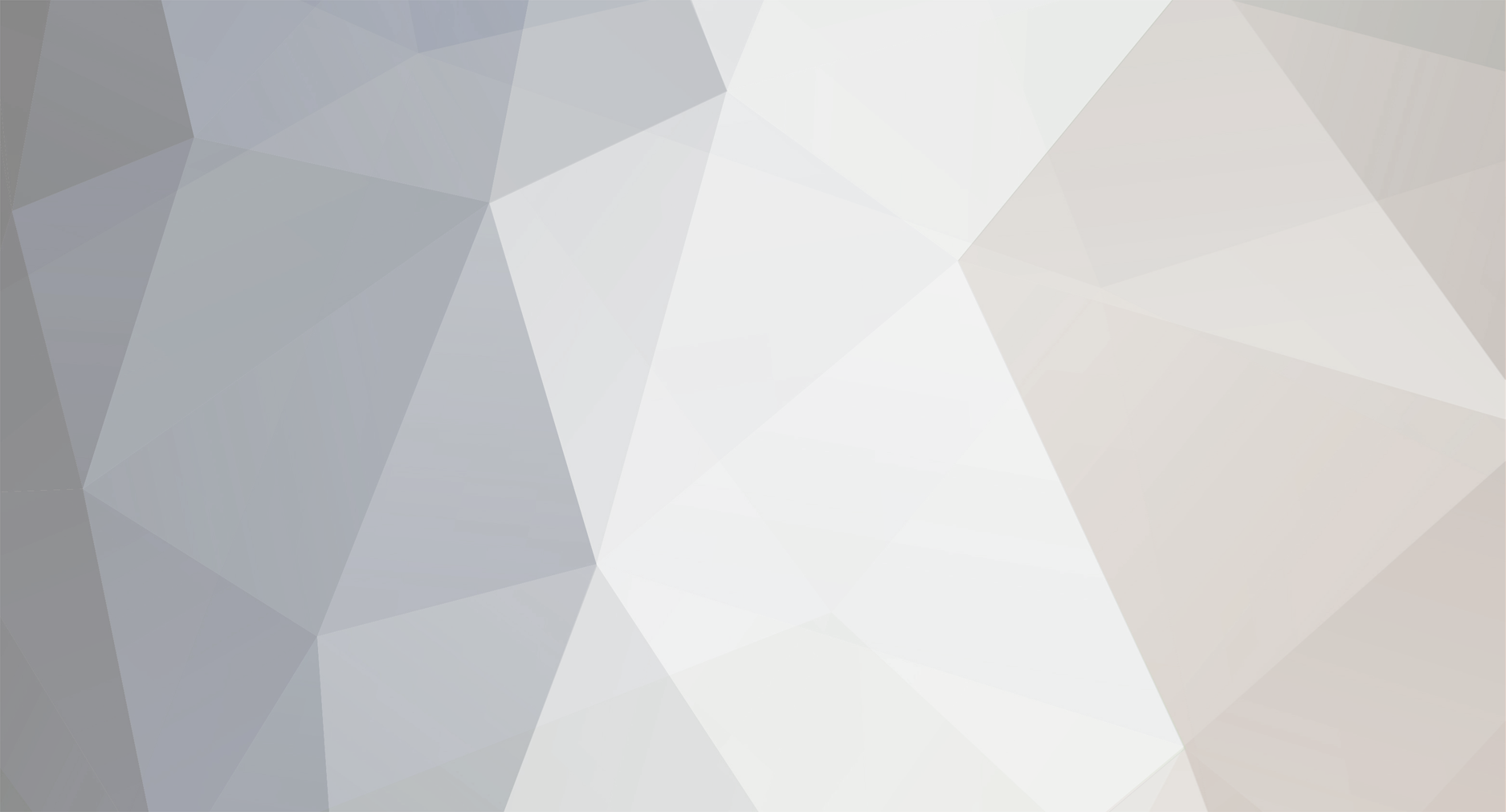
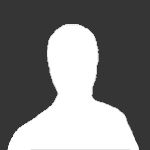
Torbjorn
Members-
Posts
1,432 -
Joined
-
Last visited
Content Type
Events
Profiles
Forums
Media Demo
Everything posted by Torbjorn
-
I picked up Eduard overtrees on their recent sale. I guess I’ll have enough time to find decals, so dfewl free to sign me up!
-
I can add a vote, but it’ll cost you one vote for Airco&co!
-
On the contrary that’s how I expect all colours to have been named. ”What colour was it?” ”The colour of grass”. I wouldn’t be surprised if someone told me ”green” is some pre-Babel word for grass and ”blue” meant ”sky” once upon a time. — On more important matters, I’m satisfied that Airco is in the fight again but utterly disappointed in the performance of the more esoteric subjects, especially Neutrality, Pillars of Fire, Names&Dames (what’s the ”names” part supposed to be anyway?) and Emergency. Aces High I would have expected to be on the superior side of the blue given how popular aces are in terms of subjects.
-
Modeller-friendly!
-
I accidently stumbled upon this set of completely random photos of completely random aircraft. Alas, if there only were a GB to build them in.
-
I would suggest to merge Sopwith with Airco/DH, though it probably the same suspects who vote for both anyway. And Neutralitity is certainly not popular in this day and age
-
Don’t. It wouldn’t work. I only accept bribes.
-
This is gonna be tricky, I have apparently signed up for almost all of them
-
Thanks guys! I haven’t forgetten her: she’s ready and waiting for me to find enough motivation to take pictures for the Gallery. I got hooked on other projects that are more fun than photography!
-
I like to start with the most difficult task so that if I fail, I don’t hve to throw away something half finished. This time I had to wait since I needed to finish the fuselage first. I’m talking about the windscreen/skylight, which has a smooth form curved in several directions. It’s very prominent, rather unique and defining of the type, so it’s important to get it right. Due to its complicated forn I decided to mould the whole topside with clear plastic - the clear parts can the ”simply” be masked. A male mould was made from round stock with the same diameter as the cowl mould to ensure an identical curvature, with a block of wood glued in place of the windscreen and sanded to shape. The pencil marks show the approximate location of the cockpit opening. The first try was a complete failure. I got some plastic from a food container - it turned an opaque white upon heating 😩 Guess I overheated it, or R-PET isn’t ideal. Or both. Will have to do some research and steal the secrets of the vacform canopy alchemists.
-
Small update. Wings almost done, still need to finish the edges and cut off the ailerons. That however makes them fragile (esp. the trailing edges if I make them thin, which I intend to) and delicate to handle, so I’ll wait with that. Looking at this photo, the outboard edges are too fat and needs trimming too. Chairs are in place, Douglas fits perfectly. The observer would need to straddle the pilot’s chair, but should be able to fit unless too stiff. Rather intimate and claustrophobic though. I made an instrument panel based on this photo: https://digitaltmuseum.se/021018816542/thulin-na-thulinavdelningen-pa-landskrona-museum Soon the fun begins!
-
Thanks Chris. I’m gluing the entire contact surfaces. Or rather, trying to. Out of laziness I’m using what’s available in my desk, which is Tamiya green label liquid glue, which is not ideal for the task. If you put too much, it will locally dissolve the thin sheet resulting in a start-over-from-scratch situation. If you use too little, it evaporates before you have time to press the surfaces together. I start with one side, glueing the leading edge, then little by little working my way aft. The upper surface is convex so it doesn’t matter much if you miss a spot as the sheet will be stretched, but if you don’t glue everywhere on the concave underside, you might end up with airpockets - you can see examples of this on the photo above - I was sloppy. With linen-covered wings like this you can sort of get away with that though (maybe a superflous observation - I guess this method wouldn’t be useful for non-clothcovered wings anyway ). Thanks - I’ve seen your wings and they all look the part. I have only tried that method for tailplanes, but only because I don’t have the patience to place all those strips on a full wing, and I find it difficult to sand one-part wings consistently (cores to be clad do not need to be nearly as pretty).
-
Apologies in advance for a long picture-heavy post. Finished most of the cockpit. Most internals were built up with scrap and plastic strips. The front underside had a curved fairing of sorts (to get rid of castor oil splatter?), almost identical to that of the Sopwith Camel. I sanded a block of plastic to its approximate shape and glued in on the deck: the outer underside can now be sanded out of this block to shape at some later date. As the photo shows, I’ve filled the aftermost section to make it robust. Not too happy with the wood paint: too much contrast, although the photo has exaggerated it. Since it will barely be visible I’ll leave it. As opposed to earlier Thulins, the NA was built with a metal tube frame, which I depicted with stretched sprue. The curved wooden frame were just to hold the curved wooden side panels in place. Currently waiting for the Milliput leather imitation in the seats to cure before I can do more. Douglas Bader is anxiously waiting to have a go. He’s my go-to sanity check regarding seat and control placement. He’ll likely have to remove his prosthetic legs to fit in the observer’s seat though: I’ve never seen such a cramped cockpit, but I have checked and double-checked and it seems to be as built. The foot-rests for the observer can be seen next to the stearing stick! —- Waiting for that I decided to make use of the rare sunshine… …by starting on the flying surfaces! I arrange a poor man’s drafting table by taping the drawings and some rulers to the window and rely on sunlight for translucency. I follow Woodman’s method of embossing ribs on a thin sheet and wrapping this ”skin” on an inner core. I’ve been dissatisfied with one part of my earlier builds and this is an attempt to fix it. The ribs look good on the upper side, but on the underside the linen will sag and the ribs look sunken rather than raised. Tried something slightly different now. I first embossed the upperside ribs with an ink pencil, like previous tries, but then flipped the sheet and *lightly* embossed theunderside with a ball tool (giving wider and flatter imprints) from the outside, so the ribs will be pushed in rather than out (but only slightly). Photo below shows the underside getting embossed: The result is this: The upper side has a reasonable wavy appearance while the underside (shadowy lower sude in the image) is flatter. This sheet was folded over a .6mm plastic core sanded and bent to an aerofoil shape. Here it is with the lower wing ”skin” freshly embossed: The underside isn’t perfect, but better than my previous tries so I’m happy: The reason I filled the aft fuselage is that I want to saw a slit for the empennage, made in one piece for the sake of robustness. This part is made by embossing .3 mm sheets (because Eduard Nieuport empennages measure 0.6 mm and I have no better input on the thickness) and gluing them together. This has the downside of having the leading and trailing eedges to repair, but I prefer that over having to add rib structure to a single piece. Here it is, glued, with the two rudder/fin halves made in the same way (I cut to shape only after joining the halves): The elevators will be cut away I think, haven’t decided yet.
-
As soon as I have found Draken decals for the F4 wing!
-
That’s exactly how my demarcation lines look when I use too much paint and rip off the masking tape too fast. I knew there was some use of this technique!
- 927 replies
-
- 10
-
-
-
Had a hickup: the spinners are two-piece affairs, and I sort of assumed the seam is where there should be a seam. That was wrong, I realized when checking photos to determine how scratchy these things were. These seams are very prominent, so I am trying some in-situ fillling and sanding: Otherwise I added some chipping (photos of Itsy Bitsy reveal there is no paint left on the leading edges) and oils. These things were extremely worn, but I’m always aftaid of overdoing it. Soon ready for the gallery.
-
Strangely I cannot find any photos of the Thulin G engine (annoyingly the Thulin works used the same alphabetic naming system for planes and engines and even cars - at least they switched to a Roman numeral system for the motorcycles!), but there are plenty of highly detailed Thulin A photos, which look almost identical to the Le Rhone they were reverse-engineered from. I suspect the G looks the same but with 11 cylinders. Here are some photos of the front of the NA: you can see details on 2-3 cylinders at the bottom, the rest is pretty much invisible. https://aeronavium.wordpress.com/2016/03/28/enoch-thulin-pa-landskrona-museum/ What you suggest is an option, but I wanted to try the method outlined by Woodman in his book: tightly wrap metal wire around plastic, bake it, and the plastic should partially smelt and fill the voids between the metal wrappings, thus creating cooling gills..
-
Thanks - though I still have to do something about the engine since it lacks two cylinders. I’ve never scratch-built a rotary or radial as I could not match available aftermarket, but since that bulbous spinner will block almost everything I don’t think it’s worth the money to buy a resin, even if one can be found. I’m considering just to find two spare cylinders (I have several Smallstuffmodels engines, and they usually have at least one spare cylinder) and rearrange the one on the picture. Thanks - but so far it’s only cutting plastic, I assure you that I’ll slow down soon enough
-
Thanks - I hardly expect anyone to have ever heard of this plane. It didn’t achieve anything exceptional, or introduce anything new. I’m only making it due to a certain fascination of Thulin, and this marks the end of his work. And the GB supplied the extra mojo I need to make a prototype, which I otherwise have little interest in. I’ve started. The fuselage will be built up by flat pieces of sheet for the bottom and linen-covered aft section. By printing two drawings, I use one to cut out panels and cross-sections that I glue directly onto the plastic sheet. I usually try to make some cut exactly, while the rest are cut overly large, to be trimmed to size after attached. The front side panels were wooden panels, bent to transition from a straight side to circular, to conform to the circular engine cowling. This is a construction that Thulin had used for many previous types, and I could reuse the moulds I had previously made for a Thulin D. The topside will be trickier. Anyhow, here are the pieces. The port side side panel hasn’t been cut. The used mould on the right. A surplus Le Rhone from a Roden Camel will be used for dryfitting and aligning the front parts. The NA used what was basicly an 11-cylinder version of this engine of almost the same physical dimensions. Glued all but the port side front panel. Need to leave access for construction of internals, but need one panel in place to keep the front firewall in place and avoid warping. This will be the smallest two-seater I’ve built.
-
edit: title was ”Thulin NA” - about halfway I got the impulse to add the N type the NA was derived from as well From the ceiling in a room filled with rotary engines and airplane models at the Landskrona town museum hangs a small biplane of 1919 vintage. The room displays a small exhibition dedicated to Enoch Thulin and his Thulin works (AETA) - a short-lived aviation company which went bust after Great war surplus flooded the marked and the demand fell. Despite its relatively short lifespan, Thulin laid the foundation of Swedish aviation industry, produced a dozen or so types, some license-built, some own designs. The preserved plane in the ceiling is the Thulin NA, the last of the lot. Only one prototype was built. First flight in April 1919, made a respectable 215 km/h powdered by its 9-cylinder Thulin G rotary. A bare month later, Thulin crashed fatally during a practice flight with an older design. With the market saturated and Thulin dead, the company was gone within a year. The NA ended up in the Landskrona museum as one of a few preserved Thulin aircraft. A photo here: https://digitaltmuseum.se/021018827355/flygavdelningen-pa-landskrona-museum-i-taket-flygplan-modell-thulin-na The museum measured and produced drafts of the plane, now available at the public Swedish digital repository. So, courtesy of Mr Göran Lundin and the Landskrona museum, I printed these drawings to produce the model from: After once having built a significant part of a model only to discover the drawings were scaled wrong, I now measure all drawings after printing and mark them with the actual scale as extra verification… The model will be built from plasticard and the usual scrap metal and, if I’m lucky, parts from the spares box.
-
Almost there… At some point I knocked off and lost both pitot tube and underside elevator balance, had to scratch replacements. Since this requires painting I fixed some seams I weren’t happy with. Landing gear in place, and she leans the right way. The missing bits and bobs are painted. I managed to glue one wrong prop blade on the wrong hub before I noticed they aren’t identical (in case someone else didn’t know: they spin different directions and the blades are mirrored along the centreline). Did some final painting based on the wonderful Life magazine photograph. The gray on the fins/rudders are what appears to be touch-ups made with the underside colour rather than olive drab. The exhaust stains were made with Vallejo Aged white, which seems to match the photo. Varnished and waiting for final weathering.