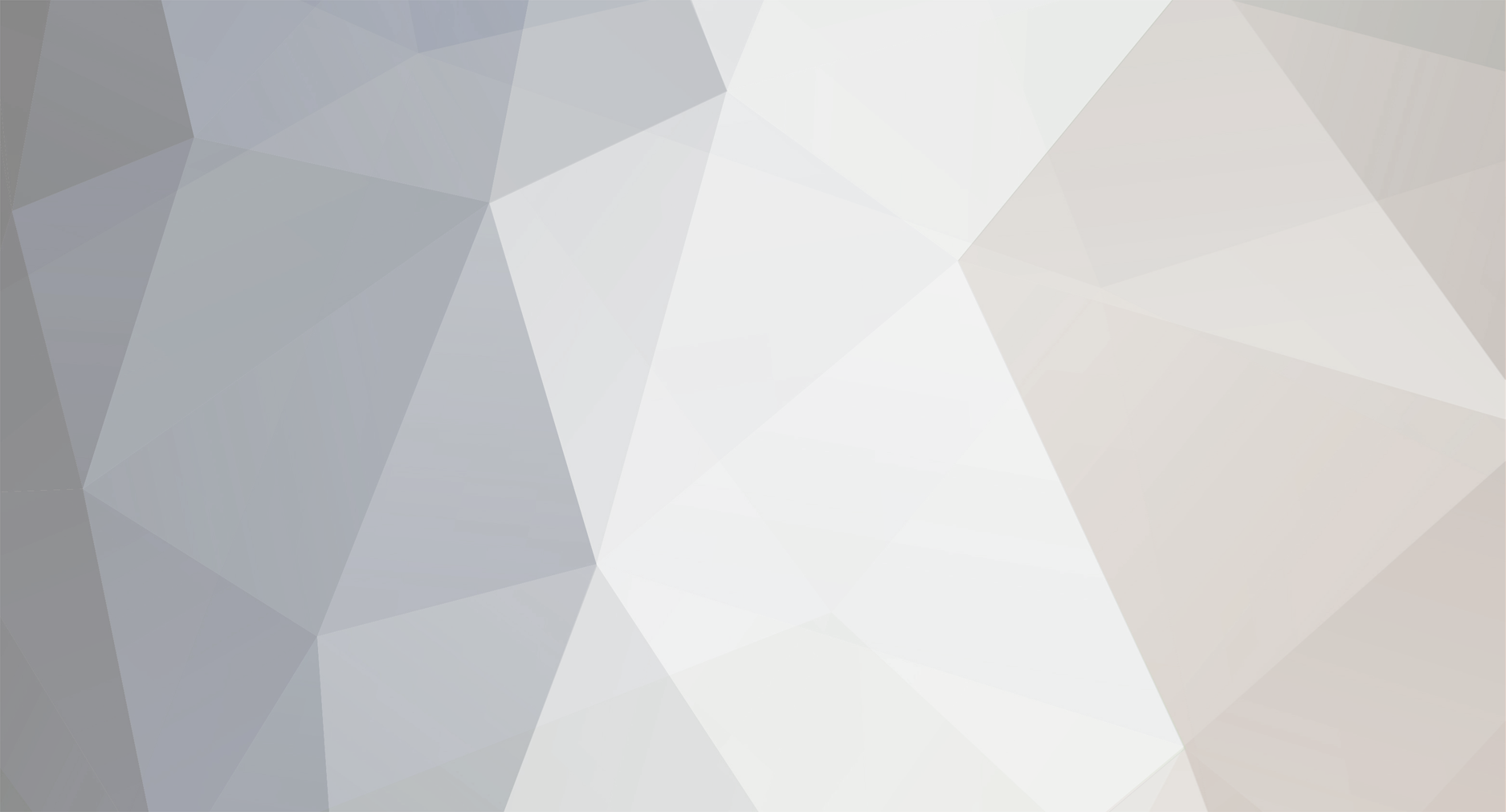
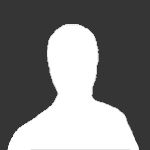
Tony Andrews
Members-
Posts
11 -
Joined
-
Last visited
Profile Information
-
Gender
Male
-
Location
England
Recent Profile Visitors
The recent visitors block is disabled and is not being shown to other users.
Tony Andrews's Achievements

Newbie (1/9)
8
Reputation
-
Blender can export STLs, amongst other file formats so just use File -> Export -> STL. One useful option in the dialogue is the choice to export everything or just the selected object(s). Without entering scaling information the size of the object will likely get lost but it's probably easiest to rescale within the slicer. Tony Andrews
-
For MakeHuman it is probably best to look at their own website or Youtube videos. First biggish challenge is connecting MakeHuman to Blender so a figure can be directly imported. Other than that, generating a figure is pretty much straghtforward other than navigating the convoluted menu tabs. The other integration, i.e. MakeTarget and MakeClothes look pretty involved and I haven't personally tackled them to any extent. Presumably adding clothes/uniforms is a priority - this can either be done in Blender by, e.g. posing the bare figure to use as a basis for sculpting the clothing around it - which will only be valid for the single pose - or learning how MakeClothes works, in which case one can form the clothing one time in Blender, export to MakeHuman, then import the clothed figure ready for posing. It's on my to-do list for sometime in the distant future. The only YouTube source I've found to be reasonably comprehensible is by VScorpianC. Neither of these options appear easy to me! HTH Tony Andrews
-
Have you applied a "rig" in MakeHuman? In MakeHuman you can select the "Pose/Animate" tab. Beneath this the "Pose" tab gives a (limited) number of options for the figure, and the "Expression" tab allows for various facial expressions. The "Skeleton" tab, however, inserts an armature which can subsequently be manipulated in Blender. If you add a rig you will see the basic bone structure showing up in MakeHuman. Import the figure to Blender and it will include an armature. Blender will now have "Pose Mode" available. Choose this and you can then select bones which can be manipulated using the normal Blender methods, e.g. "G", "R", "S". Normally reposing a figure would just involve "R"! Any large changes are likely to create "creases" on the surface which will need clean-up once the pose is set. HTH Tony Andrews
-
If you want a belt that exactly lies on the surface of the seat then you can try using project to surface. There are a few steps involved but it is fully parametric so very easily adjustable, unlike the form tool. Assuming your seat is roughly "L" shaped then you first need a plane that can "see" all of the seat parts where the belt lies. Look at the seat from the side and hopefully you are looking roughly along one of the origin axes (let's say X). In this case create a sketch (Sketch1) on the Y-Z plane and imagine a point that can see all of the front of the seat rear and the top of the seat base where the seat belt will lie. From this point draw a line (Line1) towards the centre of the seat and another line (Line2) perpendicular to this. Close the sketch, select Line2 and choose plane at angle. If necessary adjust the angle so looking at the plane will see all of the seat where the belt will lie. Create a sketch (Sketch2) on the new plane and draw the shape for one side of the belt section - line, arc, spline as needed, imagining that it is laid out on the seat behind. Offset this line by a suitable amount for the width of the belt then draw lines between the ends of the two curves to close the shape. Close the sketch. Now pick any plane you fancy and create a new sketch (Sketch3). Choose Create -> Project/include -> Project to surface. Select the face(s) where the belt will lie, then the four lines in Sketch2. Choose Project Type=Along Vector then direction is the first line drawn in Sketch1. Now there will be a suitable shape drawn on the seat. I think the best route now is to go to the surface tab and Create -> Patch. Pick the lines from Sketch3 and you should get a surface body laying on top of the pre-existing seat. Finally use Create -> Thicken to make a solid body representing the belt sitting on the seat. If desired bevel or chamfer the edges. As appropriate use mirror to get left/right elements and maybe build the belt up in sections, merging the parts together later, Hope that makes some sense. Now, if you want a fabric finish on the belt then Fusion is probably not the best tool. Blender, which is totally free, can do the job really well except that the learning curve to use the program properly is unbelievably convoluted. For a job like this, you can 1. export the belt from Fusion as an stl, 2. import to Blender, 3. find a suitable texture file online, 4. apply this texture to the belt. There are only a few steps here: 1 and 2 are trivial, 3 is not hard, but step 4 involves numerous selections each with a gazilion options. I can try to describe a process if you want. Tony Andrews
-
Designing/Printing humans - anyone know how?
Tony Andrews replied to bootneck's topic in 3D Printing Chat
It would be worth looking at Blender (free) or ZBrush (limited version free for personal use). These programs are both designed, amongst many other things, for sculpting figures. Tools are available for creating figures and clothes. Intimately linked to Blender are MakeHuman and MakeClothes. These may well also work with ZBrush but that's way beyond my limited experience. MakeHuman allows you to create pretty much any human figure you could imagine. If you include a skeleton rig then the figure can be posed in Blender. MakeClothes allows clothes to be designed and, if done correctly, these can also be posed along with the figure. Blender has incredible capabilities but is also UNBELIEVABLY non-intuitive for a beginner. Try these for starters: https://www.youtube.com/watch?v=nIoXOplUvAw https://www.youtube.com/watch?v=jnj2BL4chaQ For MakeHuman: https://www.youtube.com/watch?v=WiEDGbRnXdE (this is an older version and some aspects have changed significantly) Biggest issue with Blender is identifying the 1% of its capabilities that you actually need. However, as it's free and has a large user base, there are a lot of resources available. As a very trivial start you can do the following: 1. Run MakeHuman to play with a figure design starting from its default. 2. Select the "Pose/animate" tab - pick "MakeHuman" on the left then "Default"on the right which creates the skeleton structure. 3. You can also put on some basic clothes if you want - "Geometries -> Clothes" then pick options from the left and right sides. 4. Send this to blender either by exporting from MakeHuman (as an mhx2 file) and importing to Blender or via its built-in direct link. 5. In Blender select "Pose Mode", choose a bone, press "R" (Rotate) and move the mouse to change the pose. HTH Tony Andrews -
Help please on drawing this vehicle cab in Fusion 360
Tony Andrews replied to bootneck's topic in 3D Printing Chat
I would think you should be able to make it with lofts and suitable rails - probably in a few stages, e.g. the lower "bulge", upper bonnet and cab. For example to do the lower part of the cab unit use the top view to draw the outside shape of the lower part on one sketch just above the front bumper then draw the upper shape on an offset plane at the join line half way up to the cab windows. If you then add sketches based on the side and front views you can draw curved lines connecting the top and bottom planes to use as rails for the loft. Alternatively you may want to exp;lore surfaces or forms if you haven't already. Surfacing potentially allows easier generation of smooth thin curved faces whiich can then either be built up into a uniform thickness, stuck together to form a solid, or used as a cutting tool to cut up a solid body. The form tool allows sculpting of very "organic" objects albeit with limited "reversibility". Try looking at a few youtube videos on "Car modelling" or "T-splines". Tony Andrews -
If you were to buy an SLA printer today ?
Tony Andrews replied to nheather's topic in 3D Printing Chat
Looking at entry level printers, the Photon build plate has a ball joint to allow angular adjustment but has no Z-axis play. Therefore you have to drive the Z axis gently to the desired position, tighten the ball joint and then set this position as zero on the controller. The Mars has a sprung loaded joint which means it can allow for variations in the Z axis and you just have to loosen the bolts, set the controller to go to home, push down to help the springs align the plate, and tighten the bolts. The Mars 2 is similar to the Mars although the instructions now suggest making small Z adjustments after tightening the bolts and then setting Z=0. The Photon Mono and Mono X have 4 bolts on the build plates which slide in slots allowing for variation in the Z axis but, unlike the sprung-loaded Mars, not helping to push the plate onto the levelling paper. Once you are confident I don't think any of them are particularly more or less difficult than the others. If you use the machine sensibly there seems very little need to keep meddling with the alignment anyway. The Mars has the USB slot in the centre on the rear. This seems really inconvenient for access but does reduce the chance of knocking it accidentally once it is installed.. The Photon and Photon Mono have the USB on the side towards the rear. The Mono X has it the side towards the front and the Mars 2 has it on the front. If you really want the connection in a particular place it is not hard to find a USB extension cable and work out a way of attaching it. I have my printers in trays and just secure the socket of the USB cable onto the sides with bulldog clips. The Mars and Photon have very similar slides for the Z axis. Those on the Mars 2 and Photon Mono are the same style but seem a bit more robust. The Mono X has two guide rails so should be more stable. This is an area where the more expensive printers, e.g. Mars Pro, are an improvement. HTH Tony Andrews -
If you haven't already, it may be useful to look at components, assemblies and joints. Assemblies break a project into manageable elements (but all within one file). For a locomotive chassis one could create separate components for a frame, axle box, axle, wheel, connecting rod, etc. Once designed these components can then be readily reproduced and connected together using joints to form an assembly - e.g. two sides of the frames could be rigidly connected and axle boxes could be rigidly positioned in slots in the frames. Next wheels could be attached to the ends of axles which are then positioned in the axle boxes with rotational movement allowed and finally connecting rods could join the wheel sets, also with rotational joints. Once completed the wheels and connecting rods should be able to move correctly. As others have said, the 10 file limit is not really a serious issue for home users - it's only bad if you want a load of files open at once. HTH Tony Andrews
-
Expanding from the above to a less "Tonka-like" tyre that is quite quick to create and looks OK at scale, you can create essentially two sketches. One is a cross-section of the tyre/wheel that will be revolved around the axis. This needs two profiles - one to define the overall cross-sectional shape and another of the cross-section at the bottom of the treads. These two profiles can be revolved to give two separate bodies, "inside" and "outside", forming the wheel+inside part of the tyre and a "slick" tread respectively. The second sketch can be drawn normal to the first and contains the tread pattern - best to extend beyond the outside face of the wheel so it cuts nicely. You then extrude this to cut through the slick "outside" tread body and form one tread slot. This can be mirrored or patterned to create the inside/outside tread shape then copied around the wheel with the circular pattern. HTH Tony Andrews
-
Fusion 360 - how can I draw panel lines for 3D printing?
Tony Andrews replied to bootneck's topic in 3D Printing Basics
If you just want to put slots in the flat surface then the easiest way is to put a sketch on that surface and then extrude into the surface, which looks like what has already been done for the recesses for the blast deflectors. If you have simple straight lines then drawing rectangles is probably easiest with the width of the rectangles set to the groove width, e.g. 0.2-0.3mm. Any less will almost certainly not show up in the print - 0.2mm is only about 4 pixels . If the pattern is more complex then it is probably best to draw the shape as a line then offset +/- by half the groove width and join up the ends of the lines to make an extrudable shape. The depth of the groove is controlled by the extrude. The profile of the groove can be tweaked by applying an angle in the extrude and/or adding fillets or chamfers to the outside edges or bottom corners of the groove. If there is a regular spacing then you can use the rectangular pattern to reproduce one groove either by copying lines in the sketch or features in the 3D body. Again, you have probably already done this for the structure on the back of the blast deflectors. HTH Tony Andrews -
Fusion 360 - how can I draw panel lines for 3D printing?
Tony Andrews replied to bootneck's topic in 3D Printing Basics
I don't proclaim much expertise but here's a few options. None are very pretty and all have limitations. 1: Emboss. Only if the surface of the body is not too complicated (2D curves extruded are probably OK, 3D curvature probably not OK). Create a sketch and draw some long thin rectangles with the width you want. The positioning can be adjusted during the emboss process so the rectangles don't have to be aligned exactly right. Close the sketch and select EMBOSS. Pick the rectangles on the sketch and the face on the body then DEBOSS and enter the depth of the panel lines. Big pluses of this approach are that the position of the lines can be easily adjusted, the lines wrap around the body, and it is easy to apply a fillet if desired. Downside is that you need a relatively simple surface or it won't work. 2. Cut through a surface layer. Break the body into two pieces comprising its outer surface and the main bulk. One way to do this is to use SHELL to create the "skin" with the depth desired for the panel lines, then reproduce the original body and use offset face to move it inwards to fit inside the "skin". Next create a new sketch on a suitable plane and draw long thin rectangles to match the panel lines you want. Switch on only the skin body and extrude from the sketch to cut through the body. As the extrude only goes in one direction you cannot wrap around a body in one go so may need to do several sketches in different orientations to create a decent approximation, e.g. side, top, 45 degrees top-side, 45 degrees bottom-side. 3. Project to surface. Create a suitable plane, preferably in front of the body. Create a sketch on this plane and draw lines to match the panel lines. Close the sketch and create a new sketch (sketch plane doesn't really matter). use CREATE -> PROJECT/INCLUDE -> PROJECT TO SURFACE. Pick the face on the body, the lines on the sketch then ALONG VECTOR and choose a suitable axis (most likely normal to the sketch plane). This creates lines along the surface of the body which should match your panel lines. Next CONSTRUCT -> PLANE ALONG PATH and pick one of the lines on the surface of the body. Now create a sketch on this plane and draw the cross-section of your panel line, e.g. a rectangle with a rounded end. Now SWEEP this sketch along the line. This does a good job at fitting around quite complex shapes. The ends of the sweep may have glitches due to the 3D orientation of the path. This can be resolved by an extra cut at the end of the path. As a trick you could also add material to the body first so the swept path can be made longer, then project the lines, sweep the cut and finally cut off the extra material. Any better suggestions would be welcome HTH Tony Andrews