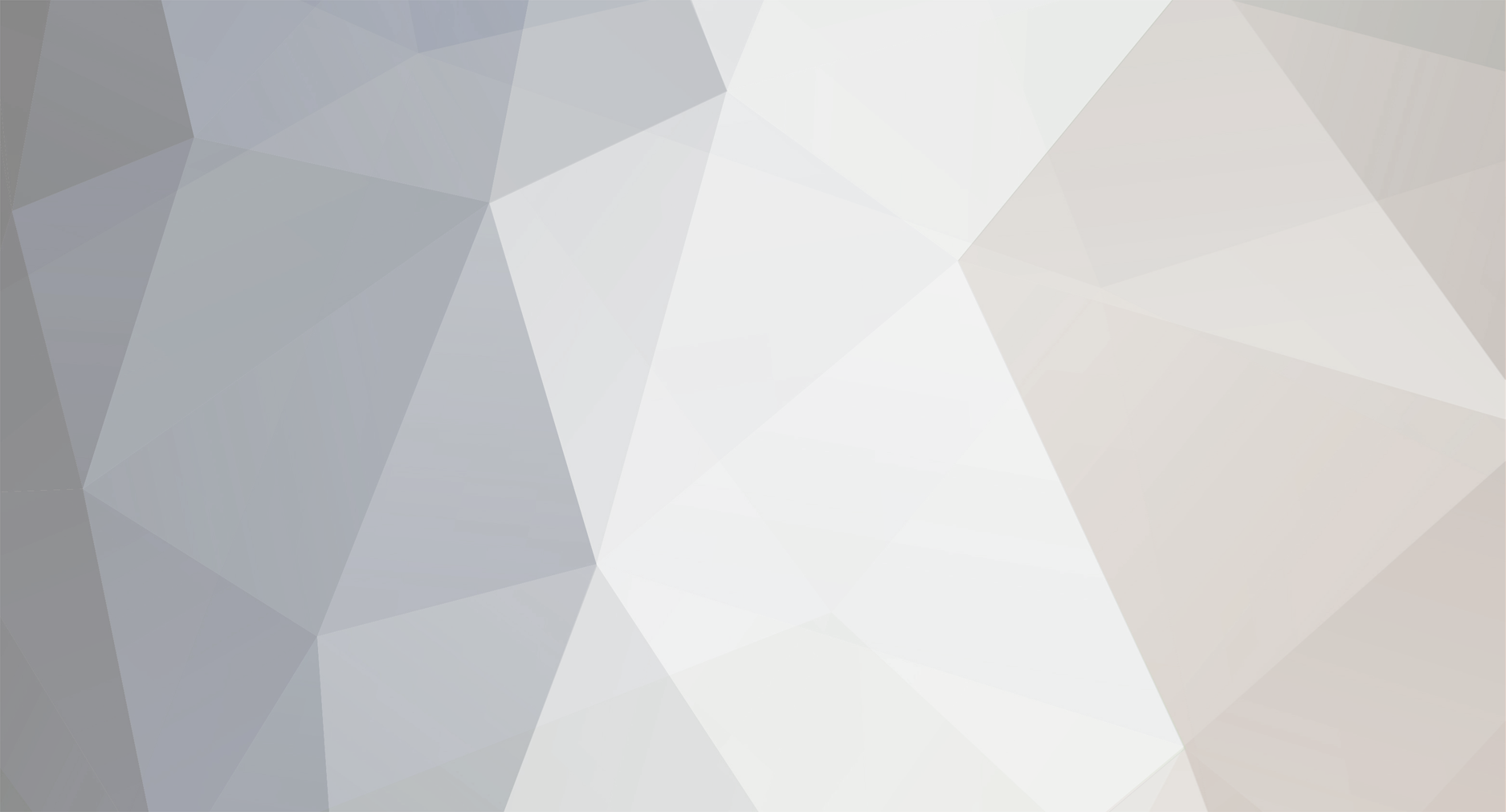
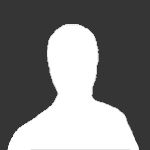
zibbit
Members-
Posts
52 -
Joined
-
Last visited
Profile Information
-
Gender
Male
-
Location
Victoria BC
Recent Profile Visitors
The recent visitors block is disabled and is not being shown to other users.
zibbit's Achievements

New Member (2/9)
168
Reputation
-
Great spit collection and congrats on the new workspace.
-
One UH-1N Iroquois and a terrible mistake
zibbit replied to chikavili's topic in Ready for Inspection - Aircraft
Beautiful finish on that Huey, what about contacting Italeri directly to see about sourcing the required parts? -
It's nice to see a Boeing door finally stay closed during a flight; although, it seems like there's a problem with the fuselage skin. 😛 Beautiful model, that would've been a chore to finish.
- 15 replies
-
- Boeing 747
- Revell
-
(and 1 more)
Tagged with:
-
Just a thought; but, for ease of printing you might want to consider parting the top of the cylinders off in the valley between the first two horizontal cooling fins. It might make the final product more stable during printing. I know my variant had lots of issues trying to print those perpendicular faces
-
I like that you're taking on this engine.. can't wait to see your results. My 1/10 attempt is almost complete. It took me quite some time to CAD up PJVision's plans, there were a few errors in his measurements that didn't line up with subtle items in the engine. More notably the cylinder head valve pockets would've been cut into the cylinder walls, and the cooling vanes weren't symmetrically lined up which I found weird. I attributed those errors to having to roughly measure actual parts without using 3d scans. My best advice, become extremely comfortable with the revolve command, and circular sketch pattern. That'll help out the modelling exponentially.
-
Nice to see the Merlin project is still progressing. My new job has got me so exhausted by day's end that it relegated my 9B project to a non-existent pace. One of these days I'll get back to it..
-
Nice job so far. Something to note with all F-18 variants, the main flaps will always droop after shutdown to almost their max angle. The elevon's will also always rotate to a similar position as depicted in your first reference photo; somewhere between the upper angle marking on the tail, and the position shown above. The rudders also can be moved by the wind, so the position isn't always the same. Unfortunately, I don't recall if the leading edge flaps droop or not.
-
Latina Sopwith Camel aftermarket build
zibbit replied to zibbit's topic in Work in Progress - Aircraft
BTW, does anyone know of a proper brass color that can be both brush painted and airbrushed easily? I'm having a HORRIBLE time using Vallejo's Model or Air Color acrylics even while using their branded "flow improver".. Basically the problem I'm having. I find the paints clumpy, and unable to stick/coat to any surface in anything resembling thin coats. I guess I got too used to using essentially ready to use Tamiya/Mr Hobby/AK acrylics. I find the Vallejo Metal Color lineup is phenomenal by air, and semi passable by brush; however, I cannot for the life of me get Vallejo's "Model/Air" Color lineup to do anything through my airbrush except clog it or push around clumps by brush. Thanks- -
Latina Sopwith Camel aftermarket build
zibbit replied to zibbit's topic in Work in Progress - Aircraft
Haha thanks, to be honest, every part has gone through the same scrpteneering process as those cylinders.. I just never documented it because that takes time away from the bench. You should see the size of the "throw away" bag of parts that I've developed.. it's starting to get ridiculous. I will admit after seeing some of the builds on this forum, pushed me to want to expand my skills and produce a higher quality final product. This is especially true with Twobad's magnificent 1:8 scale Merlin build... that thing is a work of art. -
Latina Sopwith Camel aftermarket build
zibbit replied to zibbit's topic in Work in Progress - Aircraft
With having a little extra time on my hands due to leaving my job, I was able to put in a few extra hours on this build. Now I'm at the exciting stage of adding color to the various components. I will admit, it's difficult to add contrast or interest to an essentially monochromatic subject. I mean the whole engine (cases & jugs) are built out of steel, brass and aluminum for the accessories, with copper intake runners. Instead I tried to focus on individual components and how they might look when they're situated immediately beside other components. The central cases while they're all built from steel are cast; therefore, I could paint them steel using Vallejo MC paints, then dulled them down with a matt varnish over the two components. The varnish isn't changing the color, but it's affecting the hue of the part. Anything that's spun steel or machined steel maintains its shine so those components will be covered in a gloss varnish. Bolts/nuts were brush-painted using Molotow Liquid Chrome, with a light wash of black & brown Tamiya Panel Line accent color to make individual components pop. I'm undecided if I'll re-print the lube pump then refinish the component. There's a few too many layer lines for my liking that are a little more prominent than I thought they might be. So for now, I'm going to leave everything unglued to the central support frame. The cylinders I got to play around a little more with color due to the heat they probably saw during service. Started with a Vallejo MC Steel base, followed by a light mist of X-13 Tamiya Metallic Blue near the top of the jug, followed by a downward angle spray of Vallejo MC Gunmetal Grey to make the cooling fins pop again. The valve rockers were painted using Vallejo MC Copper Ok, that's it for now.. Hopefully in the next short bit I can actually start gluing parts together. -
Latina Sopwith Camel aftermarket build
zibbit replied to zibbit's topic in Work in Progress - Aircraft
That support would've been tricky to separate from the part. I too was having adhesion problems, turns out I believe mine were temperature related. Printing at 20ËšC half of the prints would partially stick; yet, if the vat and build plate were at 25ËšC, everything would stick. I ended up installing a Chitu Systems heater on the back of the printer that was aimed at the removable exhaust vent on the cover. -
Latina Sopwith Camel aftermarket build
zibbit replied to zibbit's topic in Work in Progress - Aircraft
Topic for today: Cylindrical Woes. So I scaled back a little and reassessed what I was trying to accomplish here. Items I decided.. Concentrate on a clean build, not a technical marvel that's almost impossible to build. In saying that, I have simplified some of the assemblies to ease construction. Essentially, I combined the Intake Collectors to the Cylinder head. I'm still undecided if I'm going to have a moving piston because I think the whole engine assembly would become quite fragile just to see the piston move up/down in the jug if you strained your eyes hard enough to see it. As much as I'd love to have the thing move, I'm just not sure it's worth the extra effort in 1/10 scale. Next thing I needed to address, how to 3D print air-cooled Cylinders and still have a clean print. This is how many sets of cylinders I've printed thus far: I'll use a 5X illuminated magnifying loop to show you each result individually. Pardon the dusty loop. Keep in mind, each set takes anywhere between 3 - 5 hours to print regardless of how many items are on the build plate. Set #1: These ones were printed vertically in an attempt to minimize supports. It was great, I only had to add 8 supports around the unseen edge of the cylinder, and everything else self supported themselves. Unfortunately, you can see everything printed well, EXCEPT the circumferential cooling fins running all the way up the sides.. DOH!! Questions I had to answer.. did the cooling fin gaps become uneven because they were unsupported? Did they do that because the jug is solid causing weird tough/soft/tough pulls, thereby inducing layer shift? I didn't know.. All I could do was go back to the drawing board to try and solve WTH happened. Set #2: troubleshooting two's company, three's a crowd In order to answer the first question I had, I decided to hollow the cylinder model in CAD so it has a 1mm thick wall (not including the fins). You can also see that I added the Intake Collectors to the Jugs at this stage. To answer the second question I had, this time I chose to only print three models in different orientations on the build plate. The one on the left was printed vertically, the one on the right was printed at ~30Ëš, and the last one was printed horizontally. Unfortunately, the horizontal one failed to adhere to the build plate. Vertical print (left one).. while it's better than the first batch, it still shows some layer shift. Abandon ship!! Angled print (right one).. That one has even gaps on the cooling fins, however separating the cylinder from the raft/supports proved to be a nightmare.. Now I had to work on optimizing the support placements. Set #3: The widow's peak arrived. In an effort to minimize cleanup, this time around I tried one centralized row of small supports each grabbing each cooling fin. Combine that with the bottom ring of supports that I had before made for a model that separated easily from the raft/supports. Unfortunately, during printing, this caused some layer shifts to happen causing a sharp dip in the fins. At this stage, I did some test fittings of the rocker arms. I'm really happy how the arms fit, and best of all, they've got a ball socket hinge so you can position them however I want: Whether it be open, closed, or somewhere in between. Set #4: Step by step, Oh baby... The newly integrated step works well to locate the height of the cylinder in the cases to prevent myself from installing them too far inboard; however, I still had to do a wee bit of sanding to clearance the model which I'm ok with. Next I added beefed up supports on the lower hidden edge inside the cases to see if I could minimize the widow's peak.. Nope, that's didn't help at all. The widows peak is still there. Set #5: The peak is kinda gone, but now it's worse, but better.. WTH!!! Yet again this time around I had the model supported by the centralized row of small supports; however, this time I added four additional rows of staggered support pins on every third cooling fin.. Yeah.. the peak is kinda there, but now caused an entire stack wavy cooling fin that looked WAY worse than the relatively uniform widow's peak. Luckily, I could sand the wavy fins away revealing relatively straight fins. Unfortunately, this means the cylinders are no longer round and became ovalized. Crap, that'll show up in paint, so toss those cylinders in the bin. Set #6: Success.. well, kinda. For this print I used 5 complete sets of small supports for each cooling fin covering the bottom 1/4 of the cylinder. It seems to have stopped the wavy and/or widow's peak, however now I need to build a mandrel to mount the cylinder to my drill so I can lightly sand the cylinder to remove the leftover support that marked the surface of the cooling fins.. I can deal with that. Ok, that's it for now. Time for a pint- -
Brilliant work so far; it looks so realistic. Surprises me how large that QCU engine is seeing it next to the ruler/coffee cup. Hmm, I'd almost be tempted to try building it in 1/10 scale.. I mean how hard could it be at 80% size to what you've produced.. haha I think I'd be biting off too much to chew 😛
-
Latina Sopwith Camel aftermarket build
zibbit replied to zibbit's topic in Work in Progress - Aircraft
Haha thanks for the kind words heloman1. So I've almost consumed 1L of resin so far.. most were throw away parts for fitment checking. Here's what I've got printed so far: I find it hilarious that you can actually see the spark plug electrode on the end of the plug. Or read almost everything that's written on the front case data plate. I decided to combine the UK variant nose-piece, hub flange, and added the prop retaining bolts as I wasn't planning to model a propeller, I think it looks best with the prop bolts installed. I also added a bunch of details to the Central Support/Nut because there wasn't enough to paint when everything could fit under a 0.1mm square.. lol Dry fitting the rear-end of the Clerget reveals a lot of detail remains and most is clearly visible. I've still got one more 7hr print left for the engine stand, piston, master rod, cyl. head push-rods, rocker-arms and a replacement front case (you can see a chip in the second photo). Hopefully everything plays nice and sticks to the build plate properly cause I'm almost out of resin. -
Latina Sopwith Camel aftermarket build
zibbit replied to zibbit's topic in Work in Progress - Aircraft
Wow, I should probably provided an update to this thread. So I've been testing various Elegoo resins for resolution and dimensional accuracy. I've tried their Grey ABS-like resin, Water Washable in Black and Grey, and 8K standard resin. So far no significant scaling issues have been needed to correct for shrinkage on any of them; however, I've really spent a lot of time trying to dial in the right amount of exposure so I don't bloat the prints too much. If I do, I'll start to loose detail, which I don't want, or make parts impossible to fit together. Here's pretty much the synopsis of my work flow. make a print examine the print looking for any defects if a defect is found, try and solve why it happened. Usually it's just a matter of having to reposition the print and redo the supports. Proceed to step 1. Once no defects are found on the surface of the model, try assembling successfully printed part with adjacent components. Usually this results in finding fit issues with my clearances. Sometimes those issues can be corrected post-print with a file, drill, or sandpaper. Other times the model needs to be corrected first. If the problem needs CAD work, correct the model to account for my exposure settings, make a new STL, upload STL, support model, proceed to step 1. Rinse and repeat. It's a VERY long process. The bag of throw away prints is growing at an alarming rate. I will say, I have abandoned the thought of making the 1/16 scale model variant a cutaway. Instead I will focus that attempt on the 1/10 scale engine as the parts are a little more pronounced/substantial in size to make it not so fiddly to deal with. Anyways, here's proof stuff is being done, haha. In front is the 1/16, and the two larger throw-away assemblies in the back are the 1/10. As you can see, it is dimensionally accurate. The measurement I'm taking is supposed to be 300mm diameter full size, or 30mm in 1/10. You can also see the two magnetos are printed.. surprisingly the print on the cases show up. But, I doubt it would survive a painting process. Next up, I needed to design some sort of stand for the 1/10. So, I'm actually engineering a stand that's strong enough to survive the actual motor. This is my progress on that front. Ok, that's it for right now. I need sleep.