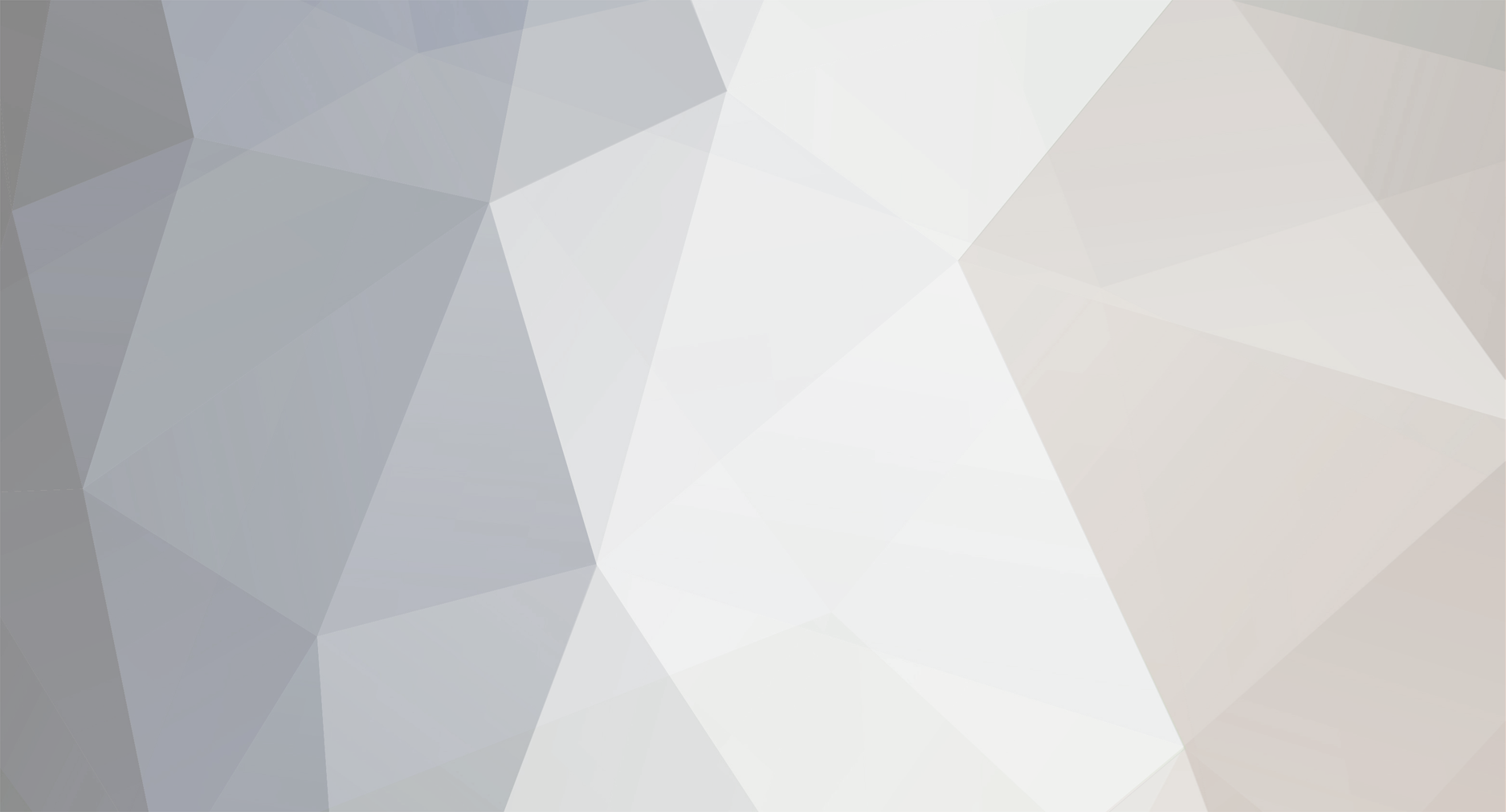
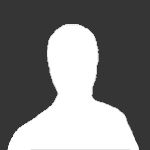
RabRoberts
Members-
Posts
105 -
Joined
-
Last visited
Profile Information
-
Gender
Male
-
Location
Brightons, Scotland
Recent Profile Visitors
732 profile views
RabRoberts's Achievements

New Member (2/9)
325
Reputation
-
No, it's not another abandoned project, just life gets in the way sometimes, but progress has been made, I think I'm done with the 3d printing part, it's mostly going to be assembling and painting, any other parts I need I'll likely make from scratch rather than printing. I reworked the engine block and cylinder heads and added cam covers, timing cover, re-designed the supercharger and built a transaxle. The end of the transaxle failed to print, but I'll just fill it with milliput, most of it will be hidden at the bottom of the engine bay. Yes, the supercharger on the real car is actually this big. Some clean up and a bit of painting, starting to look like an engine, I'll need to dirty it up a little. Finally got the body in primer, I am so rusty with the airbrush, there's multiple thick spots and runs, but I'll make the best of it and sand it out, hope to get some colour on it soon. Test fit for clearance in the engine bay, looks alright, I've had to cut away the wheel wells on the chassis to get the engine in the correct position. So there you have it, the project's still ongoing, just very slow, it's looking like the guy will have sold the real car before I finish the model, still it'll be a nice memento. Cheers - Rab.
-
Hi Ian, it is worthwhile and pretty satisfying to see it all come together, in hindsight I should have started with something simpler, smaller scale, less detailed and with no opening parts, but I've learned a lot. Your break off supports are a great idea, something like that would have helped a great deal when printing the tailgate section with the mesh, I'll keep it in mind for the future. As for thickening the parts, I used a few different methods. 1) The solidify modifier in Bforartists (presumably it's in blender too) it works best on simpler shapes, with tight radii bends and complex cut outs it can cause intersecting faces in the mesh. 2) Selecting the faces on a certain plane (i.e. all the faces that make up the roof surface) switch to edge selection and extrude edges, this does mean that you need add faces to the extruded edges and you're left with redundant geometry between the original faces and the extruded edges, but it's a relatively quick way of adding thickness to large surfaces that are roughly planar and it maintains the curvature of the parent surface. 3) Selecting the edges at the top and bottom of a panel and extruding, then connecting the extruded edges with new faces. This is quick and dirty, it doesn't maintain the curvature of the parent, but gives a flat surface, but this might be good enough on areas that aren't visible in the finished model. That's all I've come up with so far, none of the methods are perfect, other software might have more sophisticated tools available, but that's what I've managed so far using Bforartists/Blender. Cheers - Rab.
-
No new prints, but plenty of work on the fitting of the various bits and pieces, I need to make sure of the fitting before I start painting the body. Little winglets on the front wings, just made from plasticard, as I've said, sometimes it's quicker and easier to physically make the part. Testing the fit of the chassis, dash, body and sill covers, a bit of adjustment to the chassis to get it to sit flush with the body, the dash needs some adjustment and filling, as do the sill covers. Mesh over the radiator and fans is just standard mesh, no fancy printed parts here. Front and side intakes are printed pieces and the fit is surprisingly good. Once I'm sure all the parts will fit without modifying the body I can get some colour on it, hoping I can get it finished in under a year, but you never know. Cheers - Rab
-
Thanks folks, I can't believe how long it's been since I started this thing, I used to build a model a month. The insulated tent and heater are a game changer, it was 3 degrees outside yesterday and not much warmer in the shed, but the latest print was flawless. Supercharger, engine block and cylinder heads, I found a 3d model of the block online and made the cylinder heads and Supercharger on the computer. I still need to do the timing cover, cam covers and inlet manifold, but I couldn't resist blu-tacking it together. Rear engine cover Which sits in the engine bay like this. Of course, I had to stick the engine in too. The orientation is wrong because it's balanced on a usb stick, the real engine is rotated back such that the forward cylinder head is almost horizontal, that'll be corrected once I get the gearbox designed and printed. I also built the cone air filter and steering wheel. There's still a few small bits ans pieces to do, alternator, expansion tank, windscreen washer bottle, but it's getting there. Cheers - Rab
-
No new parts to show, I've mostly been sanding, we all know how time consuming that is. I have fitted the magnets for the doors which is necessary before spraying anything. The magnet in the door will be hidden, on the real car, there's a red reflector in this location. Blu-tak on the pillar and press the door against it gave me the location for the matching magnet. Superglue and baking powder on the back side to give us a bit of re-inforcement. With the sanding almost done and the doors mounted, couldn't resist mocking up the wheels to get an idea of how it will look. Getting excited now. Cheers - Rab.
- 44 replies
-
- 11
-
-
Thanks Zephyr. I'm quite pleased with the windscreen, it should look pretty good on the finished model, close to scale thickness and with a few coats of Future it'll be be nice and clear. Got some more printing done, I realised from photos that the rear diffuser and the trim piece below the rear bumper are actually connected so i redesigned the assembly and cut away the trim section from the body. The fit's reasonable, the gap between the diffuser and trim will be filled with mesh before spraying and the trim section needs some carbon decal. The front tyres have been reprinted, the wheels and tyres are actually concentric. I've also started on the tedious but essential prep work on the body. The usual, colour it with a Felt tip and sand it off. This image show why it's so critical with a 3d printed body. The 3d model isn't composed of curves, rather polygons (in this case triangles) and you can clearly see the outline mid-sanding. This would be horribly obvious on a painted, glossy finish, but it's not that blatant on the standard, grey, resin. It's also shown up a small depression on the rear wing which is either a mesh error on the 3d model, or a printing error, that'll need filled before painting. Cheers - Rab
-
Thanks Keith. Should be some more bits this week. Hi Pat, I know what you mean, I went into this rather naive, I am technically literate and I have messed around with 3d graphics in the past so how hard could it be? Turns out building 3d models for printing is not the same as doing 3d graphics, the requirements are quite different, then there's all the parameters involved in getting a decent print as well as the fact that the resins are mildly toxic. It's not straightforward at all, still worthwhile for me personally, but there are limitations and times where it's quicker and easier to just make the part by hand. Cheers - Rab
-
A brief update, after some tests, I got the exposure time for the black resin set and successfully printed a few bits and pieces. The tyres look pretty good, different widths and profiles front and rear. Unfortunately I'll have reprint the fronts, I made a mistake with the geometry and the wheel is slightly off centre, it's not obvious in the geometry or the photos, but in the plastic it's annoying clear. The MK1 eyeball is really good at spotting asymmetry is seems. Annoyingly, the resin isn't opaque, but slightly translucent, so my plan to not paint the grilles is a non starter. Reworked the seats, toning down the gloss and making the stitching look more like stitching. I also found some old matte aluminium Bare metal foil so I'm redoing the interior tub although I might need a matte varnish to flatten it a little. I'm also working on the decals, but the results with the ink jet aren't great, I'm sure I've had betters results in the past with a different printer, maybe oem cartridges would be better or maybe I'm just expecting too much. If anyone has any tips or has used a company to make decals any info would be much appreciated. Cheers - Rab
-
2 updates in 1 week, a new record. The insulated tent and heater was a qualified success, the new black resin failed to print anything, either I didn't shake it enough or I need to adjust exposure times for this resin. Switching back to the usual grey resin gave me this. Printed in the shed with the outside temperature at around 3 degrees, happy with that, it even kind of fits the wheel. I had been planning to just buy tyres, but the car has different diameters and widths front to rear and I couldn't find any sets that matched. The other thing that's been occupying my thoughts is the windows. Obviously 24th scale kits normally come with injection molded windows, not an option here. 43rd generally come with vac-formed or an acetate sheet that you cut to size. With nothing to lose, I thought I'd have a quick go with transparent sheet, the Exige windscreen doesn't have compound curves, so I thought I might get away with it. Time honoured masking tape to bridge the gap. Looks reasonable from the side. Handy template on a sheet of overhead projector film. Cut out and taped on the model and it looks pretty decent. With the roof on and engine cover in place, it's starting to look like a car. I need to order some tubes and rods for axles and to make the struts for the engine cover and the correct body colour paint has arrived so I hope to get some primer and colour on some of the parts pretty soon. Cheers - Rab
- 44 replies
-
- 10
-
-
Thanks Zepher full disclosure though, I didn't model the whole thing, it was based on a model from a racing game, albeit the earlier 4 cylinder Exige, it gave me the basic shape of the centre section, although the front needed a lot of rework and the rear was completely different. I know what you mean about there being too much good stuff on here,, it's impossible to keep up, never mind actually post or comment, speaking of which. Got the tailgate hinge working, complete with magnet to hold it shut, the magnet will be integrated into the wee storage compartment which looks like this. Just plasticard and foam board, no fancy 3d models for this part. Got the carbon decal on the roof. and the 2nd seat. and started painting the interior. There's been no printing as the temperature is hovering around freezing in the shed, but I have a solution, an insulated printer tent and a small heater should work. I've bought some black resin, so the plan is to print the tyres and re-print all the intake grilles which need to be black anyway, we'll see how that goes this week. The correct colour exterior paint Iis also on the way, maybe I can get some colour on the body and doors in the next couple of weeks. The suspension arms are likely going to be based on soldered brass rod, I can't see any way that 3d print would be strong enough, the other option would be to cut and carve from sheet styrene, we'll see. Hopefully more parts later this week. Cheers - Rab
-
Bet you though I'd given up. But no, after life got in the way for a few weeks, I'm back at it. The engine cover was never a great fit, even after sanding, it was too flat. Turns out printed resin reacts rather well to heat, so hot water then tape it down to the body and voila, it actually matches the curve of the body. I tried 3d printing the engine cover hinges, but they were too delicate to function, unlike the door hinges, which are hidden, they would be visible, so the time honoured "bent paper clip" technique was used. It needs to be trimmed and dressed up with putty to get the correct profile, but it works and I'm confident I can make it look nice. Ignore the blu-tak and cocktail stick. The chassis/base is well underway, I printed in in 2 parts as I didn't fancy waiting 8 hours to print it in one piece. The interior tub is attached and after some sanding and dremelling, it fits inside the body. I had to reinforce the rear with a piece of plastic and I've removed most of the wheel arches for now, but it's coming along. There's still plenty to do, I'm not entirely sure how to assemble it, and I've realised that 3d printing is not the solution for every part, sometimes it's quicker and easier to go old school and make the piece by hand, but it's a time saver on many parts. Some initial assembly soon so I can figure out how to put it together. Cheers - Rab
- 44 replies
-
- 10
-
-
A few more bits printed, I've been having some issues with print adhesion since I changed the fep so there's been a fair bit of wasted time, but I'm getting there. Brake discs, calipers and uprights, the plan is to have the discs rotate with the wheel while the calipers are fixed to the uprights. Mesh inserts for the front intakes as well as the intercooler and oil cooler that hide behind them. It turns out that all that time spent modeling the weird hex Mesh wasn't wasted, I could rescale it and use it here. I had to paint something as I was getting sick of looking at grey resin so I started with one of the seats. Seat with lines engraved more deeply and the back sanded smooth. Masking tape template for the carbon fibre decal for the seat back. Seat painted black, matt finish on the centre (the real car has Alcantara so I might flock it), gloss finish on the sides where the real car is vinyl. The red lines are where the stitching goes, it will be made more subdued and dotted later. It is out of scale, but true to scale would be invisible and I hate a model where everything is just black. I can always paint over it if it looks too big when I'm finished. Carbon fibre on the back, needs a little more micro-sol, but getting there. It's coming along, need to work on the tailgate hinges and the engine bay, maybe get some paint on the body. Cheers - Rab
- 44 replies
-
- 11
-