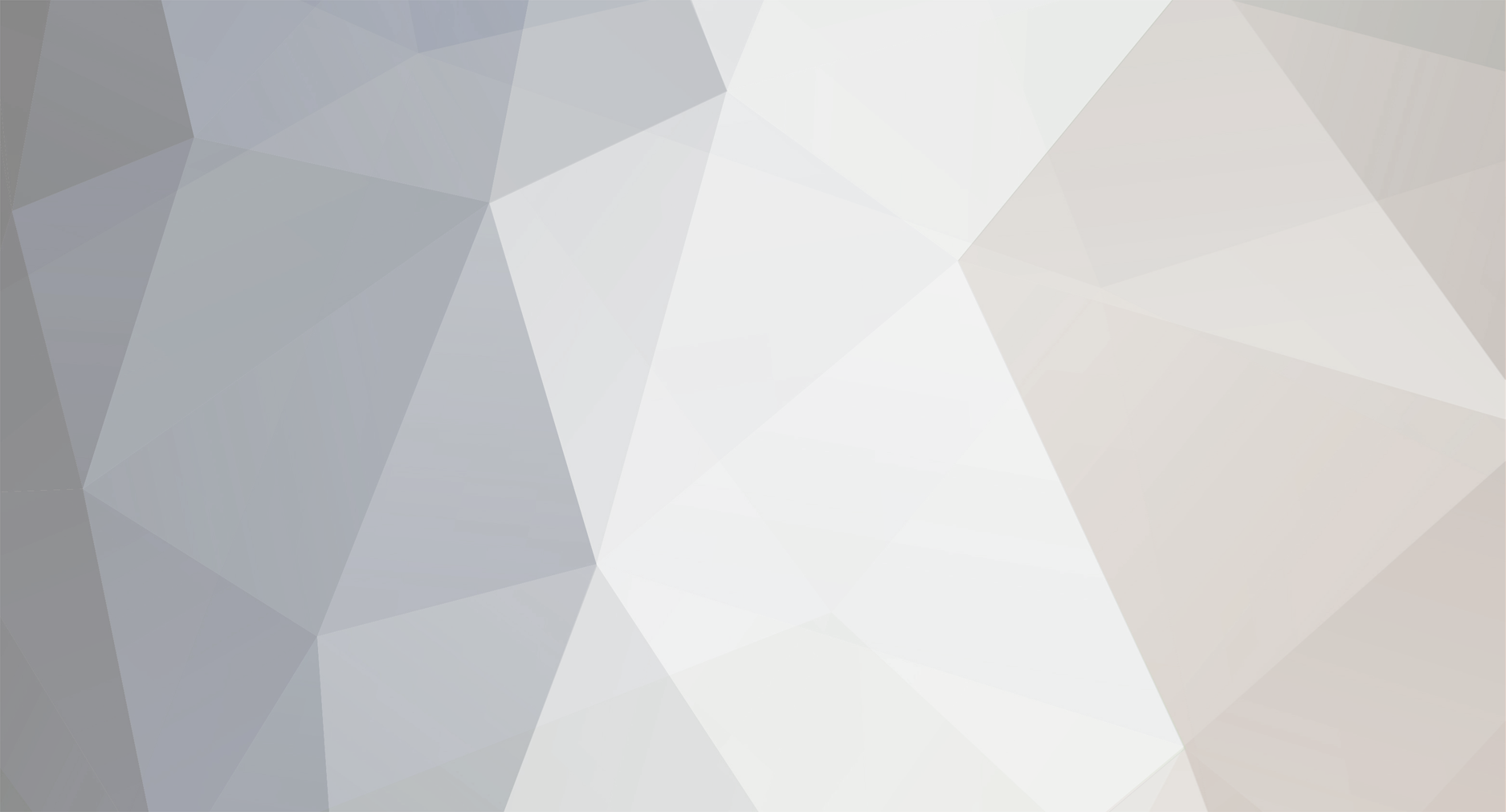
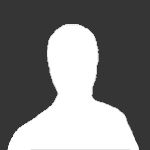
colinlp
Members-
Posts
46 -
Joined
-
Last visited
Profile Information
-
Gender
Male
-
Location
Anglesey
Recent Profile Visitors
The recent visitors block is disabled and is not being shown to other users.
colinlp's Achievements

Newbie (1/9)
14
Reputation
-
Thanks both. I don't think I could afford either, my pension isn't up to much sadly but that's no concern. I really want to build them myself, just so I can say I did no matter how they turn out. I'm still not in a position to build them yet, maybe another couple of months, I'm waiting for my cataract surgery to be over with. I have been thinking along the lines of using a PTFE strip to make a locating base, with some balsa uprights to hold a slotted PTFE tread locating strip so I can assemble before welding with plastic weld glue before turning it over to weld the other stringer on in a similar jig. Do you think that would work? My concern is capillary action taking up the glue and seizing it in the jig
-
Hi all I'm relatively new to modelling but I'm currently building a scratch build Apollo launch tower at 144 scale. I have 38 flights of stairs to make, each with a rise of 21.16mm and 14 treads per flight. I suspect 14 treads will be unrealistic and too crowded so I might opt for less. Each tread will be 6mm x 0.2mm x 2mm. What I need is some sort of jig to help me assemble them all accurately and all the same. That is where I'm lost and could do with some help, could someone give me an idea of how such a jig might be built and what materials that have no chance of getting welded to the parts Many thanks
-
Airfix 1/48 Hawker Hunter, 4FTS RAF Valley
colinlp replied to Mark's topic in Ready for Inspection - Aircraft
Very nice! I used to live at the end of the Valley runway in Rhosneigr so the chances are I saw the plane fly quite often, I remember the colour scheme well, nice to see again -
Thanks, sorry for the delay, been away for a couple of weeks. I've tried leather but it tends to stretch and come loose after an hour or so. There are ready made versions available but they are horrendously expensive and only come in a couple of sizes from the states with no returns accepted so I'm reluctant to shell out a small fortune on a chance it will fit. Another thought, perhaps I could use the rubber to make a mould of my finger and then cast a replica to send them, do you think that might be viable? I have no experience of doing anything like that
-
An off the wall question here but maybe someone can take a guess for me. I cut the tip off a finger a few years ago at the nail base, I also play bass guitar which is a problem. I made a thimble out of Polymorph a few years ago which has worked OK but is a little bulky and and sounds like a hammer hitting the string even with some leather padding. I've tried a few things over the years to make a better version but so far no luck. Recently I've heard of the rubber that can be used for moulds (molds?). Do you think it would be durable enough to be made quite thinly to peel on and off my fingertip without splitting? The tip would be protected by a leather pad so wear wouldn't be an issue. Sorry for the totally off topic question but i\ hope someone may have an idea, maybe as to a brand or type too Thanks
-
It's quite a project, I'm close to finishing the MLP. Currently I'm battling with the tail service masts, on round 2. I scrapped the first set as they looked awful, I tried to build them totally from styrene but either they were too flimsy or too chunky depending on what round section I used. So this time I've used brass and they're starting to look OK. Left to do before painting are pipe brackets, the removable handrails (using 0.5mm brass wire) and the stairwell cover. Looking forward to making a start on the LUT mid spring
- 25 replies
-
Apollo Saturn LUT by LVM Studios 2015
colinlp replied to roma847's topic in Work In Progress - SF & RealSpace
Yes the paint was a consumable meant to burn off as a form of heat shield but why the colour changes I have no idea either, The same seems to apply for the hold downs and tail service masts, they change colour frequently too. My finished model I want to represent the pre launch preparations so the hut etc will be glued in place as I don't want them to be lost over time Question here, those winches under the white covers, what was their purpose? I cant find a reference to that, I'm sure there is one but as yet it eludes me Sorry Manfred, I can't seem to copy the post and quote to take it to another thread. However I think the concept of either creating your own PE parts or finishing off with styrene now may be the only solution to finish the LVM model. I suspect an answer isn't forthcoming even if it would be the least thing to be done (I hope I'm wrong) -
Apollo Saturn LUT by LVM Studios 2015
colinlp replied to roma847's topic in Work In Progress - SF & RealSpace
Small things like the covers for the 4 winches on the MLP, there's a hut next to the lift blast shield on a few pictures on the MLP, some differences in pipe type work, the MLP legs. Nothing major but it would be nice to get it close to at least one of them -
Apollo Saturn LUT by LVM Studios 2015
colinlp replied to roma847's topic in Work In Progress - SF & RealSpace
That's exactly what I'm doing, I'm referring to as many pictures as I can as well because there seems to be many differences between the 3 launchers -
I'm in the process of building a 144 scale MLP and LUT Ken may I trouble you for a copy too. I asked for help with pictures in another thread a few months ago but it fell on deaf ears. I'll PM you if that's OK
- 25 replies
-
Apollo Saturn LUT by LVM Studios 2015
colinlp replied to roma847's topic in Work In Progress - SF & RealSpace
Your efforts are commendable Manfred. I really considered buying into this kit, I am so glad I opted to build a styrene version -
Oven temperature lower limit for bending styrene
colinlp replied to colinlp's topic in Scratchbuilding
Thanks, I don't think there is any need to rebuild, I remeasured this morning on a piece of thick glass and the wind is only 1mm which I can live with easily if I can't get the thing perfectly flat. The trouble is joining 10 90degree butt joints end to end over about 400mm is always going to have a little inaccuracy but maybe I should have used 2 or 3mm stock for the main surfaces but what I have is fine. Maybe the brick idea is a bad one, point taken. Hot water wouldn't work because most of the bracing is hidden inside and a good as sealed in hence the oven idea. Our oven is controllable from 40C upwards so maybe something like 60C-80C then remove and weigh down during cooling? All it needs is just enough to relax slightly and then hold its new position. I'm starting to think though that unless I get it quite hot, maybe too hot to achieve what I want -
Hi, help needed please I am in the process of building my 144 scale Saturn V launch tower. I have completed the basic shell of the launch platform which is basically a 50mm high box that is built from 1mm styrene with a series of cross bracing inside to support the surfaces. It has gone pretty well for my first attempt at scratch building but I have a small wind in it so whenplace on a flat surface it has a small wobble of a couple of mm. What I think I can do is put it in the oven with some flat plywood under and over with say a brick in top to add weight then hopefully it will slowly sag down to flat before I let it cool. Is this feasible? OK it wouldn't be that difficult to compensate but adjusting other bits to suit but it would be nice to get it flat. If it is feasible what temperature would you recomend for this so it doesn't end up in a free-form fried egg shape at the bottom of the oven? Hoping someone out there who has more experience than me has some idea, I have googled but I can't find anything useful at all Many thanks
-
Just an update on how I got on: I bought some Vallejo Model air paints, thinners and flow improver, I had a good play around and ended up using one drop of flow improver to 5 - 10 drops of paint at about 20psi. It worked beautifully, a good fine even spray pattern and no build up on the tip at all. The actual spraying turned out pretty good, the weathering affect I tried somewhat less so but that's just down to practice. Thanks for all your help guys
-
I've bought the Educraft paper models to use as a template and reference. Hopefully these along with the pictures and the drawings I have will be enough to help me proceed with the styrene model. Will probably build the paper version concurrently with the styrene just to get my moneys worth out of it