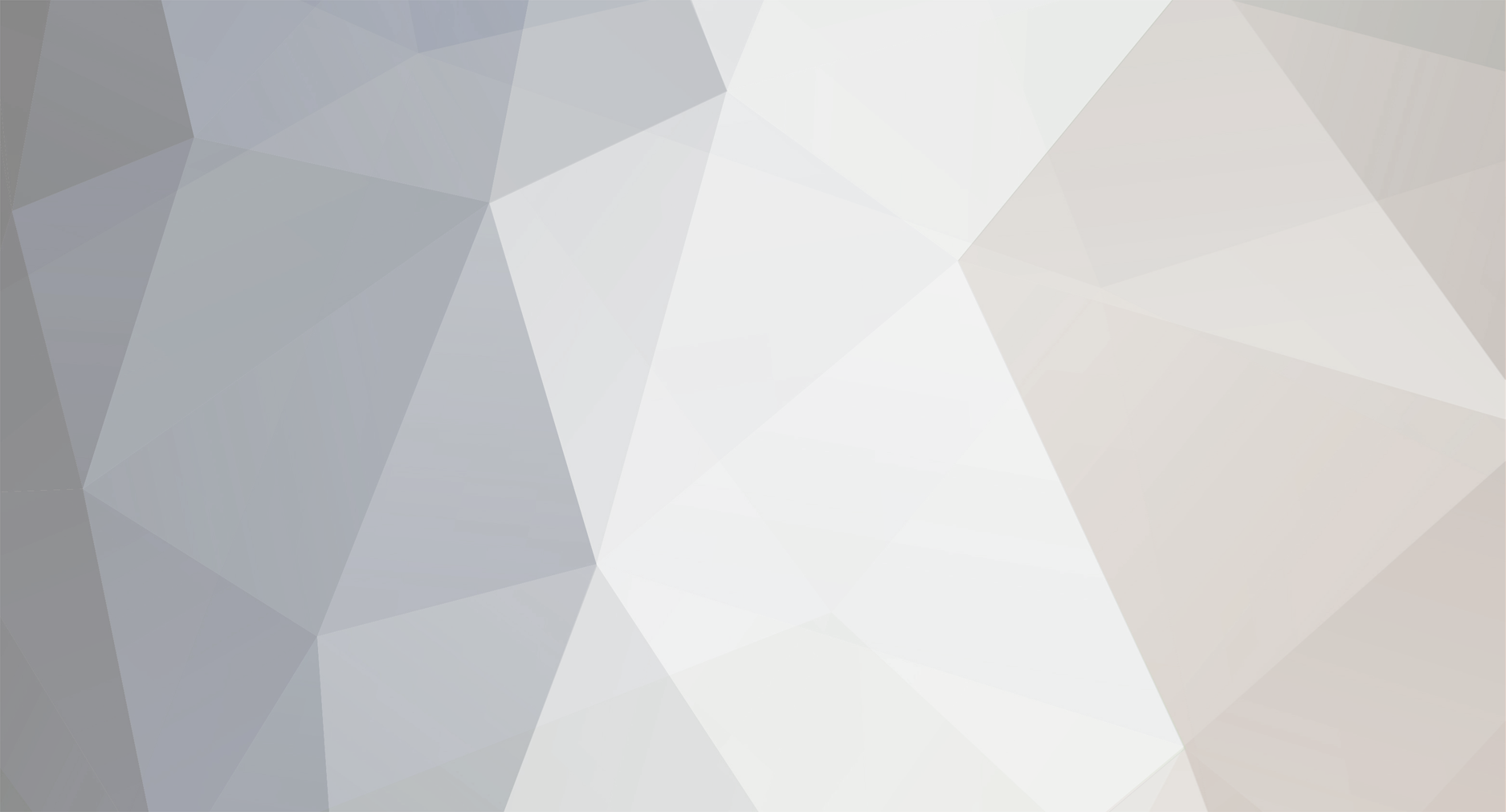
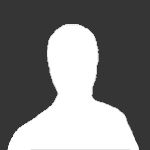
GMK
Gold Member-
Posts
1,110 -
Joined
-
Last visited
Content Type
Events
Profiles
Forums
Media Demo
Everything posted by GMK
-
Lol. Everybody loves the combat Winnebago.
-
Printed & assembled the building jig to get the truck off the deck. Starting to get a solid impression of what it’ll look like.
-
The clearing of the print backlog continues. The seat backs & mounts have been run up. The inward-facing seats have a large “wing” oriented toward the front of the vehicle to protect occupants from a sudden deceleration. So, left up the top, right down the bottom. With the mounts added to the lower hull, we’re left with this: Through the back door: The spare wheel mount was designed, printed, & mounted to the rear of the hull. Test fit with my spare wheel hub & the MRAP kit tyre: Pretty happy with the result.
-
Panzerhaubitze 2000, 1/24 scale, Scratchbuild
GMK replied to Bandsaw Steve's topic in Work in Progress - Armour
Steve - that is some serious work you’ve done there. Impressed with both your solution and perseverance. Great stuff!- 482 replies
-
- 1
-
-
- Artillery
- Scratchbuild
-
(and 1 more)
Tagged with:
-
Printed the updated radio rack & power distribution tower. These are located on the left side of the interior, behind the commander’s seat and in front of seats arrayed along the left side of the vehicle. Fresh off the printer, with support structures in place: Support materials removed (right). Radio rack to the left. The finish of the print will be improved using filler primer & sanding. Here’s a cross section of a failed print on the right. As can be seen, only the faces of the print are finished to a high standard & the bodies themselves aren’t solid. The amount of infill is determined before printing. Generally, I use denser infill for the structural parts & less infill for interior features. The aircon tower is on the printer atm, which will be located behind the driver on the right hand side of the vehicle.
-
Not much opportunity to get things done on the Bushmaster, lately. That said, managed to print the updated instrument panel, inclusive of the control screen for the remote weapon station, and have a crack at laser cutting the instrument panel shroud. Need to figure out why only the holes at the ends are cutting as ovals. The laser cutter is also getting a workout cutting the doors for the sponson stowage. Looking forward to tackling the interior prints & painting.
-
Looks interesting - and a nightmare to model!
- 62 replies
-
- 13
-
-
Thanks Steve, how’re the tracks going on your beast? End of the month update - have caught up from where I was at the start of the month! Now it actually looks like a Bushmaster!
-
Last week’s focus was the RHS stowage. The first iteration required ten prints due to size limitations of the first 3D printer (125x125x125mm). This iteration brought that number down to five prints. The underside of the bins had separate detail: Time for the LHS.
-
Panzerhaubitze 2000, 1/24 scale, Scratchbuild
GMK replied to Bandsaw Steve's topic in Work in Progress - Armour
Steve, That is hard core. Well done in problem solving. You’ve provided a glimpse into my nightmare future for a 1/16 M113! Keep up the great work. Cheers, Greg- 482 replies
-
- 1
-
-
- Artillery
- Scratchbuild
-
(and 1 more)
Tagged with:
-
Starting to learn how to use the laser cutter for thin parts. First hit out for the the 1,600 mW laser resulted in this: Test size cut of the windows went well. Need to work on cutting depth & number of passes.
-
Well, ten days later... Pretty hefty.. And a new floor.
-
Thanks Steve, appreciated. Here you go:
-
What little hobby time available this week was devoted to cleaning up the upper hull print & adding anti-slip. Other side: The anti-slip was added using Tamiya light sand textured paint.
-
First test fitting looks “workable with modifications”
-
Only 182 hours, it turns out. Upper hull print is done! With support material, it’s pretty hefty! Time for clean up and filler primer.
-
Looks like R08’s deck is getting a little crowded: RN Pic
-
A trial - but a massive increase in performance over the current F model Chinook by using T408 engine:
-
Well, the new printer with the enormous print volume has arrived. Lots to it! Got the printer sorted, less the enclosure. Time to print the upper hull. On my first go on the old printer, I had to divide the part into six pieces, inducing alignment issues. This one will be a single piece. Only 187 hours, 50 minutes to go!
-
Once the filler primer is finished, there won’t be much visible, Ray. The striations are a bit of a nightmare, though. Speaking of nightmares: tracks! Loving Xantho. Worthy successor project to AE2.
-
Thanks Steve. How are your projects going?
-
Started the design & test fit of the rear door. I’m finding jumping between parts helps prevent boredom setting in. Here’s the v1 design: Interior view: Here’s the v0 fit check print: Interior view: The tiny window & thick transparency will mean not much of the troop compartment will be visible.
-
A lot of work culminated this week. Most of the lower hull is all glued up. Very, very happy with how it’s coming together. Time to work on the interior.
-
Version 0 of the fuel cell for sizing & geometry verification. Probably get to finished the design by the end of the weekend. The square cut out is for the battery box for the crank batteries.
-
Lower hull is almost ready for final priming.