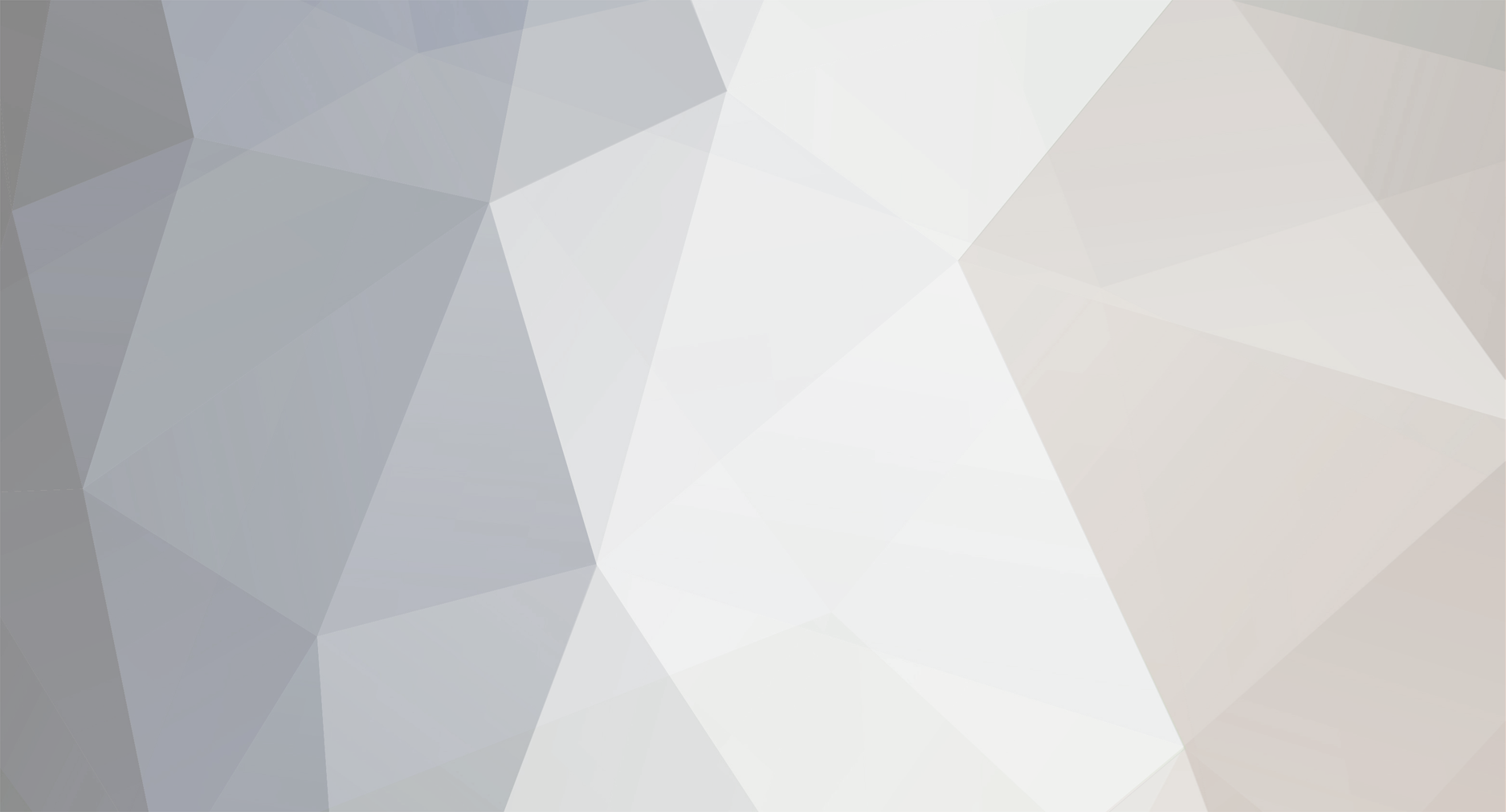
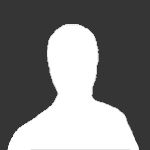
hugogo
Members-
Posts
102 -
Joined
-
Last visited
Content Type
Events
Profiles
Forums
Media Demo
Everything posted by hugogo
-
With the Hawkeye in the right colors I gave the whole thing a few layers of gloss varnish; 1 part Tamyia varnish, 1 part Tamyia thinner, 2 parts IPA to make the mix even more fluid. After each layer I removed dust specs, after 3 layers I let the lot dry for a few days. In the mean time my attention has shifted a bit towards the Super Hornets, 2 F/A-18F's for my diorama and another F/A-18E for a different project. For each of the planes I wanted to make the intakes a bit more realistic without spending too much time. Drilling out the blanked off intake and filing it neat was the least I could do: Only the bottom of the intake needs a bit of filler, no problem! With 8 parts you already have the main part ready: also filed off the rectangular lips to make the transition to the round duct smoother: Next step is the separation of the flaps: The parked Super Hornet also has its wings folded: and flaps that point downwards with the lack of hydraulic pressure: I also wanted to open up the avionics bays, and have these 3D printed: So...let the sawing commence! To give an idea of scale: the avionics bay is about 5 mm high... the housing of the nose wheel must make a bit of space it will be ok! also removed material for the front bays:
-
hi danieltomcat, that might be for a next project, this project is going depict a situation from 2009, when Tomcats had been replaced by the Super Hornet. But indeed it gives inspiration for another diorama! in the mean time, the solution for the color and the letters on the tail is becoming more and more elegant. With a handy website on the net http://scalemodeldb.com/paint you can analyse the colors used in a submitted picture. with the cursor on the tail of the Hawkeye I came to a color ratio of red:1 green:102 blue: 199. These colors I used to make a triangle in MS Powerpoint in the right blue color. with the white letters added on top (font size 13) it became more and more what I needed. A laserprint results in the following: after cutting some triangles I managed to make a sneak peek of what the tail could become: I think I will solve this puzzle!
-
I got some work done in the past few days, added more colors to the Hawkeye. With exception of the arrestor hook, all features have been painted now: de-icing boots on wing leading edge, 3 windows, anti-reflection zone around front window, black nose, air intakes and exhausts in silver and red flaps and wing parts. During the painting of the rear wings I came to the conclusion that the mounting of the vertical rear wing surfaces was not such a good idea after all, first the anti slip coating in decal form must be put on the rear wing. So I pulled them loose and repaired the damaged paint. Also the 3D printed props turned out nicely under a layer of dark grey paint: I borrowed this photo from SIMHQ to show the wonderful Hawkeye of VAW-121. Then about those decals, I systematically worked my way towards a solution: First downloaded a assembly manual of a large hawkeye, then added the lines on the tail of where the blue must come later: The font type of the letters AG I looked up in MS Word, it seems to be the itallic version of the font Monotype Corsilia, I reduced in size such that the letters are positioned about the same way as in real. After this I measured the angles of the lines, this seems to be 15 degrees almost everywhere. Looking at the size of the tail, the letters on my bird should become 2.7 mm high: Furthermore I mounted the engines in order to fill the gaps between them and the wing. Flaps and landing gear were mounted temporarily to dry fit:
-
Hi Phildageek, they are called decalwinkel.nl they are a print service that print decals with colored and white ink on a transparent decal. I figured out the font type of the "AG" tailcode and in this scale I don't think that painting it by hand will be successful. I have no experience of their product yet but we will see how far we get with 5 euro per A4 print. So what I am planning to do is to - design some blue triangles with the computer program 'MS paint', put the letters on top in white, - design the blue '603' code with white shadow on the nose (copied a nice drawing from the internet that shows the numbers really nice) See how this gets printed. It is all a bit of an experiment but hey that is what hobby is all about, isn't it?
-
Thanks James G! since the Revell excursion that the Dutch IPMS organized last week, I have fully regained my engergy to start doing something with paint again. Armed to the teeth with paint, brushes, masking tape (and of course some new kits), I have started to resume work on the Hawkeye. After assembly of the main parts and cleaning up the seems, I masked the windows and glued all smaller parts with some wood glue to wooden laundry clamps. With a bit of IPA on a cotton stick I removed grease and dust in preparation of paint. First layer was a thin semi-gloss white enamel as base coat. Did not make pictures of it since it was quite uneventful. This first layer enabled me to spot some areas that needed attention and after cleaning those up+ very light sanding for overall smoothness, it was time for a color coat. This light gull grey coat I airbrushed with a new paint for me which was AK interactive. Bought it at ESM last year, 8 small tubes with modern US navy colors in 1 box. After reading the instructions, I noticed that the paints are described to have a 'scaling'effect in them, which I think means that they are a bit lighter than the real color. Because of the small scale, I decided to mix the paint with 20% white anyway. This mix was then diluted with 20% Revell aqua thinner and 20% IPA to make the mix even more liquid. It was a bit of an experiment but I was satisfied with the result: Though the brushing goes much quicker on this small surface than I am used to, it is a real challenge to keep the layers thin and to keep a smooth surface! In the mean time I also thought about how to customize the decals that I heed for this bird. I think I will order them via a print service that can print decals with white ink. Some day you will read about it in this article!
-
Hi GMK, short: no I don't, for my own modeling purpose I was mainly interested in the catapult area. But knowing now the trick with the tie-down counting, I am sure that if you find the right photo (and not all carriers have the helo signs during all era's) then you can figure out its location and size. I would be interested how that went if you decide to pursue this one! and thank you Mr. B for the compliment, I am quite patient but also do not have a lot of space at home. My strategy of dealing with this is to make my projects more complex and time consuming than necessary
-
here is a short update: My initial idea of making the catwalk from PS strips started with a quick set-up in CAD of the main features, but ended in a plan to have the whole catwalk 3D printed. And after a few evenings of drawing, this is the result. The containers with life rafts have not been shaped exactly but at least I have an idea of size and position: This piece of catwalk forward of elevator 1 will be printed as 1 part and will measure 20 cm long x 2 cm high, smallest feature is the railing of 0.3mm diameter. Only the side and underside of the ship's extension will become PS. Will be continued!
-
thanks for all your encouragement, especially since I have decided to enlarge this project slightly. I'll let you know what happened. last week I still had the intention to dirty up the flight deck or to put my Hawkeye in some base coat, but in the mean time I have been distracted with something different: one of the edges of my diorama is also he edge of the carrier deck. What I always found impressive is that the aircraft are sometimes parked with the tail sticking over the edge of the deck. Because it seemed odd to me to just put my aircraft over the edge of the diorama, I started to get the idea to add a piece of catwalk. In order to see what this part looks like I have visited the carrierbuilders.net homepage and there I found a wonderful photo of Harry S/ Truman: http://carrierbuilders.net/articles/20060216_CVN-75_WA_Pt_2/160.jpg That would be a nice addition to my diorama, and not impossible to build too! To the DIY shop I went to get some wood, put something together and glued it to the base plate: so now my dio also has an overhanging deck! With pieces of PS sheet and strip I will add other features, not sure yet how to do the railing (wonder whether these are sold in PE?). My project just grew with a couple of months!
-
hey Orion, those figures turned out ver well indeed, and what a nice looking tracker! Congratulations with the overall result, I hope to see them in real life in October? Hugo
-
during the last few days I managed to complete the lines on the deck. After the parking lines I masked all the yellow-red lines. it cost me a whole evening to put all 250+ pieces of tape in the right location! then first a coat of yellow: and then red. Finally the white lines around the hatches. I also discovered that the Eisenhower has the parking lines a bit longer than any of its sister ships, so I masked these again: and then we have a brand new carrier deck!! Next thing is to put a layer of gloss varnish on top to protect the paint, and then I will make a start with dirtying things up a little. Because there is no such thing as a clean carrier deck!
-
this week I found some time to start with the deck lines, First I put a few varnish layers on the deck to protect the color that I already applied. After a light sanding with 2000 grit sanding paper, I decided to paint the parking lines first. Made 0.8 mm wide lines by sticking tamya tape on either sides, then created 10 mm spaces for the red-white colors: applied white paint first. In this case I used Revell aqua color because it dries fast, enabling to do the red immediately after: removed the tape covering the to-be red parts, moved them over the white lines: put some red paint on: and then, ever so slowly, removed the tape. A wonderful red-white line appeared! and there we have the parking lines done! :
- 129 replies
-
- 13
-
-
I got some work done tonight, painted the catapult track and the manholes in the deck: next step for this one will be a different shade of grey for the JBD and then a layer of varnish and thereafter the lines on the deck. Also made progress on the hawkeye: Put the pilots in! But then I noticed that they are sitting quite far forward... and with the canopy on, it really stands out DISAPPOINTMENT! What to do now? I did not manage to pry open the nose and take the hole cockpit floor out. Then I decided to remove the pilots, simply break the back rests off of the chairs, then glue the back rest against the back of each pilot and glue the pilot in the right position. It is not pretty but it got the pilots looking out of the side window again.And except for the pilots you won't be able to see anything inside anyway. As a bonus I decided to rearrange the dashboard to its right location too: The rest of the wings and parts fit quite well, just a smear of putty in some corners: and a bit more on the upper wing. Notice the flaps that I cut out to be repositioned for take off: that's it for now!
-
indeed it is SLA, layer by layer resin 'jet' printing with wax 'jet' printing as support structures, followed by UV hardening of the resin layer. A likely reason for no figures being commercially available in cast resin is probably the delicacy of the thin shapes like arms and legs. Even though for most parts a single 3D print is (for now) much more expensive than a resin cast, I think that in this area of tiny, highly detailed shapes, a 3D printed product can earn a good place in the modeling market.
-
thanks eamonn, Phil, MontasB for the encouragement, I needed exactly this bit of stimulation to pick the project up where I left it and painted the Jet Blast Deflector screens and some other stuff, more pictures to follow! Yes Tony I agree with you, if you consider resin parts and photo-etch an enrichment for the hobby, so is 3D printed parts (btw a lot of resin part manufacturers make their masters from a 3D printed part nowadays). On top of that there will be a time where everyone can make or customize designs to their own liking, instead of buying only the things that manufacturers offer to you. And until parts are printed in color, there is still lots of paint and assembly work to be done, which is good for the hobby! Updates will follow!
-
today I completed the carrier deck crews I have been working on. From back to front 1:32, 1:48, 1:72 and 1:144. I have had my dose of figure paiting for this year. Next will be some progress on the Hawkeye!
- 129 replies
-
- 11
-
-
carrier deck crew for modern aircraft carrier in 1:350
hugogo replied to hugogo's topic in Work in Progress - Maritime
Hi Despy and Woodstock74, that could be an interresting project indeed. Is there any ytpical dress that modern submariners would wear? Pictures would be welcome. I already have guys in overalls, caps and life vests so I think I could make something and show it? -
Last weekend i had the time to paint the Hawkeye crew. I decided to give them a desert uniform in order to have some contrast with the vest. This is how it turned out. Next is a gloss varnish and some shadows/highlights:
-
carrier deck crew for modern aircraft carrier in 1:350
hugogo replied to hugogo's topic in Work in Progress - Maritime
had some time this weekend to test my patience...painted the 1:350 carrier deck crew: I'm getting cross eyed after a day of paiting these small figures! -
carrier deck crew for modern aircraft carrier in 1:350
hugogo replied to hugogo's topic in Work in Progress - Maritime
Hi Colonial! that would look like a fun challenge to model! Seriously, would you like to have that in a particular scale? Pls send me a PM if you like, it could be a fun project to make... -
after almost getting crazy about painting 30+ figures, I managed to finish all highlights and washes yesterday. Final step is a coat of flat varnish overall al then reapply gloss on the helmets and goggles. This is how they turned out so far: in 1:144 scale but also in 1:72 scale: and 1:32 I feel the urgent need to start building something like a carrier deck or simple, straightforward navy jet!
-
carrier deck crew for modern aircraft carrier in 1:350
hugogo replied to hugogo's topic in Work in Progress - Maritime
Hi Jockster, indeed, Harquebus beat me to this remark, indeed there is a gentleman with a Shapeways shop that is much more into WW2 figures than I am. I cannot judge about quality or price but if you want to go for WW2 figures he is probably the guy to contact. As far as figures in 1:700 goes: I was already surprised that the 1:350 figures worked out. With the current state of the art I do not see this happening now! -
carrier deck crew for modern aircraft carrier in 1:350
hugogo replied to hugogo's topic in Work in Progress - Maritime
Hi Paul, that is great feedback, thanks for you update! Yes I see your point about the weak spot being the ankles, the trick is to design the lot such that the parts don't come off at Shapeways, in which case you surely end up with an incomplete set, but do come off if and where you really want them to. What I had in mind is to cut off the material around the feet and them sand the remainder under the shoes with sanding paper. Would that help? Another tip for you hopefully: just let the lot soak in a jar with IPA for 10 mins and move each print around gently with tweezers. The wax will dissolve automatically, no rubbing needed. Last but not least: I might have a trick to add more figures in 1 set which I would like to try, so let me know before you order? The thing is that the max file size of any 3D print is 64MB and that limits the amount of figures that you can have in 1 set. The more figures I can cram in 64MB, the cheaper each figure gets. If this works then you can also let me know which figure you would like to have as extra in the set! As far as different poses and outfits; each figure costs around 1.5 hours to design, so doing this as a hobby makes it quite difficult to put a time limit to the availability of new figures. But by all means if you have photo's of a guy that you would like to have a figure of, please send it to me and I can see what I can do! hugo -
carrier deck crew for modern aircraft carrier in 1:350
hugogo replied to hugogo's topic in Work in Progress - Maritime
Hi Ex-FAAWAFU, I think I saw that come by. It would mean a lot to me if you would share your painting efforts on the forum, I have not started this endeavour myself yet! Good luck with them. -
Hi Kirk, the file must be sent to the printer in .STL (stereo lithography) format. If your CAD program can export it this way, then you can upload this file to Shapeways or any other printing service on the net. What you need to keep an eye on, is that you do not make cavities in your model, where the resin cannot go out of anymore after printing. The model can be multiple primitives, as long as they touch or slightly overlap. I had a model once where 2 primitives were 5 mu away from each other (my mistake) and the 3D printer printed them separated. Each loose part that you want must be a minimal dimension tall (I think it is a cube of 3mm). There is also a rule of thumb for minimum wall thickness, rod thickness etc, see the Shapeways website for guidance. Of course, connecting them via some material also prevents parts from ending up missing. Finally, if you upload your model, the model is calculated via FEM to check for printability. This gives you quickly an indication if you need to improve your model or not. I hope this helps!
-
carrier deck crew for modern aircraft carrier in 1:350
hugogo replied to hugogo's topic in Work in Progress - Maritime
Hi Mike, I must say, doing the figures in 1:350 scale is actually a spin off of the same figures in 1:144, 1:72, 1:48 and 1:32 scale that I already made. I started to make them for myself, for my own diorama's because when it comes to US navy carrier deck stuff, there is not so much out there and I was tired to buy the same Fujimi crew over and over again. Still having plans to design the open avionics bays for an F/a-18F in 1:144, and some tractors and weapons trolley....on top of all the kits I still need to build....wonderful hobby isn't it?