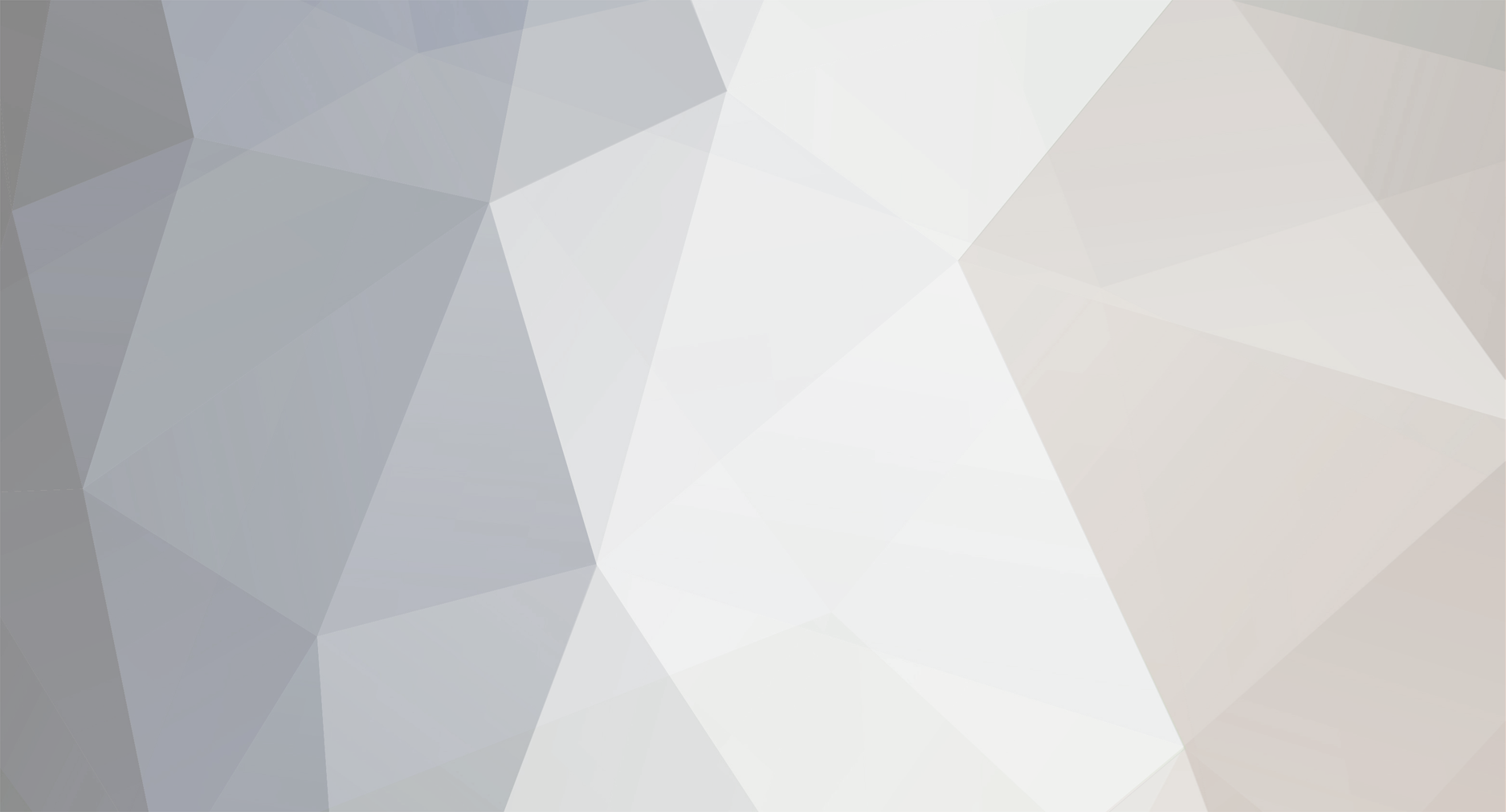
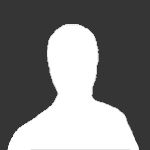
mnord
Members-
Posts
68 -
Joined
-
Last visited
Profile Information
-
Gender
Male
-
Location
Stockholm
Recent Profile Visitors
The recent visitors block is disabled and is not being shown to other users.
mnord's Achievements

New Member (2/9)
266
Reputation
-
Work has continued with the stabilizer. 5 mm acrylic sheet was used as a base which was then sanded to shape. Since the elevators always seem to drop a little on the "real" aircraft I decided to separate the elevators from the stabilizer. It turned out to be a little more tricky than expected to make this right but in the end I managed. Below the final result with some primer added. All the surface details will be added later. Since I now have the rudder, stabilizer and wings I laid everything out to get a teaser of what it will eventually look like, and also for the first time get an impression of the real size. A lot of work left but the main building blocks start to settle. The nose section will be done at a later stage. The cannons will be mounted to the wings and thus they need some holes to fit in. The original idea was to rig the wings up and simply bore some 3 mm holes, but (as so often before) I needed to change strategy as it turned out too difficult to drill with such precision. Instead I made two blocks in styrene, drilled the holes in them and then faired them in. They were first measured out. Then the styrene parts were mounted. The cannons will be turned from brass, but since I haven't done that yet I made the creative solution to use 3 mm drill bits to help out with alignment. The styrene was first fixed with epoxy glue to allow for some adjustments during hardening, and the gaps were filled with CA glue. And, as a last step, it was all sanded into shape. The small part is for the pitot. A little more work than first expected but that seems to be the rule throughout this project ๐
-
I'm using the machine below for vacforming. They are all over ebay and are not the expensive, around 150 euros I believe. If you stay within its limits it is good, for example with the styrene plastic I'm showing above. For sturdier materials, like the transparent acrylics I have been using for the cockpit canopy above, it has been slightly more challenging. The heating element can not be adjusted neither in height nor in temeperature, so it has been overheating a lot of acrylic sheets for me before they got soft enough for forming. To get a softer and uniform heating of acrylic I have been using the kitchen oven, and then quickly moved them over to the machine. The vacuum pressure is just enough for this - 1 mm acrylic works ok, 2 mm works with some effort, but also works. But this is kind of a stretch. For softer and thinner plastics like styrene or PET-G it will work just fine, as long as your parts are not bigger than the 5-6 centimeters that fits inside the frame ๐
-
Once the wings were ready they should be completed with ailerons, flaps and wing tips. The wing tips were easily made from acrylic (I had to laminate two parts to get the correct thickness) which was CA:d to the wing and then sanded to shape. Then it was the ailerons. The reason they were not shaped together with the wing was that I wanted to achieve sharp edges on the ailerons. something that is hard to do with the wooden core used for the wings. In retrospect this was a mistake since fitting separate parts was a -very- tedious job, especially since the geometry of the ailerons (different on the upper and lower side) was different and a bit hard to understand from the drawings I had. Next time I will do the full wing in one go and then cut out the ailerons instead, leaving only the connection to the wing to solve (and the very edge of the ailerons, which should be sharp, is easily achieved by CA:ing a stripe of acrylic to the edge). But this time I had to do with the chosen approachj :). I started off with the acrylic pieces below and needed to somehow make them into ailerons / flap with a nice fit. A few failed attempts followed. Once I figured out the shape (it's an L-shaped profile facing the wing) I needed to figure out a good method for making them. The belt sander didn't have the precision for the L-shape and shaping plastic parts this long and thin gives you warping problems. After some failed attemps with laminating sheet plast etcetera I finally succeded with pieces of 5 mm acrylics, were the forward L-shape was done with a milling machine and the rest was formed with the belt sander. Making the aileron and flap two separate parts introduced an additional fitting challenge (although manageable) but omitted the warping problem. The wing edges needed to be adjusted to take the ailerons. This was done by taking a deep breath and run the wings through the milling machine. The full length of the wing could just precisely be supported by the mill in one go. The aluminum profile under the wing provided some sturdiness to the whole setup outside the small milling board. End result: And, finally everything could be fitted together. Fine tuning between the wing and aileron was done by shimming with sheet plastic. The part that stretches beyond the wing is intentional. It should continue under the fuselage and is one of the parts where the shape caused some headache. Surface finish is still very rough, but that together with surface details will be handled at a later stage.
-
Wings... have to be done. Fortunately they are quite easy on the J22, with straight lines. I decided to go for polyester resin on top of a wooden core, so I basically started to cut out basic shapes from 4 mm plywood. The 4 mm looked thick enough at a first glance, but at a second glance I realized a lot more was needed, so I laminated two 4 mm for each wing. Some templates for each end of the wing were done from plasticard and once they were measured to place it was time to let the belt sander work. And, it actually had to work quite a lot. Below is the port wing with a pretty much finalized shape compared to the not started starboard wing. Along the way everything has to be doubled- and triple checked, both wings internally against each other and against the blueprints. The wingtips, together with the rudders, will be shaped from solid plasticard or acrylic and are saved for later, but getting the rear of the wings correct against the rudder area was a bit tricky. Eventually the wings were covered in layers of polyester resin, sealing the wood and providing a plastic surface for panel lines and details. The polyester resin is quite easy to work with once dried (applying it is a mess, however, and it is nasty stuff, so take precautions) but still some filler was needed for some bubbles in the end. A plastic strip was added to the area which will meet the rudder, and sanded to shape. Halfway done! No time for the wingtips and rudders, and then everything should be fitted to the fuselage. More to come ๐
-
Trying to finish off the interior so the next thing was the seat. The seat started off as a wooden plug which was used to vac form a basic shape. Some cutting, filing and sanding later I had something that resembled a seat. Some wire was added. Unfortunately I had to shim the bottom a little since I'd been to aggressive in the cutting and I managed to melt part of the bottom in the process (the plastic was very thin here). Fortunatly, though, it seems like the original seat had some kind of cusion. I doubt this a little since I only have one full picture of the seat which is from a non-flying museum plane and I think the normal was to sit on your parachute, but I chose to believe as it was actually the only picture, and I needed something to cover the melted part. The cusion had a quite sloppy fit so I formed a couple of them with milliput and then tried out the best. Seat belts were done by adding tape over kitchen foil from which stripes in the right dimensions were cut out. Holes were punched with a scriber. A part of 0,4 mm brass sheet was cut to form a headrest. The headrest was cut out from 0,4 mm brass sheet, rounded off and bent to shape. Everything was sprayed with interior green and the cusion and seat belts were sprayed with some mixture of yellow-white-green. After that it was assembled. The headrest is seen to the right. It had the corners rounded off with a file and the top part was bent. And, finally, it was all put in place. I see that all the edges in the cockpit and on the canopy are in need of some trimming now, but I will put all parts in place first ๐
-
So, scratch building obviously means redoing a lot of stuff. This time it was the rear part of the cockpit canopy that turned out to not make it. It was too wide and also I was afraid that the thin material (1 mm) left little room for adjustments. I decided to pull a new part out of 2 mm acrylics. Unfortunately this also forced me to review my vac forming process as the temperature span where the acrylics is soft enough for vac forming is quite narrow. Too much heat and the plastic will boil to vaste, too little and it will not form. Anyway, finally I got a decent new part, to the left in the picture. However, the part was still a bit too wide and it turned out that the problem was with the master plug. The master was adjusted, and rather than pulling an entirely new canopy (it use to take a few attempts before I get a decent one) I decided to heat up the existing one in the owen and just adjust it. The techniques are obviously many here... ๐ The new canopy worked out better, but the greater thickness of the material caused some struggle with the structure underneath it. Rather than doing everything new I adjusted what was - I expect / hope these changes to be hidden once the canopy frames are painted. The accommodations for the tailwheel required some surgery. At one point I carved out some space for the wheel bay and created a wooden plug which was used to vac form the area. A "roof" for the wheel bay was created but once everything is finished this area will not be visible. The position for the tail wheel mount was measured out and a brass mounting was turned on the lathe. It will definitely stay in place. The hatches were carefully measured and cut out. Some cleanup clearly needed, but overall good. The part was glued on and roughly sanded into place. With the tail wheel area and the rear part of the canopy in place the work could start with blending everything in, including all blemishes on the rear fuselage. Some automotive filler was used. A lot (lot, lot, lot!) of sanding later everything was eventually blended in. Not very evident from the picture, but now everything is actually super smooth and also the tail fin is now "one" with the fuselage. The canopy will be polished later, now it's time to continue with the forward fuselage part!
-
The instrument panel is in place, marking some kind of mini-milestone for the project, here seen together with all the dust accumulated in the process... The seat, control stick and throttle quadrant are still missing, but they are so to say off the critical path so they can be saved for later. The pedals are nowhere to be seen but they are actually in there, in the dark. It was quite a channel to find a way to mount everything together. Unfortunately no photos of that, but the solution was a mix of cyano, epoxy glue and pieces of bent sheet metal that was glued to the fuselage and act as mounting points. Let's hope nothing comes loose during the rest of the build! So now it's the time to fit some canopy. Frames need to be painted inside, so measuring everything up and mask it off will be the first task. The rear gap is intentional and will be filled with material of some kind, probably wood and polyester filler. The canopy actually has a pretty good rough fit, but this will probably require some effort until the next update.
-
Some pedals were made. The pedals themselves were cut and bent from sheet brass while the supporting stags were cut and sanded from plasticard, all four at once to save some effort and make it easier to make them uniform. The final assembly with paint. The stags could have been longer, but I don't think it will be noticeable at the end as their final location is quite hidden. So with all parts around the instrument panel area done it's time to assemble everything. There is not much to hang on to in this area of the cockpit, yet the assembly needs to be rigid. I don't want anything fall loose later on in the project... The "dashboard" was given a piece of sheet brass which will support the instrument panel. Then the "dashboard" was fixated. Some adjustments still needed where it meets the fuselage, but only minor stuff. More to come!
-
Well, this project has been pretty standstill over summer but now I have resumed the work with the instrument panel. A plasticard has been mounted on the back and some punched plasticards has been added to get the openings up to level. When the instrument faces are in they should be almost flush with the panel. This requires some patience but eventually it was done. This is the main instrument panel together with the two instrument boxes that should surround it, with some added details and ready for painting. The photo I made of the instrument faces turned out to be not worth the effort. The photographic film used is quite sturdy yet flexible, so it was hard to turn out nice round pieces (they ended up malformed in too many cases), and it also had a greyish tint that made it extremly difficult to actually see the dials once they were mounted. A clear, possibly thinner plastic was needed. I decided to simply print the dials onto a printable decal sheet and then apply them to a transparent 0.3 mm plastic sheet. The dials are lacking the high resolution of the photography but in the end, once in it's final place, this will not be very notable. The area around the instrument panel is currently blocking a lot of other progress on the project. Without it in place I cannot mount and fit the canopy, and without that I cannot really finalize outside work with the fuselage since the canopy is integrated. Hence, the pedals and the area on top of the IP, the "dashboard", needs to come next. The "dashboard" has a complex shape which more or less requires it to be vacuum formed. I made a master of hardwood, together with two other masters for a cockpit seat and for the tailwheel bay. The fourth part is for a 1/72 Hawker Hunter which started off as an "easy" side project to this one... ๐ This time the vac forming was an immediate success. Quite a different experience from the struggle I had with clear acrylic when making the canopy earlier. A very raw part, ready to be fitted in. ....and more or less done, here also with some added details. Black paint still needed, but that will wait for the moment. Next to come are the pedals!
-
The most prominent part of the cockpit is of course the instrument panel. The initial strategy was to drill holes in a thin plastic/brass sheet and put something resembling the gauges behind it, but recalling how hard it was to get this good during the build of my P-47 I reconsidered. I decided to instead mill holes in a thicker material and punch put some gauges which are then dropped into the openings, hopefully giving me some more control of the alignment. First the gauges, which were a little of a challenge. Although I had some images of the gauges themselves I couldn't first figure out how to get them to scale - my printer simply didn't have enough resolution for an acceptable result. But what if I photograph an overscaled version of the instrument panel on film and use the negative directly? That could be worth a try, and by coincidence I also photograph with an old-school (well, from the 1980s-90s) large format camera from time to time. An advantage here is that the camera focuses on a ground glass (what you see is exactly what you get, also the measurements) which means I can measure the real size of the instrument panel directly and photograph it to scale. I made sure to get a bunch of instrument panels on one 4x5 inch sheet and one trial version is shown below. The actual image is on the back of a negative so I will have the "glass" for free. Some white color painted behind accentuates the gauges. The holes are just punching tryouts - the plastic in the negative is quite sturdy so I wanted to make sure it's doable before continuing. Two new punches were turned to my home made punch and die set. Luckily only two sizes are needed, one is on the picture. The instrument panel ended up being milled and cut from 1 mm acrylic. Using a thicker plastic makes it more rigid and the risk of breaking anything when cutting the holes is mitigated. A few attempts were made and the version to the far right was the best. The holes for the big instruments turned out to be 2 mm, which was good since a milling bit could then be used for cutting. The milling bit puts a little less stress on the material than a drill bit does. The selected panel was roughly cut and then patiently filed down to the right dimensions. I refrained from power tools this time - they are faster, but one mistake and you need to start all over again... The result, ready for some extra detailing and paint before the gauges are being dropped in. As seen I had to shim one side a little in the end to get the measurements right.
-
The rudder got some 0.3 mm copper wire added in the groves that should serve as a "ribs". Everything was glued with CA and the wire was eventually cut to length. The trim rudder was also scribed at this stage. With the wire in place the rudder was covered several times with an automotive spray filler, then sanded down to give the impression of a framework structure covered in fabric. The trim rudder was defined once again and in the end I sprayed everything with some Tamiya primer to check the result. Below everything dry-fitted to the fin and fuselage. As can be seen both the fin and fuselage needs their share of surface/gap-filling work. However, there should be a smooth line from the canopy down to the fin, so in order to start I also need to fit the canopy, and in order to fit the canopy I better complete the interior first since the space left for this work will otherwise be very limitied. Hence I need to fix a chair, an instrument panel and a few other stuff... Well, it at least gave me a reason to get the interior parts I have so far into their final place. So, on to some milling, drilling and vac-forming (!) to see if the interior can get a little more busy!
-
Yes, it's a Proxxon BS/E. I have a dedicated holder for it which can be clamped in a vise, so I'm holding the part while letting the sander be stationary. In the beginning I tried the belt sander handheld but it was more difficult. I am actually looking for a bigger one that has a wider belt and a board to support more precise angles, so basically in the other direction from where you are looking. Probably you can make use of both Since I still haven't found the "right" belt sander (maybe a disc sander could be something) I'm continuing with this setup in the meantime. So far it has got the job done and it's not a too heavy investment.
-
The acrylic transformed successfully into a rudder, which is pictured below during one of the first dry-fittings with the fin and the body. The fin that I had attached to the body earlier had to be slightly redone as it ended up leaning a little and with somewhat wrong dimensions. The fin was skinned with 0.3 mm styrene sheet, and the whole rear area of the fuselage was formed into a "flowing" shape with some (careful) use of the belt sander. The rudder was in orginial covered with fabric. The frames underneath the fabric will be done in a classical manner with thin wire that is covered with either filler or cyano and then sanded into shape. Some groves were scribed for the wires with the aid of a spare piece of acryclic sheet which served as a ruler. A two-thirds finalized piece. Next step will be to scribe the trim rudder, which has been marked out, and fix the wire thing.
-
It has been a while since the last update and the project has also moved slowly during the autumn, but it hasn't been completely standstill. The cockpit turned out to be a little more time consuming than first expected, but now at least the cockpit side walls may get their final place soon. Time has been spent on creating boxes and wheels and also some custom tooling, mainly punches of different sizes of which one of the variants can be seen at the top of the second photo. Some work is still left - the three holes in the plate should for example get some kind of gauges in them - but the main painting and detailing has been done. The structure in the rear area of the cockpit, behind the pilot, has been completed together with the tubing framework that is visible around the cockpit opening. Some adjustments are still left. To get some variation in work I have in parallell started to look into the bigger parts around the fuselage, especially around the tail but also around the rear part of the canopy. The top of the fuselage should so to say follow one smooth line from just behind the pilot's seat down to where the fin starts, so it needs to be sorted out as a whole. First step was to align everything in the jig again. A surface gauge is used to mark out various heights around the fuselage and make sure that they end up in the same places on both sides. The canopy has some fitting issues at the bottom (not as big as it may seem in the picture, though, but it's still there). At the bottom of the fuselage the plastic had somehow "sunken" during the casting and created a dent. The white plasticard is there to build up the correct shape again. It has been roughly sanded but the final finish will be done later as this is not the only part where some finishing filler will be needed... The gap in the canopy is luckily below the windows, in the frame, so a piece of plasticard has been added also here. It will be sanded to shape and fitted before everything is being polished up. To position the fin some holes for guiding pins were drilled and the pins were glued The fin itself was formed from a piece of hardwood with the help of a belt sander. It's here seen dry-fitted and next step is to cover it with 0,4 mm plasticard. The rudder will be formed from an acrylic block, or at least that is the plan. I only had 5 mm acrylic which turned out to be on the thin end so two pieces has been glued together with superglue and is now waiting for the belt sander. Will get back with an update, hopefully in less than six months
-
On to the โbusy cockpitโ which isnโt less busy than it first looked. Currently Iโm working with creating all the boxes and parts from acrylic and brass. Measures are a mix of drawings and eyeballing, and as much as possible is created with the milling machine. The bigger crank on the lower left part here (which is the most complex part in the cockpit except for the instrument panel) was filed from a piece of brass, and a piece of brass tubing was cut to length to form the handle. After a first layer of paint: One of the most notable parts of the cockpit is the part of the fuselage tubing framework, which is visible from above on the cockpit sides. 0.5 mm brass wire was laid out in a pattern and then soldered. Some clean up and fine tuning left. The angles of the frame is correct but the fuselage is not - om the model the cockpit opening is widening a little towards the front of the aircraft. This is not really accurate since the original cockpit opening was almost square, but when I realized the error I decided to ignore it as it would be too hard to fix (and after all not very notable). The frame will be adjusted to fit the model of course, and also the small gap in the soldering will be sorted out.